在彈性製造的產線設計中,輸送系統是非常關鍵的一環,所有的協同作業都必須透過實質的產線連接,此一連結不僅是物理性的機械,也包括資料的通訊,不過目前傳統的生產輸送仍然問題重重。
生產輸送問題重重 彈性電驅輸送系統可解決
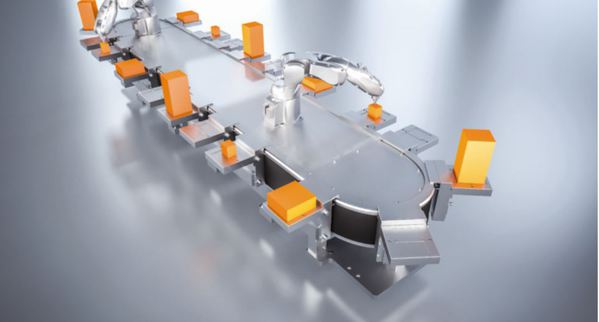
圖1 : 採機械式設計的傳統輸送帶不但容易故障,而且採固定式設計,難以因應現在智慧製造的彈性化生產需求,彈性電驅輸送系統則以電驅加上磁浮技術,讓工廠產線更靈活。 |
|
首先是機械磨損,現在的輸送系統採用機械鏈條、不但會產生磨損也會帶來較大額度噪音,而且會需要例行性維護,維修也更為複雜,必須耗費大量的維修等待時間,造成產線OEE下降,另外傳動精度也有限。
第二個問題是各站之間的位置不能靈活變動,現在製造業急單、插單的比例越來越高,產線彈性的需求大幅提升,而一旦出現變線需求,機械必須花費大量時間重新調校。
第三是缺乏資料溝通與設備協調難度高,傳統輸送機制無法與控制系統、生產系統進行資料交換,更難以融入到數位化設計的建模中,對要求必須與數位化設備、機器人高精度協同的智慧製造系統,將成為系統盲點。
第四是產品換型週期長,每次調整產線需要進行拆裝,重組,花費較多的時間,最後則是輸送、上料、加工、下料過程複雜,尤其對於加工工序較多的生產而言,非有效加工時間占比較高,如此將造成產線冗長。
彈性電驅輸送系統則解決了上述問題,此系統是在由線圈組構成的直線軌道上運作,動子滑塊可以在X軸方向移動,而這個軌道可以為直線、彎道各種形式,可以構成不同的產線形式。
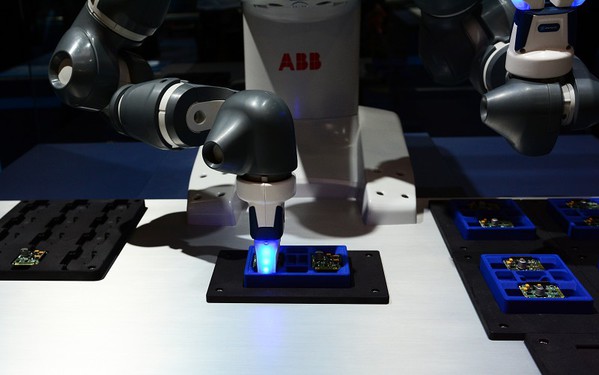
圖2 : 彈性電驅輸送系統是為了解決生產制程中傳統產線的問題,此系統為典型機電一體化設計。(source:B&R) |
|
由於軌道後的線圈會產生磁力,與滑塊的永磁體產生水準方向的排斥力推動滑塊的運動—這與伺服電機原理一致,只是這個是切開的伺服電機,而且與普通直線電機不同在於它的滑塊數量是眾多,以貝加萊的SuperTrak軌道為例,此軌道最大可以達到50公尺長,而滑塊間距可以在200mm左右分佈,最新的ACOPOStrak已經規劃的單個專案可以達到320米長度,500個滑塊,滑塊最小間距50mm。
機電一體設計 可與Digital Twin整合
由於變軌過程是採電磁方式,因此變軌過程中不會造成如傳統機械的磨損,而透過電磁系統,也可以將產線的位置等資料進行回饋,管理端可完整掌握輸送帶的動作、位置與速度等資訊,對要求整合製造現場資訊的工業物聯網來說,彈性電驅輸送系統可主動提供資訊,將數據納入管控平台,有利於管理人員判斷其狀況。
另外,彈性電驅輸送系統也可以因應產線要求進行客製化設計,例如將小型的軌道設計出像F1一樣形成一個「維修站」,當有瑕疵品被檢測出來後,即可送到此處,同時此一「維修站」還可以作為更換工裝夾具的地方,讓維修和更換夾具並不影響當下產線。
彈性電驅輸送系統是為了解決生產制程中傳統產線的問題而設計,此系統是典型為機電一體化,可與新世代產線的Digital Twin鏈接。
Digital Twin是整合數位化設計與實體物件,以虛擬建模方式驗證產線,並可直接下載到實體物件的控制器中運作,而實體物件的運行過程可以即時在虛擬環境中數位化呈現並調整,
Digital Twin的好處在於可預先規劃與驗證產線,在專案未進入安裝之前即可驗證其可行性,另外也可在虛擬環境中調校控制邏輯、同步關係;而在Digital Twin的設計中,即可納入已經數位化的彈性電驅輸送系統,讓設計者在初期就可實際掌握整體產線運作狀態,落實智慧製造願景。