AI模型在各項應用扮演的角色愈來愈重要,為了開發以AI驅動的產品,工程師需要將AI整合至整個系統設計的工作流程。不論是哪一種應用,大部分的工程專案均是以類似的工作流程進行,最後則產生不同的結果。
當各種資料可取用性提高、能夠支援從資料處理到部署的完整工作流程工具的誕生,意味著除了機器人和自動駕駛等最廣為人知的應用之外,AI模型在其他應用扮演的角色也愈來愈重要。
為了開發以AI驅動的產品,工程師需要將AI整合至整個系統設計的工作流程。該工作流程包括四個重要的階段:
AI模型在各項應用扮演的角色愈來愈重要,為了開發以AI驅動的產品,工程師需要將AI整合至整個系統設計的工作流程。不論是哪一種應用,大部分的工程專案均是以類似的工作流程進行,最後則產生不同的結果。
* 資料的準備(data preparation)
* 建立AI模型(AI modeling)
* 模擬與測試(simulation and test)
* 部署實現(deployment)
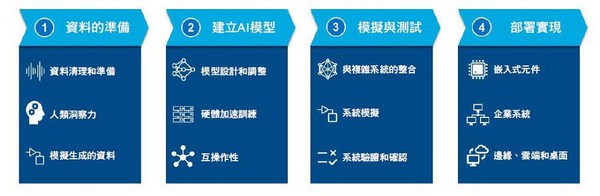
圖1 : AI工作流程的重要階段。每一個階段建構在前一個階段所完成的基礎,並且關聯到未來會被整合至完整AI系統的AI模型建立過程。 |
|
不論是哪一種應用,大部分的工程專案均是以類似的工作流程進行;然而,產生的最終結果卻大不相同,接下來舉例說明。
自動瑕疵偵測
自動檢驗與瑕疵偵測對於高吞吐量生產系統的品質控制相當關鍵,許多產業採用檢驗與瑕疵偵測系統來找出產品表面的缺陷或裂痕,部署AI瑕疵偵測演算法,可以比傳統的影像處理等方法來得更快、更健全。
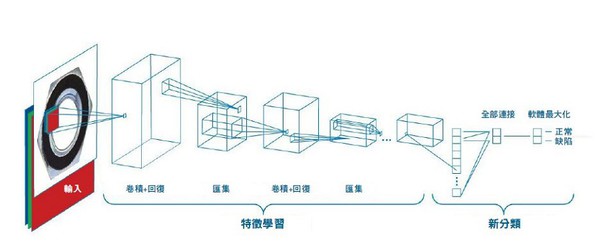
圖2 : 一個簡單的CNN架構。自動地從影像學習特徵,以用來辨識不同等級的物件,在這個案例是正常和不良的零件。 |
|
Airbus建立一個AI模型來自動辨識飛機內輸送管線的瑕疵,他們將飛機內的輸送管線,以不同的照明條件、角度、位置錄製成影片。在進行影片資料的標記(labeling)之後,他們設計並訓練一個深度學習網路,其中使用如語義分割(semantic segmentation)等技術,找出輸送管線上的通風口與線路位置,並且有一使用者介面來即時地呈現瑕疵偵測結果。
MEG訊號解碼
訊號資料使用在AI系統工作流程時,本身便存在一定的挑戰。原始的訊號資料很少被直接加入到AI模型中,原因是訊號資料通常帶有雜訊且具有記憶密集(memory-intensive)特性。
因此,經常會再加上時間-頻率技巧來轉換資料,收集模型學習所需的最重要特徵。工程師可透過多種方式轉換他們的資料,並且使用在AI模型–舉例來說,他們可以透過小波散射(wavelet scattering)的方法將原始訊號資料轉換為「圖片」。
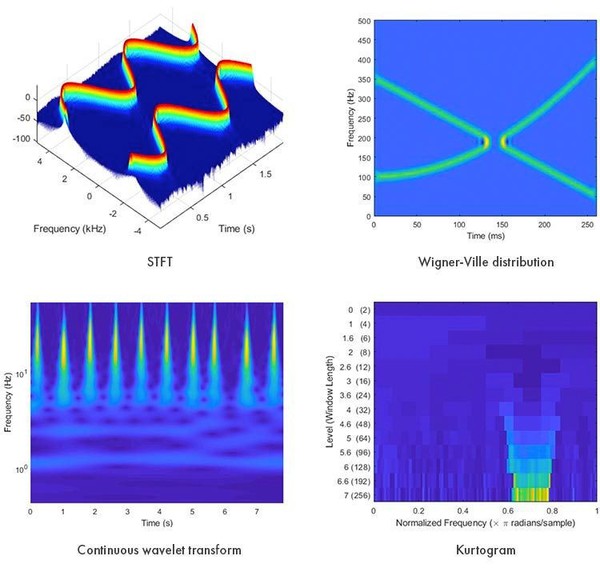
圖3 : 訊號資料可以使用多種方法來轉換。這些圖片可再被使用在CNN架構,以深度學習方法來進行資料的分類。 |
|
對於患有晚期肌萎縮性脊髓側索硬化症(amyotrophic lateral sclerosis;ALS)的病人,溝通會隨著疾病的演變而變得更加困難。德州大學奧斯汀分校(University of Texas at Austin)研究人員開發了一種非侵入性的科技,使用小波和深度神經網路來解碼腦磁波儀(magnetoencephalography;MEG)的訊號,並且在病患想像述說完整語句時,將這些語句偵測出來。
這些研究人員使用小波多重解析度分析來進行診斷,並將MEG訊號分解到特定的神經震盪(neural oscillation)頻段。他們從經過降噪和分解的訊號中擷取特徵,再使用這些特徵來訓練一個支援向量機(support vector machine;SVM)和一個淺層的人工神經網路(artificial neural network;ANN)。這個團隊還接著客製了AlexNet、ResNet、以及Inception-ResNet等三個預訓練的深層卷積神經網路,解碼MEG訊號,讓分類的準確度從80%提高到96%以上。
以雷達為基礎的物件偵測
對於自主車輛來說,若要在夜晚、惡劣的天氣、較遠的距離等情況下偵測行人與其他的物件,以雷達為基礎的系統的表現會比攝影機來得更佳。AI分類演算法可以被使用在雷達訊號來依照物件的特徵來區分出具鑑別性的群組。
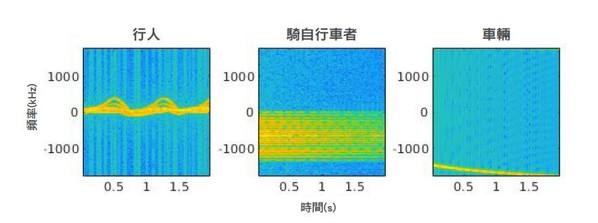
圖4 : 以光譜圖(spectrograms)表示的雷達訊號,用來以具鑑別性的特徵進行三個物件的分類。 |
|
為了達到這項能力,PathPartner的雷達團隊開發了一個以雷達點雲偵測(radar point cloud detection)為基礎的分類器。他們在嵌入式平台上實現了這個分類器,並且真正地在測試場景進行驗證。
在進行早期測試時,這個分類器偵測到一個人需要花上5-8秒,生效時間過長。團隊將訊框時間(frame time)由每秒3幀增加為5幀,並且建立一組以前一組特徵的移動平均值計算出的新特徵,來解決這個延遲。經過測試與快速設計疊代,他們的物件辨識準確率可達到99%。
預測性維護
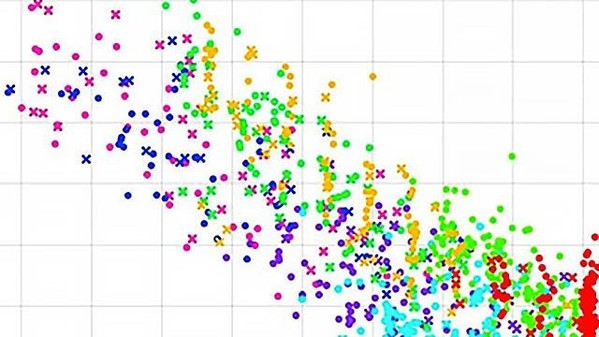
圖5 : 使用Classification Learner app進行故障診斷,其中比較了各種機器學習演算法,在部署實現之前找出最準確的模型。 |
|
因為機器故障而導致的停機,可能為仰賴製造和生產的公司帶來相當昂貴的成本,而部署健康監測和預測性維護系統可以將這些成本最小化,並且讓效率最大化。預測性維護應用使用先進的統計和機器學習演算法,在機器真正發生問題之前,先辨識出機器的潛在問題。
Mondi Gronau的塑膠生產工廠一年的塑膠與薄膜產品出貨量大約有1800萬噸,工廠內900名工人一天24小時、一年365天地操作了大約60台塑膠射出、印刷、上膠、與繞線機。Mondi開發了一個健康監測與預測性維護的應用,其中納入了以機器學習模型產生的預測,這項應用讓設備操作人員可以在故障發生之前,就先接收到關於設備潛在故障問題的示警,Mondi也將該應用做成一個獨立的可執行版本,現在已經在工廠生產線上使用中。
(本文由鈦思科技提供;作者Johanna Pingel任職於MathWorks公司)