基於工業4.0理念近年來已逐步落實於產業鏈,對於影響切削加工品質和生產力最前端的刀具監測者,除了End user之外,也陸續向上延伸到系統整合(SI)、工具機製造(Maker)廠商。尤其是未來新興產品朝向個性化、客製化訂製方向發展,相關製程也須不斷進行工序整合、高度自動化,帶動車銑複合加工機和零組件、周邊自動化設備需求水漲船高。
根據國際工具機大廠DMG MORI曾分析現今製造業市場趨勢,認為除了受到少子高齡化社會影響,將導致勞動人力短缺,加速機械人工智慧化(AI)之外,此也有助於解決過去因為量產汽車、馬達轉軸等零組件生產型態多元,必須結合車、銑與鑽削等多站機台和工序分離(Process Segregation)模式加工,每日產能約達到100~1,000件,卻造成占地空間太大等問題,而開始轉型為高效率智慧製造生產。
改用車銑複合加工機來分別因應未來航太與醫療產業,若採取工序整合(Process Integration)模式來提高生產效率,以每日產能約1~10件生產多樣少量、客製化產品。或是如汽車與3C產業,仰賴高度自動化(Hyper Automation)與智慧管理模組,可在極短交期內,每日批量高效生產5,000件以上產品,從而提升整廠產能的兩極化方向發展。
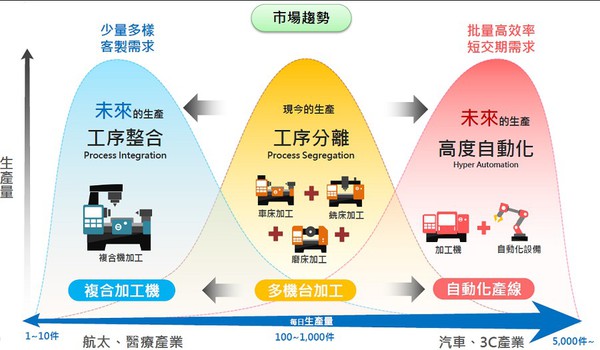
圖1 : 為了轉型高效率智慧製造,近年來業者改用車銑複合加工機,以因應未來航太與醫療產業採取工序整合,或是汽車與3C產業的高度自動化生產,朝向兩極化趨勢。(source:PMC) |
|
精機中心AI刀具智慧管理系統 整合刀倉與刀塔自動換刀
精密機械研究發展中心(PMC)也趁勢協助業界,轉型智慧製造生產,透過科專計畫協助開發能同時完成單機多道工序整合、高度自動化加工的斜背式多刀塔車銑複合加工機,得以減少加工站數量;進而整合自動化與智慧管理模組,執行高效生產解決方案,來實現24/7不間斷自動化加工。
其中,有別於傳統動力刀塔,最多僅能裝配16把刀或4刀塔的64把刀,常導致依序加工使用的刀具常受限於備用品不足,或磨耗過度後須停機換刀。PMC智慧機械設計部經理林成興指出,雖然現今台灣一般市售車銑複合加工機均有搭配伺服動力刀塔,卻不具備自動鬆/拉刀把的功能,導致所有刀具的上下替換皆須仰賴人力,而影響生產效能,有必要開發一套具備鬆/拉刀把機構,可自動換刀的動力刀塔設計模組,讓使用者選擇搭配外部刀倉與自動換刀機構的連結作動,快速替換刀具。
PMC便為此開發AI刀具智慧管理系統,整合刀具資訊並控制機台和刀倉換刀,進行高效率生產刀具管理。可在使用者導入自動刀倉系統後,視需求增加放置20把刀以上加工或備用刀具。並在刀具取放處設計安裝RFID讀取天線,當取放刀把入/出庫時,系統可同步讀取刀把資訊即時管理;採用模組化刀架設計,也可替換單一刀具,能有效降低維護成本。
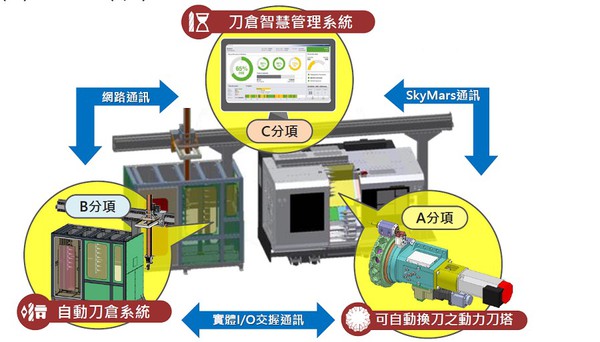
圖2 : PMC為此開發AI刀具智慧管理系統,整合刀具資訊並控制機台和刀倉換刀,進行高效率生產刀具管理。(source:PMC) |
|
經由上位AI刀倉智慧管理系統通過實體I/O交握通訊,整合車銑複合加工機在自動刀倉、動力刀塔的刀具位置等資訊,更有效率應用產線上的所有刀具。進而按照產線排單生產需求,透過不同演算法運算、規劃排程工序,即時反應今日排程、工件是否無誤,並調配刀具使用。
林成興表示,透過線上監控有效管理其刀具履歷、刀具佔用率、空閒率、替換率,記錄刀具磨耗狀態,並利用類神經網路LSTM精確估測智慧刀具壽命可用率等相關資訊,倘若無法用到下一次工序時,須及時替換或遞補更新備用刀。藉此軟硬整合手段,將有效提高刀具使用率、減少停機,讓產線達到24/7不間斷生產,為客戶提升設備整體稼動率OEE等價值。
且為此開發車銑複合機換刀系統,具備自動鬆/拉刀把功能,同時整合BMT介面動力刀塔系統與鬆、拉刀機構設計,與刀塔高度整合,利用切削主軸馬達提供鬆刀動力,以進行刀把自動取放、裝卸的專利動力刀塔系統,避免額外裝置鬆刀用油壓缸,減少空間干涉,且軸承無需承受油壓缸推力;以及HSK介面可換刀動力刀座、拉刀機構設計等,來實現外部刀倉的自動刀把交換功能,將大幅擴充刀具用數量。
透過高效率自動換刀作業,搭配外部刀倉系統的刀具,與自動換刀機構的連結作動,讓加工用的刀具不受限於刀塔端,從而減少人員換刀時間,毋須仰賴人工作業。無論新舊車銑複合加工機都能實現不間斷自動排程換刀生產,執行彈性多樣的工序加工和連續生產目標。
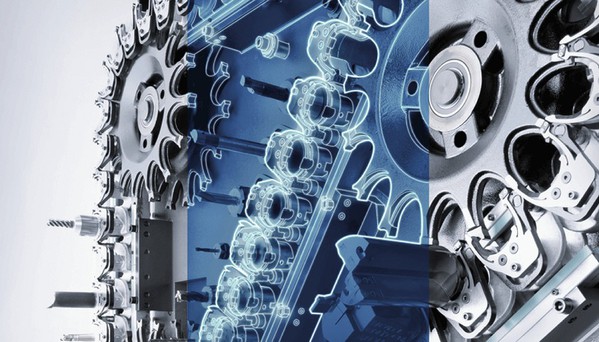
圖3 : 透過高效率自動換刀作業,搭配外部刀倉系統,最多可增加放置20把刀以上加工或備用刀具,與自動換刀機構的連結作動,從而減少人員換刀時間,毋須仰賴人工作業。(source:dmgmori.co.jp) |
|
達詳智能刀具管理系統 實現金屬加工自動化
當傳統金屬加工業面臨疫情衝擊和通膨隱憂,以及航太、電動車等高值新興產業崛起,皆造成全球供應鏈轉型升級與人力不足等多重挑戰,紛紛調整傳統生產模式,積極轉型智慧製造以保有競爭力。
尤其是在加工過程中須要大量使用各種不同刀具,所以產生刀具存放與管理的問題。過去主要透過人工定義刀具壽命,再行抄寫記錄、儲存,用來推演所需刀具數量與種類,無形中會增加人工成本,且無法避免出現拿錯刀、缺刀等失誤,造成浪費和庫存壓力。
即使刀具確實損壞,發生撞刀或斷刀後停機,再重新換刀、補正設定的時間就會延遲,甚至拖累設備稼動率。一般現場操作人員來領刀或換刀的理由,通常也是刀具受損或遺失,但刀具管理人員無法判斷真實性,只能被動補充刀具來避免耽誤工作,皆將導致成本難以控制,為現場操作人員及業主最不樂見。
因此,如何有效管理庫存水位與減少浪費,還能正確選配刀具而避免耗損,對於終端加工生產者會是相當迫切的課題。達詳自動化公司則可扮演系統整合商角色,提供金屬製造業所需智慧製造解決方案,包含精鑄、砂鑄、壓鑄,以及工業機器人、拋光研磨後處理製程,與智能刀具管理、AI智慧製造系統、AS/RS自動倉儲系統等自動化整合服務。
現也透過達詳自主開發的DSA專利智能刀具管理系統,有別於現今市面上既有刀具管理系統和存放設備,共由「DS智慧刀具庫」+「DS智慧刀具車」+「DS刀具管理系統」3個面向全方位智慧整合軟硬體設計而成,以協助使用者正確選用刀具、紀錄刀具使用歷程,並藉此自動判斷刀具狀態而提高生產效率,不僅有效控管刀具庫存及成本,也減少加工失誤的風險。
藉此讓業主除了可透過系統在現場換刀時,自動輸入補正值到加工設備,而避免人為輸入錯誤,導致撞刀;具備自動配置所需刀具到刀具車內功能,可搭載達詳獨家設計DS智能刀具車為主的AGV自動搬運系統,將所需刀具自動運送配置到機台邊,再利用Wi-Fi與工具機交換資料。
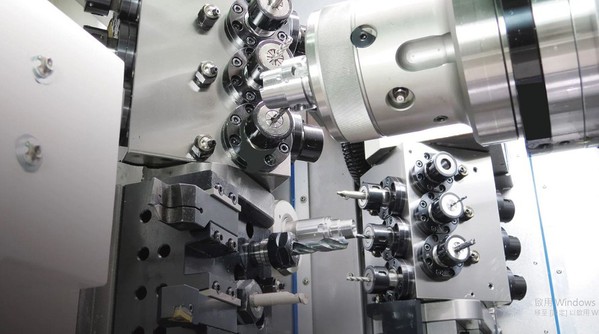
圖4 : 由於車銑複合加工機在加工過程中須要大量使用各種不同刀具,該如何有效管理庫存水位與減少浪費,還能正確選配刀具而避免耗損,對於終端加工生產者會是相當迫切的課題。(source:sme.org) |
|
透過RFID辨識技術同時整合刀具庫和刀具管理系統,搭配磁鎖式刀具的互鎖換刀機制、雲端化智能系統管理的換刀流程,整合資料庫的刀具履歷和庫存狀況等資訊,使得系統能比對RFID,限制人員領或換刀行為,避免刀具遺失或者上錯刀的情形發生;進而管控刀具庫存、節省尋刀時間,得以有效協助客戶解決庫存及成本管控的問題。
該刀具管理系統利用資料庫管理技術,同時監控刀庫、刀具車及工具機內所有刀具的資訊和狀態,透過分析管理各項數據而有系統化管理刀具庫存水位,並建立刀具履歷,進一步與AI技術整合,計算出最佳建議刀具,控管採購需求數量和整體加工成本。
讓業主既可結合現有訂單,經由達詳自行設計的SMB系統,蒐集各項設備資訊和APP/WEB友善的使用者介面呈現,來瞭解未來1~2個月內生產所需刀具;並搭配DSA雲端智能刀具管理系統配送,可從遠端即時監看而掌握現場機台狀況,結合量刀系統預先紀錄補正值。
此從SMB導入到刀具管理系統的運用,都在體現智慧工廠可真正幫助客戶落實高效管理與生產,還能搭配DS智慧刀具管理、SCADA、MES或是自動化系統等軟硬體完善整合,更能按照客戶需求和預算去協助評估與規劃,實現當下智慧製造帶來的產能與效益目標,解決多數傳統產業轉型的困境,緩解工具機產業長期缺工問題。
結語
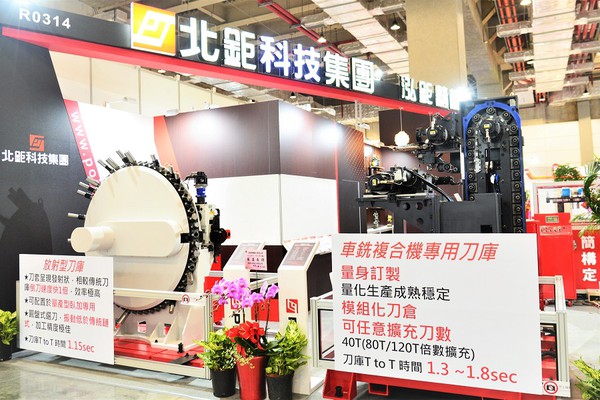
圖5 : 產學研各界應積極改善產業體質,包括上中游工具機及自動化設備、系統整合等廠商,藉以提升設備稼動率、確保穩定品質與訂單交期。(攝影:陳念舜) |
|
自從2018年以來,台灣機械業雖然受惠於地緣政治導致供應鏈衝突,導致供應鏈重組;以及因疫情促成遠距作業、企業數位轉型等需求,與電動車等新興科技持續擴張,伴隨半導體、電子設備出口商機。
但下半年則面臨俄烏戰火波及,造成能源、原物料通膨危機和供應鏈瓶頸,產學研各界仍應積極改善產業體質,包括上中游工具機及自動化設備、系統整合等廠商,須積極投入開發車銑複合加工機等機種,同時導入周邊刀具智慧管理系統,藉以提升設備稼動率、確保穩定品質與訂單交期,將是轉型成敗與否的一大關鍵!
*刊頭圖(source:wintool.com)