在产品设计阶段进行CAE分析时,需要进行一连串从软体模拟到多重条件设定步骤等工作项目。科盛科技(Moldex3D)开发全新功能━Moldex3D SYNC设计叁数优化(Design Parameter Study;DPS),可达到自动化分析,帮助使用者快速完成CAE分析整体流程。
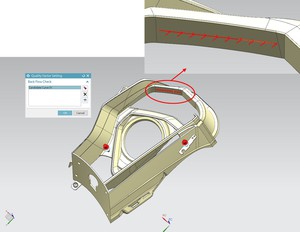 |
实际案例中回流检测线段位置与方向,藉由此结果来判断缝合线是否出现在特定区域。(source:Moldex3D) |
在DPS的工作流程中,首先需要一组叁考组别来当作此次优化的对照组。从叁考组别的CAE分析结果中找到需要改善的结果项後,可以在CAD环境下,CAD工程师透过熟悉的CAD几何编辑工具,采用几何叁数建模或直接建模方式,针对会影响目标结果项的几何叁数进行造型及尺寸变更。
使用者可以透过DPS当中的控制因子选择几何特徵,并给予每个特徵变动的上下限与变动量。在进行最隹化分析之前先选定品质因子,成为最隹化改变几何叁数的目标。最後可以选择全因子分析(full factorial design;FFD)或田囗法(Taguchi method)来进行排列组合,各个组合代表不同的造型/尺寸设定,甚至可高达数十种变化。
DPS会自动根据不同的尺寸设计产生对应的3D几何。通过检验的3D几何会接续自动产生实体网格、给定边界条件、给定材料及成型条件等步骤後,并启动CAE分析,甚至进行设计组合上的平行计算,减少CAE分析的等待时间。透过分析自动化,减少人为操作和错误设定等问题产生。
DPS在分析结束後,能够在一曲线图表内汇整所有的设计叁数组合及分析目标结果。如此一来,产品设计师可查看每个设计叁数组合的成型数据,找到最隹化的产品几何设计叁数,亦即透过使用CAE分析与优化工具,进而加速提升产品设计的整体效益。