@前言:因應製造業歷經從大規模量產到多樣化、體驗時代,達梭系統,也在日前舉辦「體驗時代的製造業」大會上,發表隨之從現實、虛擬到虛擬+現實整合各階段的3DEXPERIENCE Twin平台,並引進AR、AI等工具,加速製造業從數位邁入體驗經濟時代。
向來致力於3D數位設計、模擬和產品生命週期管理(PLM)解決方案的達梭系統(Dassault Systemes)不僅近年來持續推動3DEXPERIENCE平台有成,並積極配合中國製造2025、台灣智慧機械等政策,落實於智慧製造。進而在今(2017)年11月7~8日再度於上海舉行的「體驗時代的製造業(Manufacturing in the Age of Experience)」大會,向現場超過1,700位產業合作夥伴,與40位媒體及分析師發表最新3DEXPERIENCE Twin虛實整合平台,以及結合擴增實境(AR)、人工智慧(AI)等工具,在各領域的實際應用。
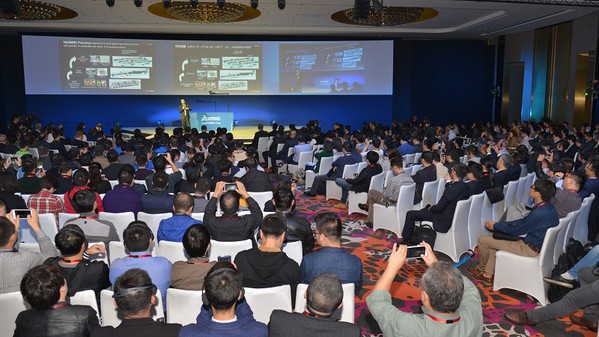
圖1 : 達梭系統在「體驗時代的製造業」大會中發表最新3DEXPERIENCE Twin平台,並結合AR、AI工具在各領域的實際應用。(攝影╱陳念舜) |
|
其中,主要透過規劃、模擬和執行全球生產流程來協助製造創新的達梭系統DELMIA首席執行長Guillaume Vendroux分析,自2001年起全球化浪潮興起後,曾吸引眾多新興經濟體加入搶奪市場,達梭系統也積極協助各國實體大規模生產消費者買得起、品質尚可的產品,再依客戶需求小幅修改,適用傳統試錯方式,使得供應鏈非常穩定。但到了2010年以來,產品上市週期變得越來越短,消費者除了接受標準品外,也開始要求須融入在地化特性,以快速調整功能配置、增加服務比重,促使製造業必須調整生態,改變以往仰賴的大規模生產方式,而強調多元化生產。
時至今日,面對當前製造業要求必須同時快速生產,且符合客戶使用者習慣的高質量產品,不僅過去提供的預設配置及功能,顯然已無法滿足消費者多樣需求。製造廠商除了被動回應市場需求,還須主動適應市場,以隨時滿足未來產品的生產方式、基地等需求;在各環節都開始融入「體驗式」生產,以加速或同步反應市場變化,才能避免被淘汰的命運。Guillaume Vendroux表示:「數位化模擬只能加快產品設計,卻無法預測未來的生產方式是否可行?」
因此,傳統線性供應鏈必須加入更多提供服務功能的人、機構等,所有與產品生產相關資源;並協同管理整個供應鏈、服務端,徹底改造價值、供應鏈,才能快速提供高度定製化產品,滿足單一消費者、客戶需求,讓製造廠商可依「我的」訂單來生產;並以水平/協同方式管理,確保在各個生產環節投入更多物流、資訊流,來提高生產速度與效率。Guillaume Vendroux指出,有別於過去產品一生產出來就能獲市場青睞,目前須依市場需求才生產,導致產品變得越來越複雜、上市週期更短,以往的試錯方式已不再適用。而須透過新一代3DEXPERIENCE Twin平台,利用即時數據來建構虛擬3D模型,不斷調適未來單一產品。
在達梭系統所提出的應用方案裡,即包含如何藉由旗下CATIA、SolidWorks等軟體設計產品,進一步透過DELMIA、3DVIA等服務規劃生產流程、空間應用,模擬整個工廠產線運作,除了活化工廠運作之外,更能透過數據判讀挖掘產線全新價值,進而作出更好發展決策,同時也能讓產線人力等資源發揮更好應用效果。
共築華為雲體驗平台 協助中小企業數位化轉型
此外,在今年大會還特別邀請華為技術公司(HUAWEI)副總裁何非出席主題演講,分享該公司雲戰略生態系中有關智慧製造的主題。係針對現今中國大陸製造業面臨挑戰,對於採用雲端解決方案的需求不同,尤其可在開放公有雲服務企業時,看出個別企業所處規模、階段,對雲的理解殊異。估計在未來5年內公有雲的滲透率越來越高,而傳統大型企業除了公有雲外,還會加速扶植託管私有雲迅速成長。
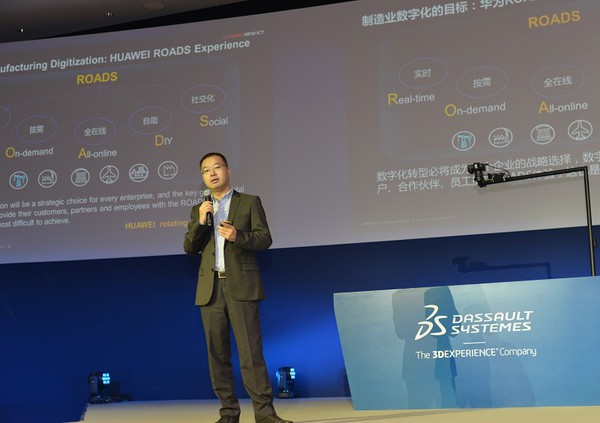
圖2 : 華為技術公司副總裁何非在主題演講中,分享該公司雲戰略生態系中有關智慧製造的主題,強調將提供客戶、合作夥伴ROADS體驗。(攝影╱陳念舜) |
|
何非表示,數位化轉型既將成為每個企業的戰略選擇之一,而數位化企業的關鍵目標就是提供客戶、合作夥伴「ROADS(即時、滿足需求、線上化、自助、社群化)」體驗,華為與達梭的共識,則是通過「雲服務」來提供製造業高度整合、低成本的數位化轉型,將是產業升級的必經之道,進而追求從點(單元)、線(產線)、面(工廠)來實現整體數位化製造。
如華為公司現有18萬員工中,僅有2,000~3,000名員工從事製造,卻可每年生產出1.5億部手機、全球超過40%以上的基站等有線與無線產品,創造出6,000億人民幣產值,即有賴於先在深圳基地建構完全標準化、數位化生產線後,以數位化技術打通從研發設計、生產元件到產品、生產線製造全流程等所有資訊源頭著手,並將資訊化覆蓋到每個角落;再借重達梭系統強大的3D模擬情境能力,通過閉循環迴路快速發現問題,大幅縮短試製、驗證週期;且納入業界大廠SAP的ERP系統,讓物流和製造系統通過IoT平台,提高生產、發貨效率,快速送達全球174國。
最後再把這些年與合作夥伴在電子製造業累積的經驗、大數據在公有雲平台上共享,並輸出到富士康、偉創力等所有合作夥伴上雲後,都能從中萃取大量相關參數,並找到適合自己的解決方案,達成資訊化改造,降低中小企業升級門檻。目前除了已先提供在「華為雲(Huawei Cloud)」上運行3DEXPERIENCE平台的解決方案,以充分利用華為在高效能運算雲(High Performance Computing Cloud)的優勢,和達梭系統豐富的產業經驗外;未來雙方還會共同定義相關的上市和銷售模式,以建設開放、共贏雲的生態,確保能為各產業客戶提供最佳整合解決方案。
藉助3DEXPERIENCE Twin 從數位化邁進體驗式經濟
達梭系統董事會副主席兼首席執行長Bernard Charles最後總結,與一般認知不同,製造業約從30年前導入電腦輔助工具,進而縮短飛機設計週期或控制工具機、機器人等自動化設備開始,就已正式進入數位經濟時代。達梭系統則很早就注意到數位化的重要性,並嘗試透過模擬分析的方法來跨越虛擬和真實,重新定義整個設計世界。也因為對於製造生產過程更瞭解,促使在設計產生新理念,認為:「創新雖是生產製造的核心,卻無法只靠設計來達成。」
數位化的第二層涵義即是「模擬」,也就是在虛擬世界測試越多,就越能掌握有效解決方案,確保最終產品質量能滿足客戶需求,達梭系統也期望能透過每年舉辦「體驗時代的製造業」大會,來擁抱全新的數位化解決方案。
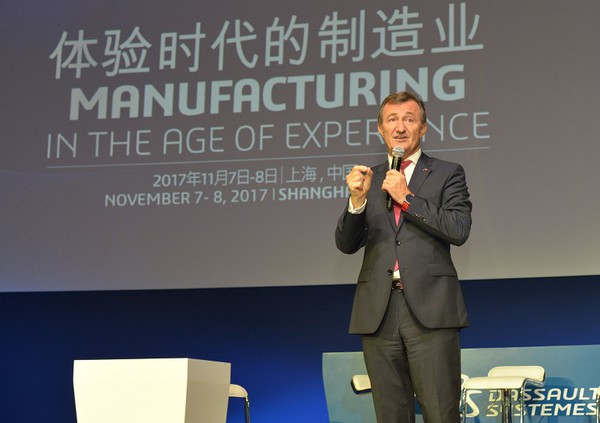
圖3 : 達梭系統董事會副主席兼首席執行長Bernard Charles總結,單純製造高質量產品的真正價值係存在於體驗的過程,可讓企業有更多動力創新。(攝影╱陳念舜) |
|
在這次也發現單純製造高質量產品已不足以滿足客戶需求,真正價值係存在於體驗的過程,又稱為「體驗經濟」,可讓企業有更多動力創新,3DEXPERIENCE Twin平台將有助於企業將新思維與生命週期管理高度整合。包括:1.促成「V+R,虛擬(virtual)和真實(real)」世界合一,讓想像成真;2.創造價值網路,而不只限於供應/價值鏈;3.擴大社會影響,即可藉該平台整合所有知識,讓任何人都更容易理解、使用。進而在工廠、車間教育人員以提升技藝,不必靠學校就能打造出高素質的工作團隊。
聚焦AI、AR布局 確保各生產環節虛實合一
在會後記者會上,Guillaume Vendroux再度強調在這次大會中首度提及的「3DEXPERIENCE Twin」應用,主要集中在製造工程領域,將使得設計得以共享,並即時虛擬呈現,快速轉化成為真實的「雙引擎」驅動能力。除了可協助探索未來,經過不斷輸入現行流程的更多數據、模擬科學,來看出未來可能的生產軌跡外;還能執行3D模擬來表達需求,再善用企業管理和營運體系,重新蒐集或分配一系列參數,確保能實現每個生產環節。
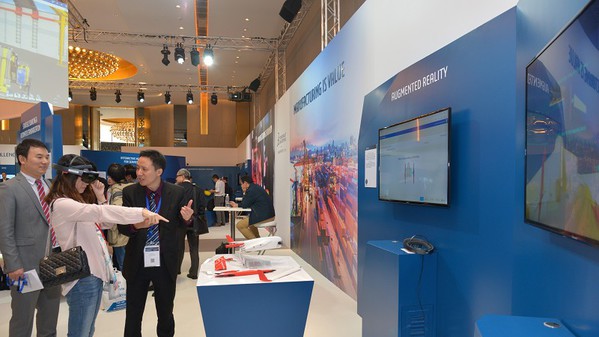
圖4 : 3DEXPERIENCE Twin應用主要集中在製造工程領域,進而讓員工沉浸於VR/AR模擬任何一種產品的生產流程,或從事嚴苛、危險工作。(攝影╱陳念舜) |
|
進而讓員工沉浸於VR模擬任何一種產品的生產流程、組裝、操作步驟,或從事嚴苛、危險工作,以提升效率和安全性,甚至可以跟真實物體進行AR互動,用來訓練,考核員工。達梭系統EXALEAD執行長Morgan ZIMMERMANN表示,接下來3DEXPERIENCE平台確實有與AR/VR相關應用,且與現今主要客戶提供的AR/VR服務一致。但他也坦言,過去AR發展的瓶頸是系統不一,必須透過感測器連結,現在則可經由3DEXPERIENCE平台連接AR/VR,用於設計製造、科學實驗,或生產過程的遠端監控,而成長關鍵仍在於未來AR載具能否提高可攜性、舒適度,才能創造更高價值!
至於在AI人工智慧應用的領域,也已獲得許多客戶採用,未來達梭系統將會著重在於怎麼樣從大數據流中找出某種規律及模式,透過用戶找到數據的特徵,以提升生產效率與最佳化。例如利用類似圖像辨識的技術,就能重新檢視物流供應鏈,並作出相對應的戰略,將有效降低供應鏈成本支出及提高效率。Morgan ZIMMERMANN還分享了以下幾個實際應用情境:優化採購流程、即時成品優化與監測、分析工人動作數據、提升物流效率等。他強調:「在 3DEXPERIENCE 平台當中,不會讓數據科學家躲在實驗室裡面,而是要落實於生產線。」
除了AR、AI之外,達梭系統在2018年仍將朝向如何提升整體工作效率,從生產的角度來說,希望在整個過程當中都能透過數據分析作出明確的決策,讓產線能達到連貫性與持續性,在 3D體驗時代當中,可以做出預測、行動,然後提供全方位的服務。Guillaume Vendroux表示,達梭系統在過去幾年來持續創新,卻也專注於「可用性」,為了縮短不同產業從工程設計到生產、交付的距離、時間,3DEXPERIENCE Twin平台透過數據連續化整合,將逐漸取代中間MES/ERP隔閡,建立改由客戶驅動創新的模式。