德國在2012年提出工業4.0概念後,各大製造設備供應商與各國政府紛紛跟進,提出類似的智慧製造概念政策,雖然各國政策內容不一,不過仍有其交集之處,現在的智慧製造概念,是讓製造業中各企業運作包括IT與OT各環節的數據可被擷取、儲存、運算、分析,再依需求做出各類決策與指令,而要達到此目標的前提是,所有數據都必須數位化,透過數位化,後端的系統才能進一步處理相關資料,也因此,數位化會是打造智慧工廠的第一步。
提升自身價值 因應市場環境
對於這次的智慧製造趨勢,參數科技(PTC)資深協理汪崇真指出,無論是工業4.0或智慧製造,強調的是價值而非製造,也就是回歸製造業本質,全球消費行為改變驅使產品生命週期縮短,製造業者如何滿足客戶少樣大量、少樣少量需求,成為贏得訂單的條件之一,企業必須提高製造生產效率與應變客戶需求能力,才能創造產品附加價值進而維持競爭力。
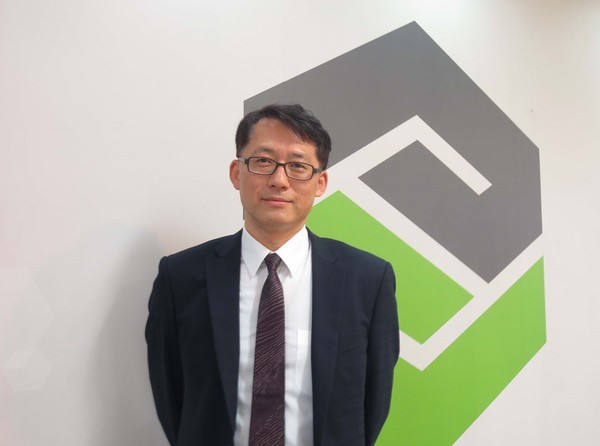
圖1 : PTC資深協理汪崇真指出,大數據是知易行難,他建議製造業可以借助專業廠商的力量,協助企業完成「行難」這部分的工作。(攝影/王明德) |
|
製造服務化、服務創新是台灣製造業升級轉型的重要途徑,是無法單純靠產品品質來維持競爭優勢,尤其台灣越來越多製造業為了邁向國際市場,在有限資源底下持續不斷創新,除了產品創新外,管理、流程、組織創新,創造產品附加價值等各層面都必須同步跟上,才能在競爭激烈的市場中站穩腳步,
從整體來看,現在製造業面臨的市場態勢是客戶的急單變多、產品生命週期縮短、產品類別少量多樣,在此態勢下,製造業者必須提升生產效率、速度、靈活性,以因應未來少樣單件所帶來的挑戰,如生產效能、庫存管理、物料採購,進而縮短產品上市時間,提高產品種類擴大需求,滿足個性化生產需求等,要滿足這些需求,就必須從數位化著手,透過數位化,讓OT與IT系統的數據可以無縫串接,從而延伸出更多系統功能與價值。
例如讓製程管控可視化,將工廠的產品製程,包括原物料管控及流程,均可直接即時的展示,利於全盤掌握製程的現況,而由於製程中所蒐集的相關數據,均可保留在資料庫中,透過妥善的資料採礦管理,決策者可以進行完整的資訊分析,以進行後續的生產規劃,或是根據生產線的現況,規劃生產機具的維修保養。
或是可全方位系統監管,讓製造設備具有完整的感知能力,以感測器做連結,讓控制系統可以進行識別、分析、推理、決策、以及控制功能。企業建立一個擁有完整設備資訊及回饋機制的資料庫,透過系統平台累積的各種資訊,讓決策者更能掌握產品完成時程,像是透過各類軟硬體的應用,建立內控預警機制,從訂單開始到產品製造完成、入庫的生產製程資訊,都可在資料庫中一目了然;當遇到製程異常時,決策者可更為迅速反應,以促進有效的工廠運轉與生產,提供即時客戶服務。
Digital Twin讓設計更精準
除了製程管理外,在產品設計端早已採用數位化技術,近年來無論在技術或應用都仍持續強化,PTC I*Center Taiwan MCAD技術總監鄭景懋指出,過去的設計多只能靠經驗傳承,透過數位化,則可以將這些無形的經驗完整保留,且具體的再次呈現,同時透過數位工具的邏輯判斷,讓設計者在設計時,對產品更有洞察力、更理解產品。
他以PTC的CAD平台Creo 4.0在賽車設計為案例指出,Creo 4.0在2017年加入可結合AR與IoT應用的Digital Twin解決方案,可為客戶帶來更精準的設計,過去的賽車設計,都是設計師在電腦上模擬車體與環境的狀況,像是引擎中的進氣閥角度、氣流、溫度等,最後再將結果輸出,製造出實體車輛,並讓車輛在路上反覆實測,逐步調整各部件的位置,此一過程必須不斷重複,且未必能調整出最精準的設計。
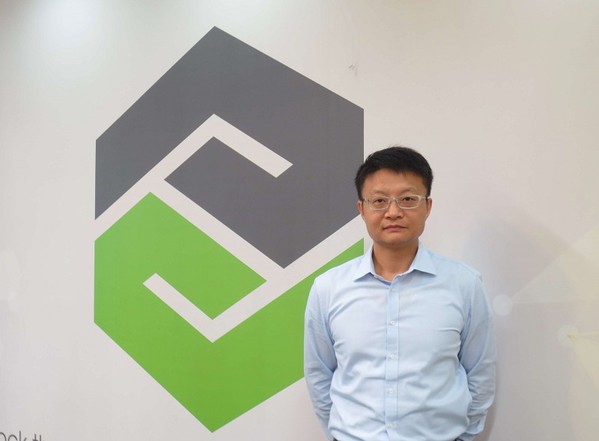
圖2 : PTC I*Center Taiwan MCAD技術總監鄭景懋表示,產品設計端早已採用數位化技術,近年來無論在技術或應用都仍持續強化。(攝影/王明德) |
|
Digital Twin的方式則是在車體各部件中建置感測器,由感測器紀錄引擎進氣閥的各種連續數據,在電腦系統中建立起數位模型,設計師可依據來自現實運作的數據,讓設計可以一步到位的貼近實際應用狀況,不再經過重複的假設與調整流程,不但可縮短產品上市時間,同時還提升產品品質。
釐清需求 劃出智慧藍圖
透過這些數位化平台與工具所架構的智慧工廠,這幾年市場已快速成形,再加上經過廠商不斷的市場教育,現在已開始有製造業者導入相關架構,對此汪崇真認為,智慧化將可提升製造業競爭力,不過他也建議製造業者在導入智慧工廠時,必須先畫出完整藍圖,如此方能清楚定位每一步建置的背後意義,後續導入的系統也能完全鏈結。
導入智慧工廠必須從設備數據的採擷開始,目前已有台灣製造業者著手建置大數據系統,汪崇真指出,數據的採擷是為了解決問題,不同問題所需要的數據類型不全然相同,例如馬達預修診斷,就必須取得震動數據,要提升設備稼動率,就需要設備的運作時間,因此製造業者必須先行釐清本身要解決的問題,不過他也表示,現在多數的決策者都知道智慧工廠要做大數據,不過大數據是知易行難,大家都知道很重要,但要實際做出來會困難重重,對此他建議企業可以借助專業廠商的力量,像是PTC就已有相關的專業平台,協助企業完成「行難」這部分的工作。
汪崇真最後也提醒製造業者,智慧製造系統屬於全新概念,在導入時必須與原有的程序搭配,例如食品廠的原料配方管理或組裝廠的機器手臂等,稍具規模的製造商在導入智慧製造系統前,都已有相關的製程或管理制度,新系統的導入必須與這些舊的做法融合,如此方能減少磨合期,同時讓製造系統更貼合需求。
**刊頭圖(Source: MSPoweruser)