汽車產品開發的效率要讓製造模擬產生最大的效用,必須使用關鍵參數進行快速測試,以找出更佳、更可靠的設計解決方案。自動化的CAD關聯模擬模型建構方法可提供數位連續性,快速解決設計變更和汽車變型問題。
時代變了,汽車被賦予的意義越來越充滿智慧和未來感。如今控制一輛現代客車所需的程式碼行數甚至可能比商用飛機和Facebook還多,而且這還沒有將自動駕駛納入考慮。這其中也許更重要的是設計和製造汽車所需的大量軟體。典型的汽車專案需要數千名工程師使用CAD系統定義幾何結構,使用物理模擬工具驗證效能,然後才能建構任意實體原型,接著使用製造軟體來最佳化工廠營運和供應鏈。
儘管有如此龐大的數位化基礎設施,汽車產品開發的效率與汽車企業的期待仍然相去甚遠。例如在完成設計階段性目標後,汽車製造商平均要用數周的時間來建構精細的汽車模擬模型,接著還要用另外幾周的時間來創建模擬和匯總相關模擬結果。這些延遲不僅影響汽車開發的整體用時,也妨礙設計探索與設計創新。
試想一下,如果在學習鋼琴的時候,按下一個琴鍵,要等一個月才能聽到所產生的音符,會是怎樣的情況?這就相當於在使用模擬時,要看到產品的行為方式需要等待一個月。因此,要讓模擬產生最大效用,必須使用關鍵參數進行快速測試,以找出更佳、更可靠的設計解決方案。
毋庸置疑,汽車OEM廠商非常希望讓設計團隊和模擬團隊更高效地展開協作。實際上,世界各地的電動車新創公司正在證明這種做法。在不使用數十年老舊工具和流程的情況下,借鑒軟體工程的做法,組織更加敏捷的開發團隊。乎普遍採用3DEXPERIENCE平台實現傳統開發環境下無法提供的協作模式和工作效率。
透過將3DEXPERIENCE平台與其設計模擬關聯性和自動化網格、扣件和配置管理進行完美結合,能夠將模擬模型的建構時間明顯縮短多達五倍(圖1),並且還將繼續進行相關改善。
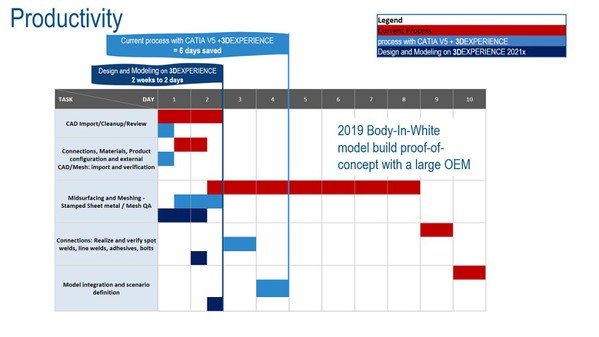
圖1 : 白車身(Body-In-White)模擬建模時間加快 |
|
跨越隔閡,推動數位連續性與協作
以車身工程為重點,我們在圖2中可以看到目前面臨的一些挑戰。首先,互不相連的工具鏈造成設計、工程與製造之間隔閡重重。以下是大多數OEM廠商的車身工程環境現狀的典型示意圖。
無法在設計與模擬間有效地維持模型可追溯性和連續性仍然是生產的一大障礙。3DEXPERIENCE平台可為所有結構屬性都提供統一的主模型(圖3),方便用戶自動為碰撞、NVH和耐久性模擬衍生合適的模型,進而解決這個難題。
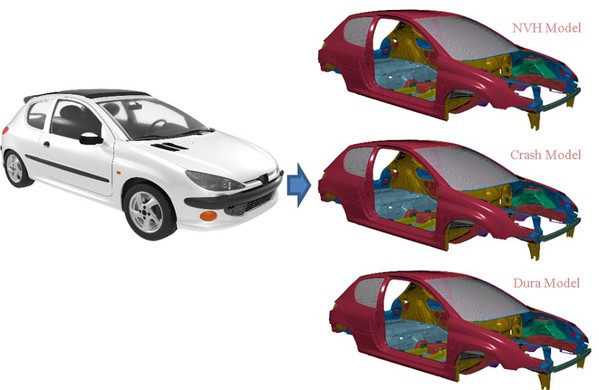
圖3 : 從主設計模型我們能自動為不同效能屬性產生模擬模型 |
|
3DEXPERIENCE平台能用CAD資料自動創建有限元網格。從同一個設計出發,您能夠為各種類型的模擬管理不同網格密度和不同幾何結構簡化(刪除倒圓角、忽略小孔等)的多種網格表現。這些網格與設計幾何結構相互關聯,所以可以在修改幾何結構後更新模型,不必重新創建分析屬性。還可以使用奠基於規則的批量網格劃分技術,自動網格化由數百個殼體部件構成的大型裝配。
典型的現代車身可能使用多達500個部件和5,000個扣件。後者的組成包括點焊、縫焊、鉚釘、螺栓和黏合劑,如圖5所示。
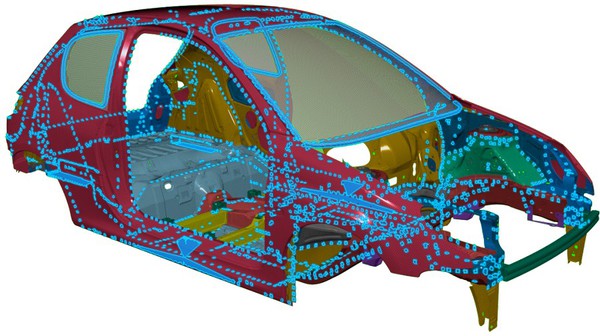
圖5 : 圖為典型汽車的扣件,例如點焊、縫焊、黏合劑、螺栓 |
|
為了以最低成本實現效能,OEM廠商極為關注對扣件的佈局進行最佳化。但是由於設計、模擬和製造團隊分別維持獨立的扣件資訊庫,團隊間資料經常不同步或發生遺失。
此外,即便是在模擬部門內部,仍然需要為不同的效能屬性管理多種扣件的表現。例如,NVH模擬中不需要針對點焊預測失效,但在碰撞模擬中就需要針對點焊預測失效。透過3DEXPERIENCE平台,也可以為不同屬性管理多種扣件表現。
最後,同一車輛的多種配置可能需要針對同一需求展開多次模擬。3DEXPERIENCE平台能讓使用者根據汽車配置輕鬆地篩選設計,然後自動產生合適的模擬模型。
需求驅動模擬
從根本上說,企業使用模擬的主因之一是預測產品效能對需求的符合度。物理測試的缺點不是成本過高,就是過於費時,或者兩者兼具。隨著汽車的複雜性不斷增加,內部要求、消費者要求以及合規要求也隨之增加。例如,以下的示意圖展現過去50年中對碰撞安全需求的大幅增加。
3DEXPERIENCE平台能管理需求與模擬驗證或物理測試驗證間的反饋環路。在整個開發過程中持續地將所有這些資訊都整合到統一平台上,提升以更快速度制定更優秀決策的可能性。
展開模擬的另一個主因是在開發中儘早地深入瞭解產品的行為和效能。透過使用模擬探索設計方案,能夠快速剔除低劣設計,聚焦於最有發展性的方案,這就是為什麼要將快速設計探索的工具整合至3DEXPERIENCE平台的原因。
如今,在進行正式設計審核前,NVH、耐久性和碰撞團隊不會展開協作。將資料統一在3DEXPEREINCE平台上,就能夠持續不斷地分享不同的設計方案和對策。透過這種方法,每個團隊都能始終使用相同的資料,CAE團隊也不必在上一個設計階段通過後,需要等到下一個階段才能驗證彼此的方案。
這種跨職務協作自然地促進多學科最佳化。在當今的大多數OEM廠商中,資料與組織方面的重重隔閡,真正的多學科最佳化依然少見。3DEXPERIENCE平台不僅能促進前所未有的協作,也能為設計探索與最佳化提供緊密整合的用戶體驗。可以在定義模擬模型的時候,直接最佳化形狀和大小參數,如材料屬性和測量厚度等。
總之,多個團隊用多種互不相連的工具展開工作的傳統方式,將難以在下一輪創新浪潮和競爭壓力下生存。3DEXPERIENCE平台可為解決這些挑戰提供下列主要價值:
* 為設計、模擬和製造提供統一的主模型
* 自動化的CAD關聯模擬模型建構方法可提供數位連續性,快速解決設計變更和汽車變型問題
* 為不同屬性的模擬提供一體化的扣件管理和網格管理
* 針對設計探索和多學科最佳化的協同工程
* 透過儀表板展開需求驅動的模擬
隨著企業擴大對汽車電氣化和自動駕駛、碰撞、耐久性和NVH的投資,各部門需要在節省資源的同時提高生產力。儘管具備出色的結構效能極為必要,但還不夠。現在面臨的挑戰是在以最低成本滿足所有結構屬性的前提下實現優異的效能。
(本文作者Katie Corey為達梭系統SIMULIA內容創作者;Deepak Goyal為SIMULIA航空航太與國防工業成長團隊模擬顧問)