看好現今積層製造逐步深入製造業應用,尤其是在航太、汽車等先進製造領域不斷推陳出新,所需關鍵零組件、模具既能整合積層製造(加法)及傳統切削/成型(減法)工法,加快客製化開發生產速度;位居供應鏈上中游的工具機製造廠商也開始引進相關硬軟體升級轉型,以提升國際競爭力。
回顧在2000年之前製造飛機結構件與蒙皮等使用的主要材料,仍採取以鋁合金(Aluminum)、鈦合金(Titanium Alloy)和其他輕質(非鐵)金屬材料為主。直到近20年來,始因為碳纖維(CFRP)等複合材料(Composites)具有輕量、高強度特性,可適應惡劣環境;加上製造技術進展與生產成本下降,陸續於航太、電動車用零件加工領域應用比例大幅增加。
且隨著新品設計愈來愈複雜,零件曲面和複雜度不斷提升,也為廠內加工設備帶來改變,需要經過重複多次轉向夾持進行加工,而容易因為人為架設失誤而報廢;複雜曲面也容易產生加工刀痕交錯的表面,不僅影響品質,可能還須反覆修整,導致交貨時間延長。
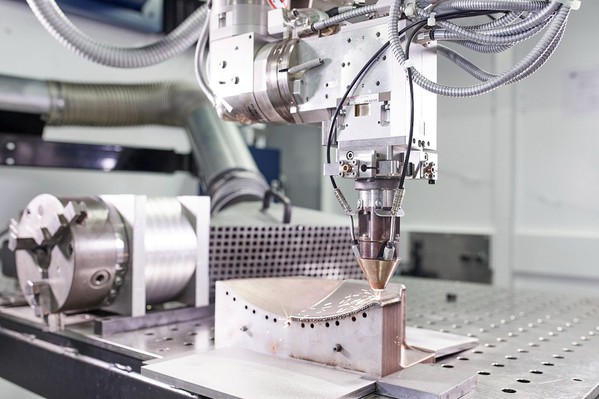
圖1 : 業者在導入積層製造之後,不僅能利用其潔淨度高、機械性質穩定等優勢;且因為採取層層堆疊工法,不受限傳統CNC切削加工的特性,已被航太、汽車製造業廣為應用(source:x-plomachinery-x-cn.img.abc188.com) |
|
反觀業者在導入積層製造之後,不僅能利用其潔淨度高、機械性質穩定等優勢;且因為採取層層堆疊工法,不受傳統CNC加工拔模角或倒勾幾何無法成型等束縛的特性,得以用來成型加工極度複雜曲面和負成型角,解決傳統模具不易處理的流道/冒口等問題。適用於快速開發模具,生產高單價、少量多樣,甚至大批量客製化產品,已被航太、汽車製造業廣為應用,將可大幅縮減產品研發時間和開發成本,提高量產良率。
即使近年來受到疫情影響民航機市場成長幅度,但包含貨機改裝、低軌衛星供應鏈等航太製造業需求仍方興未艾;加上汽車電動化趨勢,都促使機(車)身外殼及機構件、引擎等關鍵零組件及模具等加工生產領域發展創新,並紛紛投入研發輕量化、拓樸最佳化結構設計。
積+減法混合製造 歐日系大廠全都要
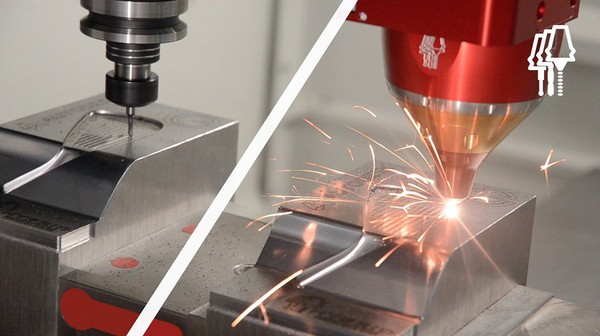
圖2 : 現今還有能整合金屬積層製造(加法)+切削(減法),形成新型混合加工設備,以針對製造或修補大型複雜外型的工件加工。(source:3dadept.com) |
|
然而,目前業界將積層製造導入快速開發生產過程中的最大困難,即是傳統機台上可成型的尺寸受限,倘若用於製造及修補如鑄造陶心或模具、葉片等較大型工件時,仍須採取分割設計再組合的方式製作。
除了已有採取傳統刀具切削(減法)的工具機,因此發展出單機多軸化(三軸以上)與車銑複合加工機種,或搭配放電/線切割、雷射、超音波等輔助成型加工技術,已成為當前工具機產業重要發展趨勢;甚至還能整合積層製造(加法)等工法,形成新型複合加工設備,以針對製造或修補飛機機體結構件、引擎葉片、船用螺旋槳等複雜外型工件進行精密加工。
包括日本MAZAK公司推出的INTEGREX e-1250V/8 AG多工複合加工機,便具有齒輪刮削、滾齒、齒輪銑削與Gear Check Plus量測功能,可應用於生產內/外正齒輪、斜齒輪和花鍵式齒輪,該機種也具備積層製造與摩擦攪拌焊接的功能。DMG MORI已推出多款結合積層製造,與一般多軸銑削功能的複合式加工機,也可應用於複雜結構、高價值工件加工。
德國HAMUEL公司研發HSTM複合加工機,還利用不同加工刀具、測頭與雷測模組,可提供專門用於修補、再製渦輪葉片與風扇的高速銑削、雷射熔覆、去毛邊/拋光,以及3D掃描/檢測、雷射打標等不同製程功能的專用機種。
涵括供應鏈硬軟體 +GF+串連積層製造解決方案
瑞士商喬治費歇爾公司(+GF+)多年來也為此,提供客戶所需積層製造材料、機台硬/軟體、夾治具等完整解決方案。即使近年來陸續遭受國內外疫情復發、俄烏戰火等變數不止,導致原物料、運費價格飆漲和交期遭遇瓶頸,+GF+在台灣除了會對於物料儲備上調整;在銷售機台方面服務,也已透過眾多應用中心,可分別針對需求孔急的客戶配合加工應用測試,或是提供展示現機銷售,以縮短客戶等待時間。
由於+GF+積層製造應用領域廣泛,目前除了可在模具業導入異型水路應用外,零件加工部份則是涵蓋了航太、醫療、半導體、汽車等產業。例如在航太產業方面,過去有許多機身結構支架係採用傳統CNC銑削加工,所使用的鈦合金材料、刀具成本價格不斐,移除的材料卻比留下的材料多;還須配合曲面設計,在加工中不斷翻轉夾持,對於產能和成本都是一大考驗。
+GF+現已發展出串聯積層製造與銑削加工設備的解決方案,便分別針對五軸銑削和車銑(Mill +Turn)加工應用發表新品,今年高階Mill X更導入Grinding高精度研磨功能。同時配合航太大廠利用+GF+積層加工解決方案進行研發,從設計端提供3D Xpert軟體開始優化產品,再進入金屬積層製造積層製造全製程整合。
+GF+進一步表示,目前該公司的金屬積層製造設備配合工業製造所需,共分為275x275x420mm、500x500x500mm兩種行程規格,可讓客戶有足夠空間同時堆疊多種設計;再經由3D Xpert軟體匯出積層製造完成的銑削程式,搭配+GF+自有3R夾治具系統,確保在製程轉換過程中,毋須重新夾持校正。
最後,針對於工件移除積層製造平板後的線切割加工,+GF+也可提供獨家CUT AM線切割加工機,得以改善傳統線切割加工在金屬積層製造時的不穩定性和零件掉落的風險,保持優良品質和完整性。透過+GF+獨特全流程金屬積層列印製程,將能讓終端加工業客戶的產品提高近20%產能,且有效節省銑削刀具和材料成本,順利達到產能最佳化狀態。
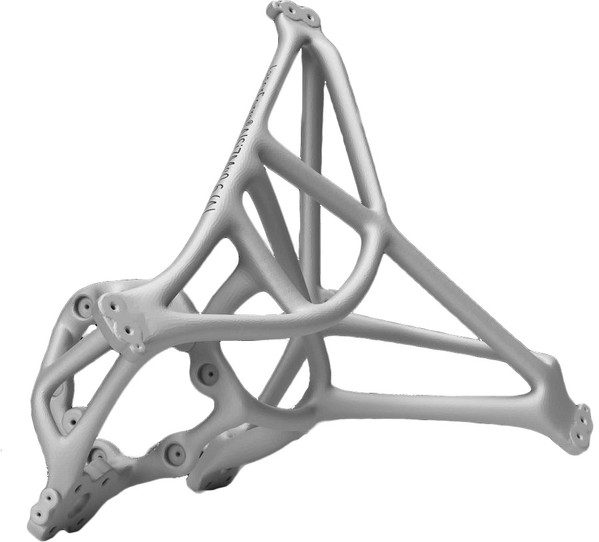
圖3 : +GF+現已發展出串聯積層製造與銑削加工設備的解決方案,克服過去有許多機身結構支架因採用傳統CNC銑削加工,對於產能和成本造成考驗(source:+GF+) |
|
跟進混合加工應用 台廠開發高階五軸機種
同樣在全球工具機消費市場占有重要地位的台灣工具機產業,則有從產銷五軸加工中心機起家的嵩富機械(Pinnacle),在2019~2020年間與成功大學、金屬工業研究發展中心合作,於現有五軸銑削加工中心機上整合金屬積層製造,可用於減縮製程、以航太引擎、燃氣渦輪機葉片等大型工件的時間及成本,並在供粉過程中逐漸改變材料特性。
嵩富機械專案經理陳錫卿坦言:「由於目前台灣工具機產業仍以銷售標準機為主,常面臨競爭對手低價搶市,導致業者經營不易;以及終端加工業者針對航太、電動車等新興應用領域所需高溫合金零組件材料,皆屬於難切削材居多,造成刀具急遽磨耗、加工效率低,製程成本居高不下等難題。」因此,業者未來勢必應轉型朝向開發高階專用機種,進而改善高溫合金加工效率及成本問題,已成為工具機產業開創新局的契機之一。
「隨著雷射加工設備逐年穩定成長,與積層製造相關市場趨近明朗,勢必帶動混合加工設備需求。」嵩富認為,其除了可應用於加工航太、船舶、汽車、模具等多項重要產業的精密組件,相較過去僅能採取各種切削工法,更提供了金屬積層製造能力;而模組化的主軸設計,更讓嵩富銷售機台在客戶選配時,可有更高階零組件選擇,並創造高價值的技術性產品。
目前嵩富與成大機械系也趁勢整合相關五軸工具機、雷射披覆DED積層製造、4/6系列不銹鋼搭配鎳基合金(Inconel 718)粉末、加減法虛擬加工系統、雷射熔覆送粉模組與熔覆品質監診等技術,形成產學研互利的協同合作模式,克服鎳基合金經過積層製造後將更難銑削,進給耗時又磨損刀具等問題。
嵩富藉此在結構設計方面,由成大協助開發以中低功率1000W雷射為熱源的自製雷射頭及雷射熔覆送粉模組,將產學研發應用成果導入產業。於同軸送粉的連續雷射披覆機台上,完成對於雷射披覆DED金屬積層製造技術的開發與分析,通過金屬工業研究發展中心進行材料分析、產品拉伸試驗;同時搭配複合五軸銑削加工系統的CNC編程,利用達康科技支援的PowerMILL軟體,執行五軸加工機加減法的工序,得以涵蓋從車用、航太及燃氣渦輪增壓器排氣葉片加工生產、局部強化,直到產品品質檢測驗證的完整流程,提供能滿足工業4.0、淨零碳排產業趨勢所需先期儲備技術。
現已陸續完成驗證葉輪載具製作驗收規格,包括:葉片尺寸精度≦±0.01mm、表面粗糙度0.316μm;融覆高度>3mm、融覆寬度1.5mm;5片硬度HV222,達Inconel718素材硬度/抗拉強度/降伏強度數據80%以上。
針對單機加減法複合製程開發工件熔覆品質金相組織檢測,該密度分析達8.18g/cm3,與原材密度8.19 g/cm3比較,緻密度達99.8%。至於熔覆材厚度標準差為5.9μm,該平均值為452.3 μm;而材料利用率則在單光束可提升40.4%,在多光束雷射下,材料利用率可提升達53.4%。
完成加減法五軸加工設備之雷射熔覆製程模組整合,技術規格包含:熔覆加工速度400mm/min、積層厚度每層160μm、積層寬度 0.71~2.3mm、尺寸精度<±8%,單光束粉體利用率提升為40.4%。
嵩富進一步表示,經過此產學合作專案後發現,旗下團隊因此對於工業級雷射源的品質差異了解甚高,得以藉雷射系統整合使用者、與了解國外雷射源技術角度後,協助建議雷射源設計及測試自主開發雷射熔覆模組性能,進行優劣比較並回饋資訊修正。團隊也經過接觸多元雷射應用產業,可由終端用戶的角度提供模組化光路的設計想法,更為符合產業需求;藉此縮短開發時程,並可搭配五軸加工設備實際應用驗證,以利達到商品化目的。
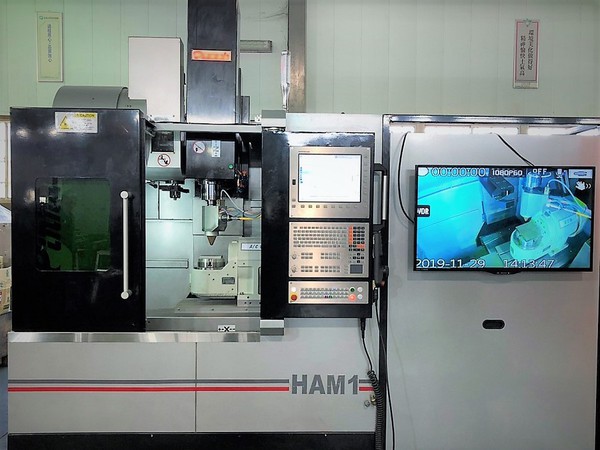
圖4 : 嵩富機械與成功大學、金屬工業研究發展中心合作,於現有五軸銑削加工中心機上整合金屬積層製造,可用於減縮製程、修補航太、燃氣渦輪機葉片等大型工件的時間及成本(source:嵩富) |
|
結語
值得一提的是,由於積減法混合加工對於工件品質要求更為嚴苛,過程中須對於工件持續加工時進行線上量檢測,既可減少多餘的上下料時間,加快生產效率;也避免了工件在不同機台間裝卸,容易影響加工精度。
不僅在瑞士商+GF+提供自動化所需的夾治具、倉儲和搬運系統,可同時整合串接+GF+本身品牌和其他加工和量測設備等硬體之外;於軟體部分則分為兩部份,在設備方面可搭配由+GF+自主開發的rConnect軟體,經過德國TUV萊茵安全認證,提供客戶與+GF+專屬的數位連線與工程師即時溝通,以及透過手機即時追蹤監控機台稼動率、狀態等訊息。
+GF+同時提供WSM系統,可以針對工件生產排程進行管理,對各站產線產能和倉儲材料進行監控,且與客戶MES、ERP共享資料,進行原物料管理。對於有客製化開發需求的客戶,+GF+也透過OPC UA通訊協定,讓客戶自由選取開發和管理所需的資料,並透過自動化整合了夾治具、搬運系統和軟體,協助客戶達到24/7無人化加工管理目標。
嵩富在生產模擬也搭配Power Milling軟體用於加工前的模擬,使之能更精準減少加工上的誤差;並搭配Renishaw工件量測產品,能直接在機台上量測工件的精度,減少再拆的工序,達到完整的加工精度效益,未來也不排除結合工業機器人進行噴粉、修補。
在整體設備效率上,則除了於機台完成一次性的工序,而提升生產效率及品質效益之外;現也配合執行廠內MES系統,可視化呈現機台生產履歷;讓客戶及供應商可修正系統軟體,共同於系統中滿足各界對於售服維修需求。
**刊頭圖(source:tctmagazine.com)