精密組裝產線追求更穩、更小、更快、更準的組裝設備,微型線性運動模組搭配低壓伺服驅動的高精高速運動控制,是產品質量提升的關鍵。
資訊科技日新月異,工業級及消費性電子產品不僅性能快速提升,體積也越趨精巧輕薄。在產線上,組裝設備要在有限空間內取放、安裝既細小又脆弱的元組件,還要顧及產品良率與產線稼動率,對於精密電子組裝業者來說,是一大考驗。
在自動化精密組裝製程中,高速、高精確度的運動控制不可或缺,電子組裝業、半導體業和設備製造商等,無不積極追求更穩、更小、更快及更準的組裝設備。本文敘述精密電子行業中,如何藉由優化組裝設備中的Z軸高速運動來提升產品良率,並且聚焦解說與微型線性運動產品,如何突破產業痛點。
Z軸運動是電子產品組裝良率關鍵
Z軸運動指垂直產品上下方向的運動,在精密組裝產線製程中,細小元件與晶片的取放、移載、壓合、貼裝、固晶、插件及檢測等,皆是Z軸運動的例子,在電子組裝產線與半導體封裝製程中,扮演著核心環節。
在精密製程中,元件的材質與體積大多輕薄、小巧且脆弱,Z軸運動過程中的力量控制若稍有閃失,皆有可能導致元件受損,進而影響成品的良率與產量。以常見的手機與車用鏡頭模組為例,在製造時需要取放、堆疊及安裝多片玻璃或塑膠材質的鏡片,壓力容許誤差在20g以內,運動控制要求極高。在半導體產業中,裸晶的移載與固定的工藝中,壓力容許誤差只有±2g,製造技術條件更嚴苛。
Z軸運動在傳統機台上,常用氣壓缸或是使用旋轉馬達搭配螺桿的方式進行驅動。氣壓缸驅動無法有效掌握力量控制的精度,也無法蒐集與監控數據。旋轉馬達搭配螺桿,雖然具有出力較大、成本較低的優勢,但也有機構複雜、易因摩擦產生零件與能量耗損、且體積較大的特性,且因屬間接驅動,控制響應速度較慢。兩者在追求高精度、高速運動控制的精密製程場景中,應用上皆有不低的技術門檻。
除了準確的力量控制,在電子產品越來越小巧的製造趨勢下,驅動Z軸運動的機構設計與製造,必須往輕薄、緊湊的方向進行。除此之外,為追求產線的稼動率最佳化,多軸同動的驅動與控制也不可或缺,才能有效提升產量。
總而言之,為了提升Z軸運動的精密製程效率,組裝設備必須解決力量控制、力量感測、位置回授、機構直驅及尺寸輕薄等多重難題,並盡可能縮短生產週期時間,才能突破製程良率的痛點。
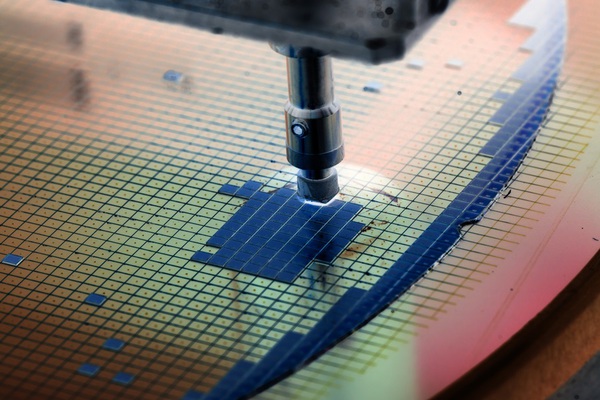
圖一 : 在精密組裝產線製程中,元件的材質與體積大多小巧脆弱,Z軸運動過程中的力量控制是影響成品良率與產量的重要因素。 |
|
線性運動模組如何一舉突破良率與稼動率難題
台達關注電子組裝與半導體產業精密製程,因應高精高速運動控制的需求,推出多種線性運動產品。其中,微型線馬致動器LPL是一款一機整合線性馬達、光學尺、力量感測器、小旋轉伺服馬達、編碼器、滑軌和框架於一體的模組型產品,可同時用於線性與旋轉運動,適用於組裝設備的Z軸或含旋轉的ZR軸運動。
LPL的連續推力為5至37N,特點是響應快、力量控制可達0.1N,細微且穩定。結合使用自製的光學尺與讀頭,位置回授解析度高達0.5 μm,符合高精度需求。零背隙的直驅設計降低摩擦耗損,有效提升設備壽命,並降低維護成本。再結合伺服驅動器,可有效滿足多數電子精密組裝、半導體封裝等應用場景中的推力、行程需求。
除了線性運動外,LPL內部也搭載厚度僅有13mm的旋轉伺服馬達,並搭配20bit 編碼器回授,在旋轉解析度可達到0.01度,可滿足高精密組裝時,最細微的微動量。
精密組裝業者最常見的製程痛點之一,是如何在最小空間體積內確保最多自由度軸數,也因此在許多應用中,機構輕薄是提升稼動率的關鍵因素。LPL在精密製程上的優勢,在於體積非常輕薄,在有限空間中只要能多裝一組馬達模組,就可有效縮短製程時間,並提升稼動率。
以tray盤上的工件移載為例,假設tray盤格子間距為10mm,若使用厚度20mm的ZR軸產品,就必須要移載兩次才能填完兩排。若使用台達最薄的9mm LPL,20mm的空間內可多裝一組,操作上一次就可以完成兩排的工件移載,稼動率即可提升一倍。
為了完全發揮LPL的體積優勢,應用上皆採多軸設計,因此縮小伺服驅動器的體積也格外重要。台達的伺服驅動器ASDA-D3,採用雙驅動系統,兩個獨立的驅動單元實現雙軸同動,確保高速度、高加速度的同時,可保持系統的運動平滑性,對於需要在極短時間內實現快速運動的Z軸高速取放至關重要。
ASDA-D3使用二軸合一的設計,一台即可控制兩個軸向,整體體積相較於台達同級100w單軸伺服驅動器,可節省配置空間高達70%,在同步使用多台LPL時,可大幅提高機台空間利用率。
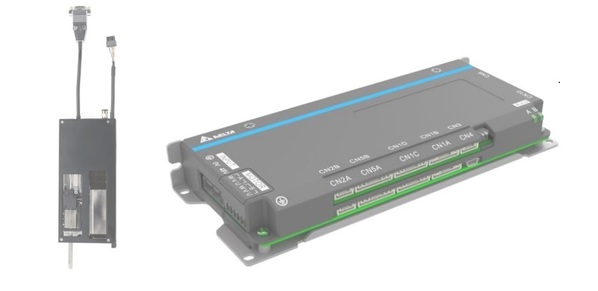
圖二 : 透過整合配置微型線馬致動器與二軸合一的伺服驅動器,可實現多軸同動並有效提升產線稼動率。 |
|
如前文所述,Z軸運動精準細微的力量控制,是提升精密製程產品良率的關鍵所在。LPL可透過伺服驅動器內建之二次平台功能,實現軟著陸(soft landing)功能。在ASDA-D3內建整合控制器功能,則能夠大幅縮短響應時間,同時節省配置空間。
透過LPL的光學尺和力量感測回授,ASDA-D3可進行細微力量控制,增加元件與晶片取放應用的效率與良率,也能幫助客戶應付不同應用的控制模式切換,減少對第三方感測器的整合與調適。
進一步說明軟著陸,在行程上可拆解為4個階段動作。如圖三所示,設想位在A點的吸嘴,要取位在C點的元件時,首先會採「位置模式」,高速下降到預設位置B。抵達B點後,採「速度模式」低速下降,緩速接觸位於C點的元件,此階段即所謂「軟著陸」。於C點接觸元件後,採「扭力模式」進行力量控制,加壓、保壓做定扭力輸出,透過力量感測回授確認取物,最後回到「位置模式」,完成取物。藉由速度與施力的細微調控,LPL可以在不傷及脆弱元件的條件下,順利進行取放與安裝。
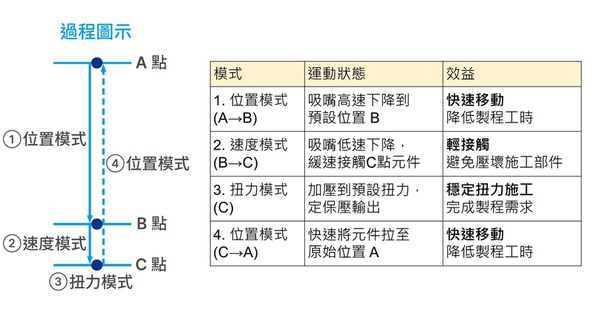
圖三 : 軟著陸原理說明,透過實現細微的力量控制,強化產品良率。 |
|
微型線馬致動器LPL結合伺服驅動器ASDA-D3的Z軸運動控制解決方案,已成功驗證並放量導入於取放貼標、3C組裝、高密度貼片、AOI檢測及轉塔分選等需要進行大量Z軸高速取放應用場景。
LPL的併排安裝搭配ASDA-D3的雙軸驅動,多軸同動配置有效提升生產線稼動率,並以高精高速運動控制與軟著陸功能,顯著改善了產品的裝配精度與良率,得以滿足客戶在精密電子組裝與半導體產線上的產能需求。