製造業面臨的競爭日趨激烈,消費者的喜好瞬息萬變,造成產品生命週期愈來愈短,客製化產品日趨多樣,製造成本亦跟著難以控制,加上更加複雜的其他因素變項,使得廠商必須隨時面對不穩定的訂單、少量多樣的生產及生產良率的控制等相關問題,如何從中找出一個能夠同時提升生產力及競爭力的關鍵策略,成為廠商有志一同的關切方向。「智慧工廠」的發展,為廠商提出了新的方向。
以智慧工廠角度出發,從清楚掌握產銷流程、提高生產過程的可控性、減少生產線上人工的干預、即時正確地蒐集生產線數據,以及合理的生產計畫編排與生產進度等,都是業者提升競爭力及生產力所必須掌握的關鍵項目。在生產過程中,包括產品及設備乃至於生產線的狀態監控,在智慧工廠的發展上,的確形成相當重要的發展課題。
環顧工廠製造的發展歷程,早期主要是讓「人」來照顧機台;在自動化導入後,雖然建立大量標準化規則,並透過程式系統加以控制加工生產,但仍然需要「人」監視機台,製程資訊亦需要透過人工抄寫,統計資訊內容亦不甚完整,甚至在設備維修上,也需要透過人的「經驗」累積。
系統軟硬整合 建構智慧工廠
一直到整合平台、軟體、硬體及機台的共同發展,逐漸形成「智慧工廠」概念,才使得廠商從單純的製造業,成為「服務型」的創新產業。自動化技術改革了製造業,歐美因此成為工業先進國家,之後在大陸低廉勞動力搶佔製造商機,世界工業聚落逐漸東移;但由於近年勞動人權較為提升,加上自動化技術發展加快,歐美製造業以電腦人工智慧取代傳統人力的趨勢逐漸明朗,從自動化轉型為智慧化已成為製造業的新興浪潮。
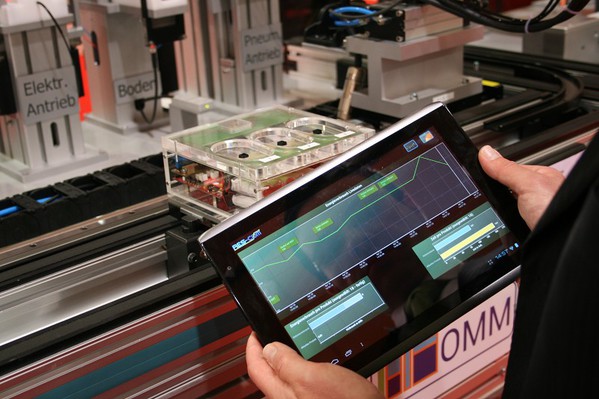
圖1 : 整合平台、軟體、硬體及機台的共同發展,逐漸形成「智慧工廠」概念後,製造業者從單純的製造業,成為「服務型」的創新產業。(Source: Festo) |
|
智慧化的概念目前仍相當模糊,而且一般智慧化常會與自動化混淆。兩者最主要的差別,在於自動化只是單純的控制,智慧化系統則是在控制端加上資料採擷,採擷後的資料必須能無縫傳送到後端累積成龐大資料庫,管理系統再依據資料庫的訊息,分析、制定出正確決策,而這些決策同時也附加自動化設備與以往不同的功能,例如設備本身所建制的感測器,可以記錄設備的動作次數或使用時間,提醒管理者進行維修。
智慧製造的目標,簡單來說,即是將人工智慧融入製造過程的所有環節中,系統直接可以自動監測生產線運作過程,亦可自動調整、自動組織,甚至「最佳化」在製程中整合設計、加工、控制及管理等過程,以適應外界或內部的變化環境。
掌握所有環節 擴張製造智慧
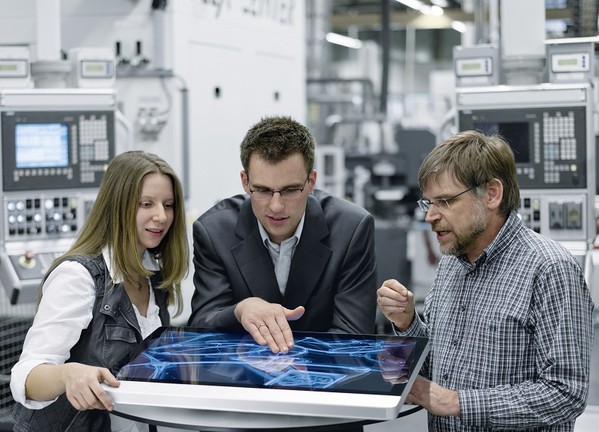
圖2 : 透過量測設備與系統的軟硬體整合,可以在日趨複雜的生產製造環境中,建構更完善的產品製造及檢測模式,讓製造更為「智慧化」。 |
|
(Source: Fabricating Metalworking)
1989年,日本提出「智慧化製造系統」國際合作計畫,從1992至1994年進行可行性研究,建立六項工業界主導的「可行性國際合作測試案例」,包括《流程工業潔淨製造》、《全球化製造同步工程》、《21世紀全球化製造》、《全方位製造系統》、《快速產品開發》、《知識系統化》等智慧系統;此後經過10年的努力,包括日、美、加、澳、歐盟、挪威、瑞士及南韓等七大地區工業界、學術界及研究單位發展出的智慧製造技術的共通平台,以及21項研究計畫,可將智慧製造系統大致歸納下列五項特徵:
一、系統具有自主能力:可蒐集與理解外界及自身的資訊,並以之分析判及規劃自身行為。
二、整體可視技術的實踐:結合訊號處理、推理預測、仿真及多媒體技術,將實境擴增展示現實生活中的設計與製造過程。
三、協調、重組及擴充特性:系統 中各組承擔為可依據工作任務,自行組成最佳系統結構。
四、自我學習及維護能力:透過系統自我學習功能,在製造過程中落實資料庫補充、更新,及自動執行故障診斷,並具備對故障排除與維護,或通知對的系統執行的能力。
五、人機共存的系統:人機之間具備互相協調合作關係,各自在不同層次之間相輔相成。
從智慧製造到智慧工廠,基本上系統的發展均依照這五項特徵為基礎,作為後續變化的支撐,而這些特徵,也成為工廠自動化的重要特色重點。
此外,在近年自動化趨勢逐漸開始重視機台的智慧化,尤其是可以自我檢測其零件壽命與效能的Smart Machine浮現檯面,這類需求主要來自於生產線大量使用或是不能出錯的大型機具上。由於這類生產線對產能與人身安全有諸多要求,對於設備的狀況監控(MCM)存在較高的要求,也形成另一層面的挑戰。
軟硬交互兼施 掌握產品設備
以目前來說,自動化產業最擔心的就是停工的成本。由於自動化設備每個零組件壽命不同,如果總是在設備出問題之後才進行維修,除了維修頻率將會隨著零組件老化速度不同而顯得難以預測與控制以外,設備的損害規模也會隨著時間而無法預期。
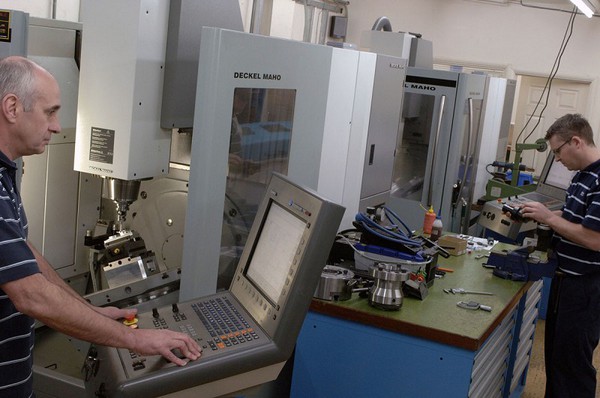
圖3 : 要達成智慧化的目標,因應複雜生產環節的量測設備,絕對是必要的重點。 |
|
當然,除了工時的損失,不必要的額外零件損害都是必須考量的因素。但由於IT技術帶給工業生產資料庫、資訊傳輸等技術的發展,讓生產系統的能力得以優化,通過對基礎生產資料的採集來分析生產流程的整體狀況,使得工廠不再是由單一機器構成,而是整合成為一個整體,因此必須對其進行全局的資料整合降低生產成本、消除浪費,以提升整體工廠運營效率。智慧工廠的對系統的全方位監管,就成為設備及零件生命周期管理的一項利器。
智慧工廠系統監管部份,由於智慧製造的設備,必須具有感知能力,以感測器做連結,系統可進行識別、分析、推理、決策、以及控制功能;這類製造裝備,可以說是先進製造技術、資訊技術和智慧技術的深度結合,而透過量測設備的軟硬體設備整合,也讓系統自我監測的能力更為完整。
要達成智慧化的目標,因應複雜生產環節的量測設備,絕對是必要的重點。而量測需求的逐漸複雜化,也造成設備硬體的模組化趨勢,當然此類系統的建置,仍須透過系統平台「累積知識」,來建立設備資訊及反饋資料庫,這則有賴於量測系統軟體及函式庫的多方整合。因此,透過量測設備與系統的軟硬體整合,不但可經由訊息整合的方式精確測知系統設備的健康程度,也可以在日趨複雜的生產製造環境中,建構更完善的產品製造及檢測模式,讓製造更為「智慧化」。
**刊頭圖片(Source: DFKI)