延續多年來台灣工具機暨零組件產業發揮中部聚落優勢,不僅成立M-Team聯盟深化中衛體系聯盟;並在工業4.0、AIoT時代加裝智慧元件,以協助蒐集邊緣運算所需真實數據;以及為了追逐淨零碳排目標,落實以大帶小策略,提高工具機生態系價值。
其中因應全球智慧製造趨勢以及創新應用需求,在美國總統川普二度上任後,將續推動如鑽探油氣能源及國防軍工、航太等精密加工領域發展,促進高階大型五軸、複合加工機種商機。
根據2023年由台灣工具機暨零組件工業同業公會(TMBA)偕同財團法人精密機械研發中心(PMC),自2024年度開始攜手產、學雙方,共同投入開發「工具機智慧零組件關鍵技術」。並針對台製關鍵組件智慧化的性/價加值議題,邀集6大關鍵組件及整機廠業者為期數週的集思廣義下,彙集並列出工具機業界至今極為關切的智慧化議題,及其意欲跨越的挑戰門檻。
除了藉此提升零組件性能,以推動台製產品往高階工具機定位邁進;進而整合硬體設計與智慧化模組,以替代進口零組件為目標,分別在零組件和整機加工應用上加入智慧化功能,包含:自適應、監控、預測診斷等在產業落地。另透過建立性能驗證與標準化測試平台,持續進行工具機零組件可靠度驗證,促進台製工具機掌握高可靠度、高值化等優勢。
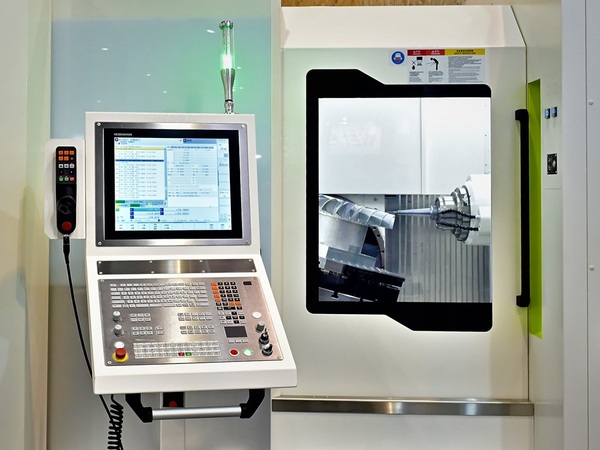
圖一 : :因應全球智慧製造創新應用需求,將促進高階大型五軸、複合加工機種商機。(攝影:陳念舜) |
|
替代進口智慧主軸 加速導入高階複合工具機加值
其中基於現今高階複合加工機,必須搭配長度較短、具備高轉速及轉矩特性的主軸,卻往往因為台製品的剛性與散熱不佳,無法針對緊密空間找出客製化最佳設計,導致台灣工具機廠商多數仰賴進口,不利於售後維修服務。
零組件廠也因為在產品優化設計過程中,須將(軸承跨距)剛性與(流道參數)散熱優化分開分析,難以綜合考量兩者之間的相互影響,常須要多次迭代計算才能找到平衡,導致客製主軸開發設計及測試週期時間,往往長達9個月。
直到2024年起由PMC引進「內藏式主軸流固耦合設計最佳化分析」技術,發展台製高效客製化主軸,將同時計算不同參數與剛性、溫度敏感度的關聯性,快速針對工具機廠目標需求調整參數,有效提升剛性37%、降低溫度12%;進而增加主軸剛性及散熱效率,減少加工中振動,而提高加工品質及效率。進行工具機零組件可靠度驗證,促進台製工具機掌握高可靠度、高值化等優勢。
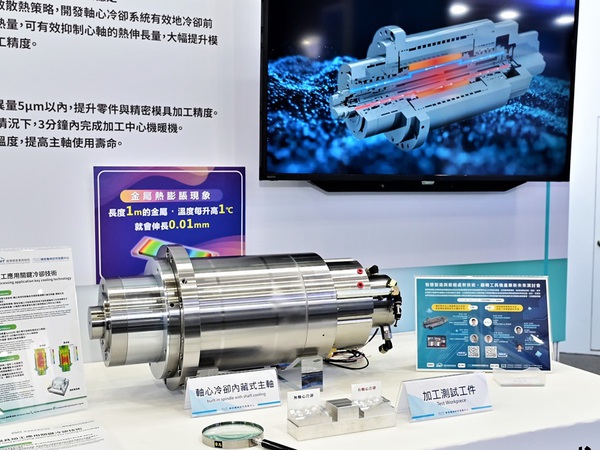
圖二 : :2024年起由PMC開發自製高效客製化主軸,將同時計算不同參數與剛性、溫度敏感度的關聯性。(攝影:陳念舜) |
|
零組件廠也能透過多目標設計最佳化,綜合考慮剛性和溫度反應結果優化設計,有效縮短產品開發優化時程至6個月已內。預期內藏式主軸產品的銷售占比,將由原40%提升至50%以上,可望滿足航太、汽車、醫療等高階加工市場需求,協助打入國際高端市場。
對於總體工具機與零組件產業,則預期將提升台製內藏式主軸銷售比例10%,產量年增500套、產值提升1.5億元。若能降低Maker端對於進口主軸的依賴,估算可降低成本約30%;End user金屬加工業,也能提高主軸剛性、材料移除率,縮減單件加工時間。
2025年工具機廠商更因為近年來受到供應鏈瓶頸及客戶提高庫存備料需求,勢將更為壓縮原來可停機保修時間,主軸軸承健康指標及預知保養,即是工具機智慧化的關鍵所在,過去軸承損壞的主因,常見於潤滑不當和污染問題。
然而,現有潤滑系統通常在設計階段,即設定如供油間隔和供氣壓力等固定參數,無法根據實際使用情況,如轉速變化等動態調整,可能導致潤滑不足或過量,PMC更為複合式緊密高性能內藏主軸,開發潤滑參數優化與狀態監控技術。
如今則可通過感測器進行實時監測並反應潤滑狀態的變化,如潤滑劑不足或過量的情況,減少了軸承的磨損,從而延長設備的整體使用壽命,預期可使產品產值增加約5%的收益。進而快速優化潤滑參數,可依據主軸轉速狀態,自動調整油氣供應,以維持適當軸承潤滑,精準控制潤滑油的用量、優化使用效益,減少浪費潤滑油10%以上對環境的影響。
包括台灣主軸大廠普森精密主軸工業公司(POSA),也已推出可內建(選配)各種感應裝置的智能化高速內藏式主軸,針對影響主軸加工精度的溫升或振動等因素,提供監控並掌握即時狀態的解決對策;同時開發「遠距離主軸異常檢測技術」,並建構高速主軸的異音、壽命及缺陷檢測分析模型。
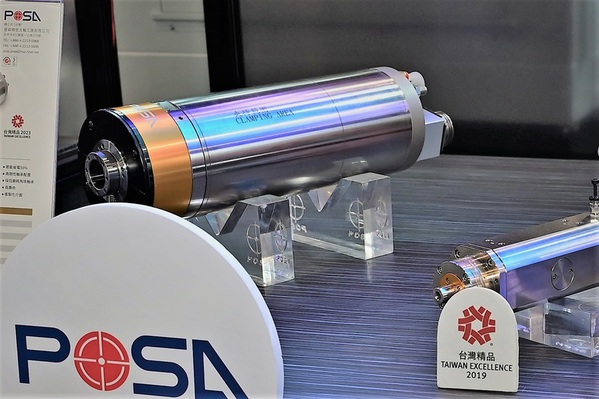
圖三 : :普森也已推出可內建各種感應裝置的智能化高速內藏式主軸,開發「遠距離主軸異常檢測技術」。(攝影:陳念舜) |
|
以及健椿工業(KENTURN)發表搭配CNC綜合加工機的高速/高精智慧化內藏式主軸,透過嵌入式感測器與台製控制器專用軟體支援,提供溫度自動化感測、熱膨脹位移感應及振動感應偵測等智慧化功能。
旋轉台受惠以大帶小 提升五軸加工機減碳效益
此外,面臨當前淨零減碳壓力下,因為五軸加工中心機的A/C兩軸旋轉工作台既屬於高單價產品,加上作動頻繁,更需要持續進給驅動,也是排碳占比最高動件。所以於零組件供應鏈率先由德川切入,也可減少零組件碳足跡,預估將能為工具機、終端市場用戶最快帶來顯著的環境效益。
德川機械公司(detron),則是台製旋轉工作台市占率首位的製造廠商,其智能五軸旋轉工作台可透過i4.0-RT智慧盒訊號傳輸,可以實現即時狀態監控、異常紀錄追蹤、保養履歷跟蹤及自動背隙補償(發明專利);並可透過MQTT通訊協定上傳感測器資訊,若再結合客戶自行開發的智慧化軟體,更進一步協助大型設備廠實現智慧製造。
德川不僅於2023年便透過PMC輔導,成為台灣首家通過ISO14064-1溫室氣體盤查的旋轉台;如今ISO 14955-1也成為內部設計高效元件的重要參照規範,能在實現同等加工性能的情況下,減少能耗。且將在今年TIMTOS展出其選擇搭載DD直驅馬達、雙導程滾子凸輪等全系列節能旋轉台,可用於承載大盤面加工航太、車輛零組件。
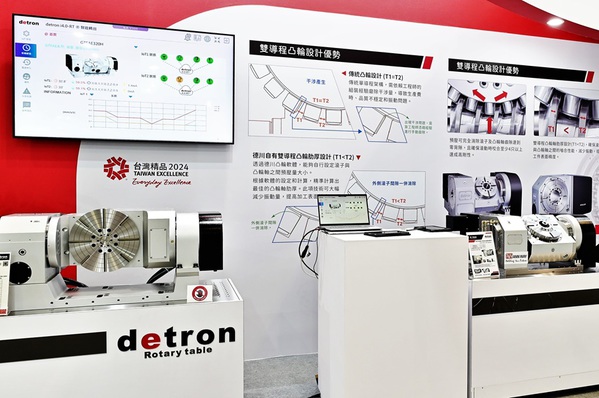
圖四 : :德川因為自主掌握雙導程滾子凸輪結構的加工原理與設計knowhow,減少過去因干涉造成震動、異音、溫升的狀況。(攝影:陳念舜) |
|
透過加工應用軟體,增加該公司滾子凸輪轉動時的貼合率,減少傳統滾子凸輪常因干涉造成震動、異音、溫升的狀況,大幅增加50%切削剛性的競爭優勢。現也提供韓國半導體產業客戶輔助晶圓加工石英、碳化矽材料,已累積上百台應用實例,並在今年台北國際工具機展(TIMTOS)也預計會與3~5家台灣廠商合作。
且有別於過去,零組件廠僅以馬達等驅動元件的出廠參數來計算旋轉軸特徵,當高階轉台通過品管出廠時,不易取得精度、摩擦力、黏滯係數等特徵參數來實現精確評估。倘若整機廠的轉台因為工件重量改變,導致負載與慣量增加,而擴大追隨誤差,將影響工件精度品質。
到了2024年開始導入PMC協助開發的「旋轉工作台即時異常自適應調控模組」後,即可供零組件廠實測五軸工具機擺動軸動態負載狀態,快速鑑別轉台慣量、摩擦力、黏滯係數等關鍵係數,將有效減少80%鑑別量測作業時間(20分鐘→3分鐘),獲得真實的轉台特徵。
既可做為提升組裝品質確認工具,以提升產品良率、降低成本,方便整機廠自動針對負載,快速調整參數提升品質;並維持智慧轉台在不同負載狀態下自適應,減少追隨誤差32.4角秒→5.76角秒,以確保產品品質加值,提升五軸工具機運動精度,驅動產業實現高效加工。
預估年產量約100台的直驅式旋轉工作台,在導入該模組後,每年可望提高10%銷售數量,增加約1,000萬元/年產值收益。終端金屬加工業也能有效提升加工尺寸精度,避免因為誤差過大而降低良率。