在塑膠射出產業中,要兼顧品質與大量生產兩大目標,模具尺寸精度是最重要的關鍵。要達到模具尺寸精度,除了仰賴工程師的經驗外,業界最常見的方式即為總體補償法。
總體補償法為使用整體平均收縮率來進行預放縮水,這種方式在產品收縮率一致的情況下不失為一個好方法;然而大部分產品在不同部位的收縮率往往並不相同,甚至可能有極大落差,如此一來便無法符合實際需求。傳統上多以試誤法來使產品符合規格,但此方法既耗時且成本高,甚至有時經過了無數次的試模,仍很難同時滿足所有規格目標,造成模具因無法修改而被迫丟棄。
為免除上述困擾,業界常利用CAE技術來診斷試模過程,在產品與模具設計階段就能及早發現潛在問題,其中翹曲問題是最直接影響產品的精度或組裝上的正確性。對此Moldex3D提出了「全方位體積收縮補償法」,針對產品不同部位潛在的收縮行為進行不同的預放縮水。此方法能快速使所有部位同時達到目標精度,有效改善翹曲。
以下以簡要方式說明全方位體積收縮補償法的流程。圖1為一個L形模型,(a)圖是目標設計的幾何形狀及尺寸(TD);(b)圖為以Moldex3D模流分析軟體針對TD的翹曲模擬結果 (STD)。接下來為能更清楚了解產品三維收縮的行為,將收縮程度分別以X、Y、Z三軸來表示,再依此收縮程度逆向補償回TD,而經此修改後的設計變更就視為補償目標設計(CTD),如圖1(c)。最後再對此項設計變更進行模擬,其分析結果就視為模擬補償目標設計(SCTD),如圖1(d)。經過此補償效應後,可以發現SCTD非常接近TD。
(a) TD: 目標設計(即產品尺寸)。
(b) STD: 模擬目標設計,為TD的模擬結果。
(c) CTD: 補償目標設計,基於STD的收縮程度逆向補償回TD。
(d) SCTD: 模擬補償目標設計,為CTD的模擬結果。
接下來以手機殼案例作說明,其幾何模型尺寸如圖2所示。該手機模型在組裝上有十二個規格,而各規格尺寸公差都不同(如圖3)。
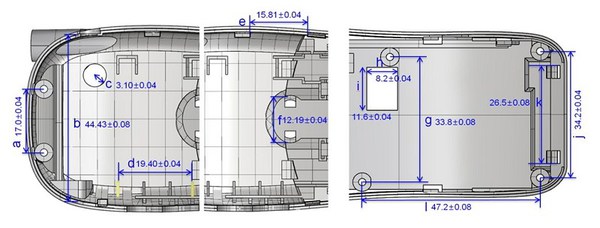
圖3 : 手機模型分成三個部分(上圖),a~l為十二個規格及尺寸公差(下圖) |
|
圖4為手機模型的全方位體積收縮補償法模擬結果,由STD-T1可知,每個規格的偏差值都不同,表示每個點收縮的方向都不一樣。考量整體的收縮行為並逆向補償回TD,將得到CTD2作為新的模具設計;CTD2的模擬結果則如SCTD2所示。顯然12種規格皆可符合期望目標,證明全方位體積收縮補償法是解決翹曲的最佳方法,可有效減少試模人力及成本,並加快生產製程。
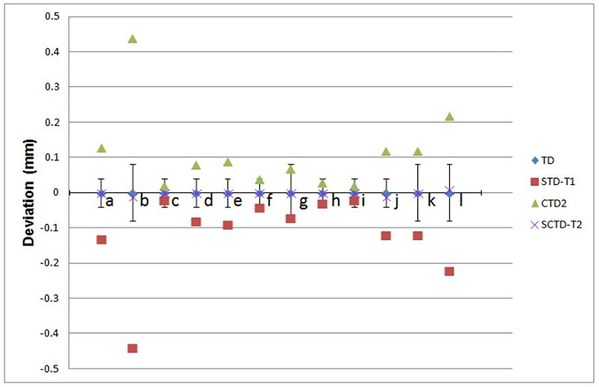
圖4 : 全方位體積收縮補償法。(TD:目標設計 STD:模擬目標設計(T1:原始製程) CTD2:補償目標設計(使用三維收縮率作補償) SCTD-T2:模擬補償目標設計) |
|