繼近年來智慧製造潮流帶動一波生產流程可視化,並打造PaaS/SaaS等創新商業模式之後,接著還可望藉此加速企業數位轉型。台灣機械業則盼利用多年來藉TPS持續改善流程累積的領域知識,與資通訊產業緊密結合,開創更大價值。
隨著資通訊產業在進入雲端時代之後推出的「軟體即服務(Software as a Service;SaaS)」交付模式,又被稱之為「按需即用軟體」,既強調「一經要求,即可使用」,讓使用者僅須透過連網下載存取軟體使用,而不必再經過傳統繁複的安裝步驟,相對降低企業對於採購軟體成本與硬體規格的要求。且具備SaaS最大特徵之一,便是包含組態選項(參數)設定和應用「客製化」,正適合台灣機械業導入用於組裝、生產管理流程優勢之上,創造更大差異化價值。
尤其台灣機械業向來具備中小企業「機動性」的優勢,因為掌握過去與供應鏈密切配合的良好默契,在購入設備決策及預估成本、交期、發包快速,常在接到訂單後未經工程分析、排程,便直接通知上游供貨、備料,再仰賴老師傅的豐富經驗大批量生產,從接單到交貨的週期時間僅以月計。
但在邁向工業4.0階段,卻苦於無法適應更高彈性與客製化需求,導致工作量和機台數據激增,企業規模有越來越大趨勢,更需要改善和消除浪費。惟若透過TPS(Toyota Production System)精實生產管理角度審視現場,卻發現目前加工廠內的物料通常存在加工、檢查、運搬、停滯4種型態,對於客戶真正有價值的加工狀態只占其中不到10%時間。加工廠雖然引進CNC工具機等自動化設備,仍須浪費人力監管生產品質與機器運轉,以及不同階段待加工的大量庫存品。
進而納入智慧機械視角,納入SMB、IoT等多樣智慧化工具之後,才能協助缺乏直接到現場觀察,並找出問題來改善能力的中小企業,避免因為人工抄寫現場生產數據不正確、難以兼顧時效性;以及日夜班生產性差異大,無法充份掌握進度、交期,只能回到辦公室坐等財務報表、ERP(Enterprise Resource Panning;企業資源規畫)系統等數據,與現場確實存在不小差異;且代工廠因為透過貿易商接歐美買主訂單,也開始被要求能隨時提供進度可視化及生產履歷。
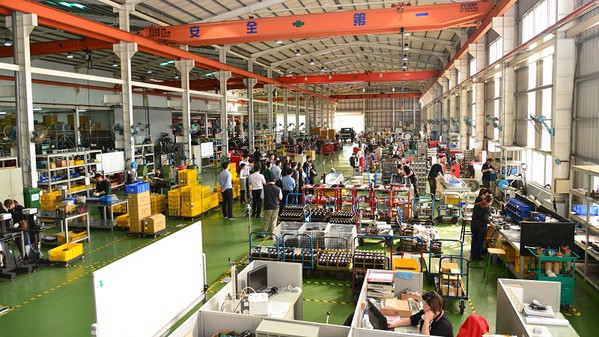
圖1 : 若透過TPS精實生產管理角度審視現場,可發現目前加工廠納入SMB、IoT等多樣智慧化工具之後,可讓機械業者在現場管理時透過IoT平台連網監控。(攝影/陳念舜) |
|
藉此可讓機械業者在現場管理的人、機、料、法準則中,透過IoT平台的sensor、SMB等硬體裝置和通訊協定連網監控,並自動擷取加工過程中的機台狀態、稼動率、老師傅經驗等資料數位化後,形成IoT內容。得以隨時將不同階段的可視化資訊存在於系統,建立生產履歷;或者即時推播到主管手機,即使出差也能監控廠內,不必等到隔日(周)才能檢討改善。甚至上傳機械雲,加入AI簡化、分析後找出新價值,同時解決中小企業既仰賴數據,又擔心供現場精實管理的資訊可靠度不足等問題。
達易智造跨領域結盟 打造金屬加工專用SaaS
基於目前機械設備業者投入自主開發軟硬體整合方案的趨勢已越來越明顯,藉著主動替製造業者把關生產品質,正驅使設備製造業者從過去以單純銷售產品為主的營運模式轉型,逐步朝服務導向企業發展,台灣最早投入打造M-Team聯盟雙核心之一的工具機大廠永進機械,更與IPC大廠研華合資成立「達易智造DZ Connect」。
經由導入研華WISE-PaaS平台為基礎的物聯網產業解決方案(Solution Ready Packages;SRP),並以領域導向(Domain-Focused)解決方案/應用場景之系統整合商與合資共創(Joint Venture Co-Creation)型態為發展重點。同時結合永進機械在金屬加工產業的專家經驗,開發出適合該產業的系統整合及顧問服務等套裝解決方案,工具機廠商透過研華平台,將更有籌碼與其他CAD/CAM軟體商談判合作,或加入不同協定同盟,在人機料法與其他領域產業合作。
受惠於這波工業4.0智慧製造潮流,達易智造市場發展部經理葉建群認為,對於台灣機械業而言的最強大需求,仍來自於數位轉型與二代接班,亟需可在短時間內大量普及工具,有助於中小企業順利接班、轉型,新進人才不只監工,還能改善生產流程,先求把流程作對,接著才能將之數位化改正,達到智慧自動化。
然而,過去TPS制度問世40餘年來,始終只有日本人玩得起的主因,不僅在於執行力高的民族性使然,還有台灣以破碎型產業居多、產品要求彈性高等特性,導致難有足夠人力分工,欲落實TPS管理的代價太大。葉建群指出:「在現今軟體、IoT技術不斷進步,與硬體更便宜之下,已導致設備自主聯網,蒐集大量數據更快又準,不必員工每筆key-in,加上自動排程、領料、派工,同時省下TPS工作量與企業成本;還能確保每批量生產的品質相同,承接穩定與高價值訂單,提供軟體服務也少被砍價,客戶甚至會要求設備要具備機聯網、可視化功能,才願意買單。
達易智造適於此時投入智慧製造應用領域,受惠於雙方能量與經驗積累,除了有領先同業的IT及OT能力之外,亦在金屬成型、切削加工等相關產業具備深厚的領域知識(domain know- how)與顧問能力,協助導入與客製化智慧製造系統。
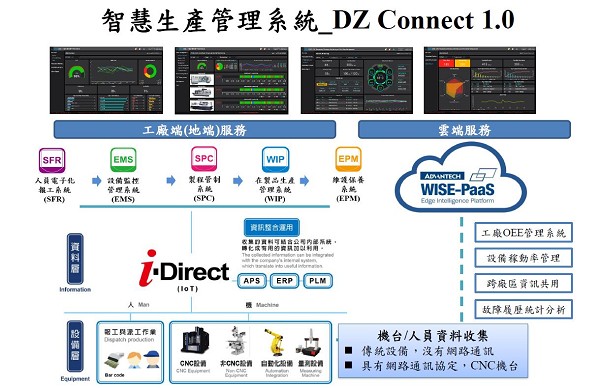
圖2 : 達易智造受惠於雙方能量與經驗積累,協助使用者逐步導入客製化智慧製造系統。(source:達易智造) |
|
目前該公司已能夠透過物聯網設備,蒐集、分析與管理廠內工具機、工業機器人在內的生產機械設備資料,從個別機台的運作狀態、設備產能分析到整廠生產進度等資訊,已有超過130家客戶的現場導入經驗及顧問服務,舉凡航太、汽機車、自行車、模具、扣件及零組件產業,都是達易擅長且經驗豐富的產業。
其中除了一、二線中心工具廠同業之外,放電加工機、沖床、車銑床、木工機等產業機械廠商也都有達易的伙伴,不被金屬加工、設備業視為競爭對手。葉建群說:「有別於早年軟體須搭配機台共同出貨到客戶端的案例約佔70%以上,近年來由於終端客戶對於智慧製造意識的抬頭,加上中小型加工廠開始擁抱新的管理觀念及工具,目前終端加工客戶的比例已提到70%左右,顯見近年來工業數位轉型的熱潮已經快速擴散。」
此可歸功於達易智造相較於其他同業最明顯的差異,除了以TPS精神為核心,讓中小企業能藉由此梳理作業流程,將對的流程數位化;同時採集機台、報工、派工及品質等OEE所需資訊出發,並搭配程式派送、智慧警報系統等,提供全廠人機料法的綜合狀況分析,使管理更為即時,也大幅減少人力與人為疏失風險。
且因為達易智造提供與Microsoft、Amazon同等的IT微服務架構(Micro Service),省下整個專家團隊進駐中小企業,建立ERP的費用。所提供的服務就像是樂高積木一般,可隨客戶需求搭配標準模組或折解重組,加入ERP或自動排程、報/派工等單一獨立系統,或多個APP程式互相支援,組合出符合該公司所需的功能,大幅降低客製化成本,並大幅縮短數倍至數十倍佈署導入期,甚至加入AI分析。
倘若同業中有不同的機型和作業模式時,軟體部份即可利用達易智造的微服務來組合成為該公司專屬服務平台,讓設備製造商可以專注於機台的研發與提升,透過相互搭配產生差異性,讓機台成為服務的一部份,更貼近顧客的日常生產需求。
此外,由於分散式的微服務架構可讓客戶從極小批量著手,快速建立PoC;還有機會彈性擴容,使軟體服務同時在雲端及地端皆能運作,進而達到「雲地共生」架構,讓軟體能完全斷網,同時在異地/雲備份。得以分階段導入單機至整廠,待確保成效後再擴大投資,解決大部份廠商須一次規劃整廠投入的金額龐大,且實際成效未知的問題。
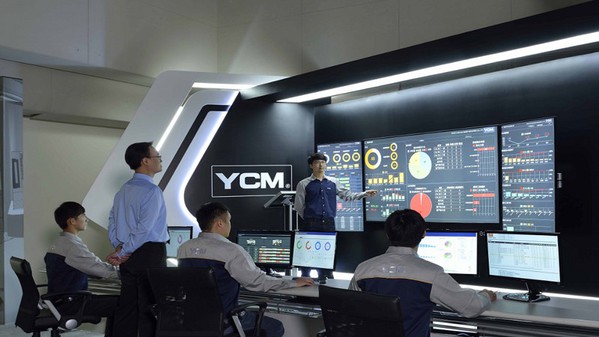
圖3 : 高度整合過的APP,無論在戰情室的各式大小螢幕及手持裝置上,皆可順利運作。(source:達易智造) |
|
進而高度整合戰情室及APP,無論在各式大小螢幕及手持裝置上皆可順利運作及切換,客戶亦可利用達易智造提供的API介面,將現行的標準軟體及APP進行二次開發,或隨意支援多樣種類的IoT硬體及協定連接上系統。
德科智能主推ERP 為零組件另創管理財
另一家出身於工具機產業的德科智能科技(dek),公司背景是關鍵零組件刀庫大廠德大集團,相對更傾向於ERP系統。經過4年努力開發出一套具可視化及跨公司的智能雲端管理平台,強調已跳脫傳統ERP系統只串聯單一公司內部流程,而是囊括整體製造供應鏈的機器設備、訂單、生產、管理、決策資訊,加快速度及降低人力成本。
德科智能科技工程師陳昆志表示,回顧過去台灣機械接到客戶訂單後,必須先用傳真向其上游供應商訂購零件,浪費要列印並傳真給供應商的採購單,就有200份之多,相當耗費時間、人力與資源。等到供應商收到傳真後,開始依單生產,並將每個零件歸屬於哪張訂單記錄下來;之後再由倉管人員依單據逐一點貨、核對,將紙筆記錄的資料輸入電腦,才能完成了一項零件的訂購動作。
過程中有許多環節可能發生錯誤或延遲,影響後續的生產效率與服務品質,必須積極思考該如何以科技的方式改善,加快整個供應鏈管理的正確性與效率;連帶也可提升服務品質、加快交期,連帶就能維繫更好的客戶關係。
近年來德大機械開始改良ERP系統之後,開始要求所有配合的供應商都一起導入,不管從採購到送貨、點交,全都可以透過這套系統來統一串流處理,加快了整個零件採購及收送貨速度;還能主動通知生產管理人員安排組裝,也大大降低各環節的人為疏失,既有效率,又可節省成本。
然而,由於台灣的製造加工廠多為中小企業、規模並不大,難以負擔一般市售ERP系統動輒數百萬元的高價。尤其對於多樣、客製化程度高的不同領域終端加工業者而言,最期待的就是刀具管理,是所有數位串流的盲點。陳昆志表示,為了提升加工效率和產品品質,過去這些年德大機械一直與工研院保持緊密合作關係,合作範圍也逐步從單機智能化,擴大發展到系統智能化連結生產設備及系統的軟體。
即將上市的軟體內容包括:智能化供應鏈聯網ERPnet系統、VMX機聯網軟體平台、先進規劃排程(Advanced Planning & Scheduling;APS)、機台稼動率監控、組裝及加工可視化、切削提效(Speed Pro)軟體等技術銷售與推廣,全方位優化機械業的供應鏈生產體質,讓使用者透過手機就清楚掌握跨廠區的生產狀況,提升全球競爭力。
其中ERPnet供應鏈聯網系統係針對客戶/廠商/供應鏈間的溝通聯繫,從接單、採購、生產、組裝、出貨等營運流程,進行雲端聯網管理。除了省去溝通協調流程,並可準確預估訂單交貨時間,實現緊湊生產、縮短交期的目的,即使買不起ERP的供應商,也能直接上網接訂單、回報交期,讓客戶及業務部人員變得更輕鬆。
接著搭配與工研院、加工業者合作開發的APS(自動生產排程優化系統)軟體分析,讓現場機台達到最有效率的生產,減少生管部門接單後的生產排程調整、採購單傳真、訂單異動處理、物料比對跟催等工作,大幅降低66%的人力。
在採購部門則可透過智能化交期回覆功能,無傳真、無紙化,縮短與供應商之間的溝通工時,相當於降低88%的工作時數;在品管部門自動產生自檢表,節省每月50%的工作時數。
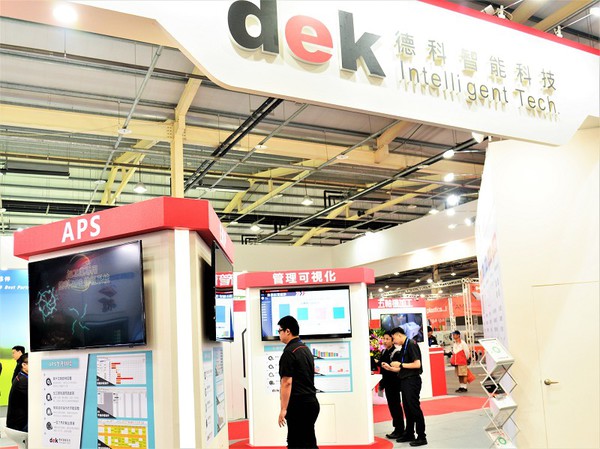
圖4 : 德大機械近年來一直與工研院保持緊密合作關係,合作範圍也逐步從單機智能化,擴大發展到系統智能化連結生產設備及系統的軟體。(攝影/陳念舜) |
|
陳昆志指出,透過德科智能的ERP平台將潛藏問題檯面化、廠區狀態即時化、管理效率數據化、企業產值極大化後,納入產品從業務、採購、生產排程、加工、組裝、品管、庫存、財務等各環節的相關資料,詳加統計分析。
在業務部門可藉此透過電腦與行動裝置,即時獲取各類型統計報表→圖表,全盤掌握公司各項營運指標的趨勢與細節;於組裝時透過機側觸控面板點選問題,再回報指定人員;加工階段,則可協助加工業者讀取不同工具機廠商的可視化資訊、參數,再與APS整合,或在戰情室串流上下資訊。
總結
「嚴格來說,工業4.0也可稱之為TPS的數位版本,與實體現場管理相輔相成,都是企業達成數位化的工具之一。」即使回顧台灣製造業智慧化演進過程,也是先經過製造→服務化;接著在約20年前開始引進ERP系統推動數位轉型,卻因為與現場資訊脫勾,而功虧一簣。直到目前始藉著現場設備自動化程度不斷提升,加入APS/SCM/MES系統、CAD/CAM/PLM等智慧製造軟硬體達成各階段數位化之後,才有利於針對產品完整生命週期有效管理。
如今台灣機械業因為已先行投入改善現場管理人機料法,嘗試最有效的改善方法還是透過TPS精實管理。2006年工具機產業甚至組成M-Team,以及2012年透過工業局、國瑞汽車輔導下深入鑽研TPS制度,於推動智慧化腳步不輸德、日大廠,已約有50%中小企業藉機聯網引進智慧化工具;5%能將蒐集得來的資訊透過AI、大數據分析,來協助找出看不到的問題。
剩下50%中的20%廠商則認為連結機台後,還須加入自動排程系統,並導入MES呈現;其餘20%廠商在10~20年前便已建置完成ERP。但執行至今的成效不彰,主因即在於ERP數據往往與現場即時資訊不一致,恐造成執行決策偏差,有賴現場人員透過自動報工、設備機聯網、物料QR-code自動辨識等工具,提高資訊準確度。
所以建議業者導入ERP系統前,務必先了解整體生產流程,確認應導入項目及可取得利益;並透過TPS認清問題、找出有效解決方法,重新找回中小企業「機動性」特色,而非視之為理所當然,成為無法改善的陋習。
**刊頭圖(攝影/陳念舜)