從技術進化的觀點來看,CNC加工製造的效能要再提升,全面性的使用數位技術是目前唯一的方向。而數位技術的發展,則又以深度的虛擬與模擬為要點。
CNC加工做為數位科技的工業應用之一,一直以來都是專注於物料加工的精度與準度的提升,以及作動工序的改良,使之可在一部機具裡完成最多的生產流程,進而增進整體的生產效能,並改善成本。
然而隨著數位技術的不斷進化,加工品質的改良已不再是唯一的發展目標,現在還要把目光看得更遠,甚至是在生產之前,也就是在設計端就開始著手。要怎麼做到?如何達成?關鍵就是數位分身。
而數位分身應用正進入到它的高速成長,將會快速布署至以工業製造為首的各種領域之中。市場研究機構 ResearchAndMarkets就預期,至2030年,全球數位分身市場規模預計將達到1558.394億美元,從2022年到2030年的複合年成長率為39.1%。主要應用在製造、航空航太和汽車領域的開發與部署,並投入在設計、元件模擬與雙生系統上。
CNC的當代發展與主流技術
然而要知道數位分身與CNC加工製造的關係,還是得從CNC的基本技術原理和目前的主流發展瞭 解起。
CNC為「Computerized Numerical Control」的縮寫,也就是數位控制技術,是透過電腦的數位化指令,自動控制機械設備及加工過程,它的出現取代了手動控制的方式。
一般熟悉的數控工具機主要有XYZ三個直線坐標軸,而多軸是指一台工具機至少具備第四軸。通常所稱的多軸數控加工是指四軸以上,其中具有代表性的是五軸。
CNC數位控制技術的應用,包含機具的智慧監控與線上檢測功能,或者透過運用更多的感測器來強化加工的品質與運行安全,並提供精確且高準度的施工數據,同時檢測機台本身機件的壽命情況,達成預診維修的目標,進而優化廠房稼動率與整體的產能。
另外,透過先進的數位控制器與精準的馬達和螺桿性能,使CNC數控系統與機台具備更高程度的加工生產能力,以達到更多軸與多面向的製造可能,進而實現高速與高精度的切削與加工生產。而可視化的加工預覽,以及自動化智能回饋也是重要輔助項目。
隨著數控技術的成熟發展,在工業4.0及數位分身潮流的推波助瀾下,傳統CNC數控系統於齒輪/螺桿加工亦可靈活運作。包括國內外工具機等OEM設備製造廠商,也紛紛與歐系大廠Siemens、NUM結盟,開發客製化人機介面及模擬軟體,以支援齒輪/螺紋磨削專業加工機,增效節能或數位轉型需求。
為因應高階精密製造、車銑複合或五軸加工的多軸應用需求,過去較為複雜的曲面加工,都須仰仗不斷的試錯開發製程。如今可透過軟體技術發展,實現防碰撞偵測,而這也是未來虛實整合系統切入的重點。
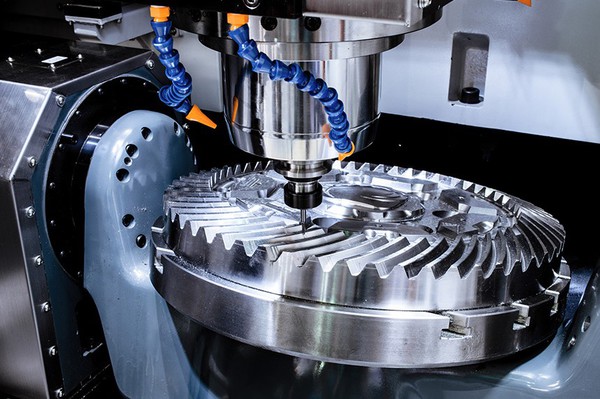
圖1 : 通常所稱的多軸數控加工是指四軸以上,其中具有代表性的是五軸。 |
|
數位分身與CNC加工
數位分身(Digital Twin)又可稱為數位孿生、數位雙胞胎,透過蒐集歷史與即時數據資料,作為現實包括人、商品、流程、系統、機器或生產設備的各種參數,轉移至數位平台上,建構一個完整的模型,模型涵蓋眾多面向及變數,變數之間相互影響,預演將發生的各種變化。
數位分身的應用,包括透過感測器數據判斷機械手臂故障問題,並且利用互動式人機介面進行診斷進而調整;而在倉儲AGV人機協作上,可以模擬整場物流、工序、排程、取物型態、動線、人機協作、動態調整物流資源,以因應少量多樣客製化訂單需求。
而在CNC加工應用上,即在加工前可先透過數位分身模擬製程,或是透過預兆診斷系統,能讓業者預知機台健康狀態,清楚何時該維修或替換零件,得以提升設備稼動率,妥善規劃生產排程。
也因此其核心除了具備模擬模型之外,與真實模型的連結是需要能夠被量化,而其量化的基礎可以被作為智慧化應用,甚至建立新興商業模式。歐洲工具機廠也在產品生產過程中,導入數位分身技術,來活化加速機械產業中的生產流程,以及提供更多的商業模式。
以台灣的東台精機為例,該公司針對旗下的TD系列車銑複合機推出了數位分身應用,其最大的特色就是只需要一台筆電就能進行99%相符的加工模擬、干涉檢查等,降低數位執行系統的負擔。
另一家業者台灣力盟(NUM)也發表了用於CNC機床的數位分身技術,可在開發之前進行設計分析、測試和性能提升,減少機床開發時間和成本,使製造商大幅縮短上市時間。
而數位分身技術的領導者西門子( SIEMENS)也推出一種新世代的數位原生CNC控制器SINUMERIK ONE,能夠串接數位分身系統與實體產品,讓機械設備製造商可藉由利用數位模擬來縮短調適時間,以便更迅速的進行機台開發,或是在虛擬環境中測試零件、改善效能。
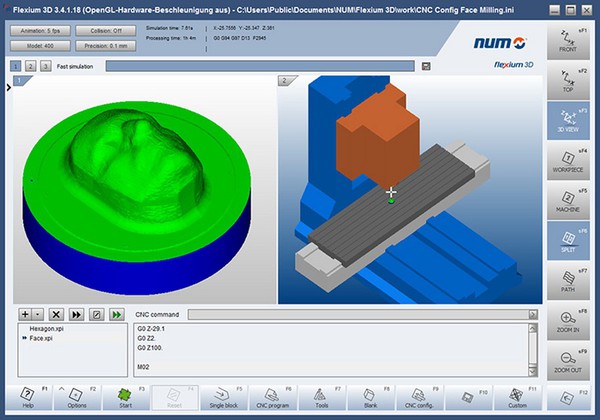
圖2 : NUM CNC系統的3D 模擬功能,能讓操作人員透過預覽與狀態顯示,充分掌握加工資訊。(source: NUM) |
|
運用數位分身來改善設計與生產
從上述的幾個業者案例可以看出,機具導入數位分身的功能或者與虛擬系統串接,已經是當前的重要發展趨勢。而其主要的用途都在於改善設計,加速生產的時程。
在一個以工業4.0為基礎的智慧製造與數位轉型時代,數位分身是其中的重要環節,它能把開發設計逐漸整合至製造執行系統裡,並且延伸到更多元的產業應用裡。近年已有越來越多的歐系齒輪加工專用機大廠,為了提升產品應用的附加價值,而相繼推出自動化解決方案服務,並結合數位分身等科技,以驅動數位轉型。
一般來說,在一個標準的CNC機具裡,只要將程式指令輸入數控系統後,經由電腦編譯計算,並透過位移控制系統,將資訊傳至驅動器以驅動馬達,使之來切削加工所設計之零件,並不會結合數位分身的應用。
由於過去數位分身應用大多以CAD/CAE為主,而機台的機械設計則多以CAE模擬為多,至整機的開發流程大多會分散開發,才可負荷單機大規模製造的生產模式。而近幾年機具設備業也開始朝向如消費性電子產品式的發展,就是生命週期縮短,同時客製化需求上升,因此就需要透過先進的數位化功能的支援下,在產品開發流程的初期,就建立虛擬機台模型。
在開發初期導入數位分身的優勢很多,最大的好處就在於客製化能力的提升。因為產品的設計與分析,都可以透過數位分身進行深入的模擬,除了可以提高與客戶之間的溝通效率,也可以在物件加工之前,就能獲取絕大多數的物件數據,提高良率也縮減誤差。
而在工件實際加工後所得到的真實數據,也可以進一步回饋到數位虛擬模型裡,再做進一步的優化與調整,再提升加工品質,或者調整設計。
所以CNC加工搭配數位分身不僅能直接反映在物件加工的品質上,同時也可以透過事前的模擬與分析,提升產品開發端的效益,甚至是拉高自身客製化的能力。若是再結合人工智慧與大數據的功能,還能讓數位分身具備更多的自主性,屆時產品的開發與生產將會進入全新的世代。
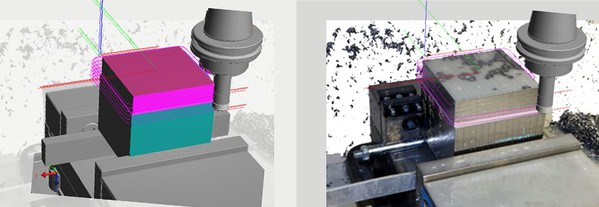
圖3 : CNC加工搭配數位分身不僅能直接反映在物件加工的品質上,同時也可以透過事前的模擬與分析,提升產品開發端的效益。(source:kth.se) |
|
結語
從技術進化的觀點來看,CNC加工製造的效能要再提升,全面性的使用數位技術是目前唯一的方向。而數位技術的發展,則又以深度的虛擬與模擬為要點,換而言之,就是要讓數位與實體密不可分,數位分身也就因應而生。
未來新一代的CNC機台都將會串接到數位的虛擬系統之上設計優化,從虛擬試運轉、生產中磨合部件,乃至翻新與服務,都會是數位分身應用的優化對象。這將為機台製造商省下大量時間,並增進其機台從概念設計到生產過程的品質。
在全球數位化浪潮席捲之下,許多台灣業者已經開始進行數位轉型,設備與技術功能不斷提升,成本也不斷下降,數位分身也將會成為最重要的五大科技趨勢之一。
**刊頭圖(source: DP Technology)