在先進的隔離式封裝中使用主動式功率元件,有助於處理更高的功率,並大幅減少電路設計中的熱管理工作,從而克服大功率充電的挑戰。本文說明高功率半導體的先進封裝有效提升效率及效益的技術與列舉應用範例。
高功率半導體的先進封裝有助處理更高的功率
表面黏著功率元件(SMPD) 封裝為設計人員提供了功率性能、功耗及易於佈局和組裝的最佳組合,可協助設計人員克服挑戰,不用大幅增加系統的尺寸和重量就能提高輸出功率。
圖一展示了一種雙向電源拓撲結構,該拓撲在8個半橋組中使用16個碳化矽功率MOSFET。設計人員利用更多並聯的離散式功率 FET來實現更高的功率,將使充放電系統的設計變得更加困難。
離散式功率FET的封裝方式,通常是採用D2PAK或TO-247封裝。當設計輸出功率水準超過30 kW時,先進的封裝方式可提供所需元件以支援高輸出功率。
圖二顯示了封裝方式選項及其功率性能。每個封裝方式選項都會依據印刷電路板 (PCB)佈局複雜性、組裝難度、輸出功率和散熱量來評定。
SMPD封裝可實現更高功率密度
設計人員可以使用SMPD來容納各種電壓等級和電路拓撲(包括半橋)的各種晶片技術。圖三顯示了Littelfuse的 SMPD 的封裝範例。SMPD採用直接覆銅(DCB)基板,帶有銅導線架、封裝鋁線和半導體周圍的模塑化合物。
DCB中的裸露銅層可使連接到散熱器的表面積最大化。將銅導線架與封裝鋁線相結合,可以簡化焊接和組裝作業。DCB結構可提供高隔離強度,並允許在單個載體上採用具有高散熱性能的多個半導體排列。
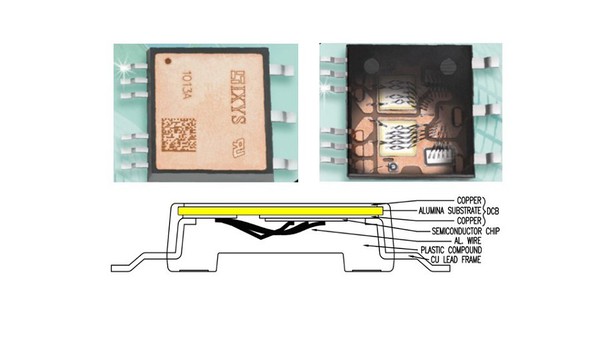
圖三 : 表面黏著功率元件(SMPD)封裝結構範例(source:Littelfuse ) |
|
本範例中的 SMPD 封裝設計具備多項優點:
‧ 可最大限度地利用半導體性能,以及低雜散電感的封裝結構形成的低電壓過衝。
‧ 在實現客製化的拓撲結構方面有更大的靈活性,包括晶閘管、功率二極體、MOSFET 和 IGBT。
‧ 由於具有背面隔離設計,所有功率半導體都可安裝在單個散熱器上。
‧ 與其它半導體封裝方式(例如 TO 型元件)相比,熱阻更低。
‧ SMPD 可提供比 TO 型封裝更高的載流能力。
‧ 半導體晶片和散熱器之間的低寄生耦合電容較低,降低了輻射EMI。
‧ 已獲得UL認證,額定絕緣電壓最高達2500 V
圖四中的每個封裝都包含兩個功率MOSFET,作為SMPD封裝中可用的多種電路配置的一個範例,突顯了SMPD封裝如何將元件數量減少近一半,從而實現更高的功率、更大的功率密度和更小的組裝尺寸。
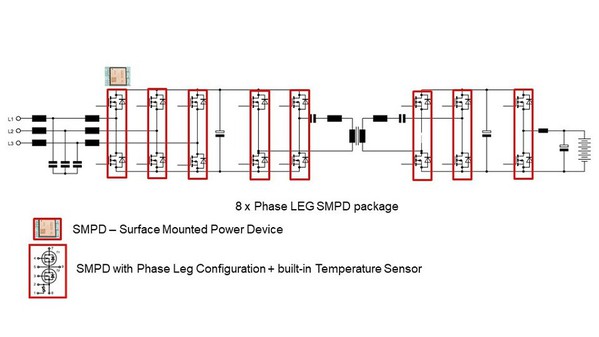
圖四 : 採用 SMPD 封裝的雙向充電器,與使用離散式元件相比,元件數量減少一半。 |
|
以更小的封裝提供更高的功率
設計人員可以提高充電器的功率以增加功率密度。它的用途很廣泛,比如電動汽車(EV)。
電動汽車的設計人員需要克服快速充電的挑戰,以最大限度減少車輛充電時的閒置時間,因此需要提高充電器的功率輸出、功率密度和效率。單個單元充電器設計範圍從 7 kW 到 30 kW。將單個單元元件組合成模組化設計可提高功率輸出,並使充電器製造商實現更小尺寸、更高的靈活性和可擴展性的目標。
在先進的隔離式封裝中使用主動式功率元件,可實現更高的功率密度並大幅減少電路設計中的熱管理工作,從而克服大功率充電的挑戰。
設計人員採用SMPD封裝,就能開發輸出高達 50 kW的單個功率單元,還可以減少元件數量來降低製造成本。例如Littelfuse的表面黏著封裝設計,可以利用低熱阻封裝方式的技術,從而最大限度降低散熱器的尺寸和成本。由於它的寄生電容和雜散電感較低,這種封裝方式可以降低輻射和傳導 EMI。設計人員可以使用更小的電感元件在高頻下工作,從而節省空間和成本。
(本文作者Martin Schulz為 Littelfuse應用工程全球負責人;Philippe Di Fulvio為Littelfuse電動汽車基礎設施業務發展經理)