積層製造 (AM,也就是「3D 列印」技術) 為產品設計所帶來的突破,可說是推動頂尖產品創新的重要推手。作為數位製造革新的重要一環,積層製造不僅大幅簡化了複雜零件的生產過程,同時還提升了性能、減輕零件重量,也減少組件數量。金屬3D 列印正好能應用在不斷追求創新且堅持超高質量的行業應用,如汽車業。
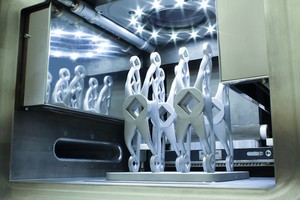 |
AM 400 製程室中的 Bleu 汽車鉸鏈組件 |
「台灣國際3D列印展」於8月29日至9月1日在南港展覽館開展,Renishaw 於 I410 攤位展出AM 400 金屬積層製造系統及QuantAM、InfiniAM軟體,搭配Equator? 檢具系統示範即時工件量測,並展出包含Bleu汽車鉸鏈在內的多樣3D列印應用產品。
在 3D 零件的製作過程中,拓撲最佳化是很關鍵的一個步驟,這可確保物料在定義的有限空間內可獲得最有效的運用。Renishaw 與世界首屈一指的 3D 設計軟體供應商Dassault Systemes攜手合作, 成功設計並製造出概念車款 Bleu 的車門鉸鏈,實現金屬3D列印零件在前衛的概念車零件上的應用實例。
Renishaw 與Dassault Systemes合作的目標,是要打造合理的 AM 設計和製造流程,讓製造商不用再花大筆資金投入「設計 – 建造 – 測試」的流程,而是享受「一次搞定」的快速效率。
由於這款鉸鏈是既複雜又輕盈的雙 A 臂組件,Renishaw和Dassault Systemes的工程師在面對這樣一個真正的生產案例時,必須使其同時符合拓樸最佳化設計結果以及積層製造設計準則。在這樣嚴酷的條件下,工程師需要修正車門鉸鏈設計後進行力學模擬,再藉由金屬積層製造技術製造雛型後進行測試,而上述流程需要經過多次的設計、力學模擬、製造以及測試,才能得到最理想的鉸鏈結構設計。若使用傳統方式製造,這樣的重覆產品開發流程會耗費許多無謂的模具及夾治具時間及製造成本,而採用金屬積層製造技術,零件在一開始便可精確地製造,大幅縮短製程時間,且節省材料成本。而從鉸鏈設計中拿掉所有支撐結構,原始與改良後的外型及零件體積幾乎完全相同,由此可清楚認知金屬積層製造技術的設計可靠性。
在和Dassault Systemes密切合作的過程中,Renishaw 採用一系列最先進的精密加工製造和量測產品,包括使用雷射粉末床熔融技術的旗艦版 RenAM 500M 金屬積層製造系統、QuantAM 建置準備軟體、工具機測頭系統、Equator? 檢具系統,以及搭載 REVO 5 軸量測系統的 CMM。