隨著環境意識的抬頭加上技術不斷地突破,近年來電動車的發展可以說是相當的火熱,普遍來看,電動車在面對既有的技術瓶頸,從操作上的流暢度、基礎建設、電池壽命等相關課題,已漸漸能有所突破,所以進一步來看,電動車的所需要的電池容量及其模組管理技術能否突破,可說是電動車接下來還能不能再進一步成長的重要關鍵。
撇除電池容量與穩定性不談,從晶片乃至於電池模組的電路設計若能有所突破,會有哪些效益?TI(德州儀器)電池管理解決方案大中華區市場與應用部門經理文司華博士表示,對電動車的駕駛來說,最為在乎的課題,不外乎是加速性能、電力還能讓駕駛開多久的時間,車載資通訊系統本身是否能告知駕駛,相關的電力資訊就成了相當重要的關鍵。
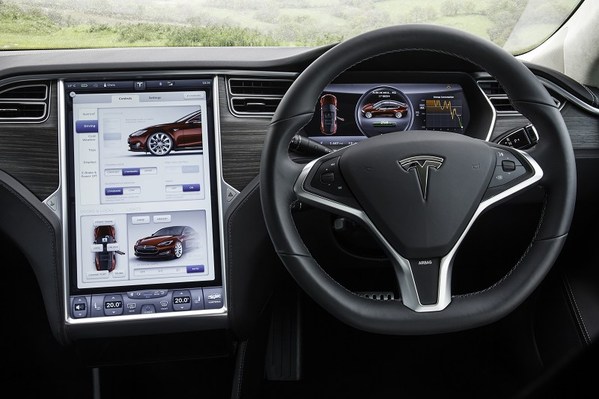
圖1 : 電動車與內燃機車輛相同,行駛距離、可用的電力與加速表現等,都是駕駛十分在意的基本要件。(Source:Tesla) |
|
就電動車的分類上,大體上可分為油電混合與純電動車兩大類別,不論是何種類型,因應道路難易度或是其他因素的不同,形成了不同的設計需求,各大電動車廠在設計BMS(電池管理系統)時,在電池串並的方式與輸出功率就會出現形形色色的設計架構。
文司華分析,不同類別的電動車對電池能量、功率密度、續航里程和溫度特性有多方面不同要求,所以無法設計出通用的電池模組。所以,車廠也只能針對電動車在充放電安全和可靠性上的要求,盡可能地精益求精。BMS系統以及其中電子裝置的性能在保證電動車安全和可靠性上,擁有核心作用。文司華也認為,未來BMS將進一步提供更加快速穩定的電壓、溫度採樣,更加精準的電壓電流測量,加強抵抗電磁干擾(EMI),提供多層次防護,並通過提高整合度來顯著改善BMS的可製造性(manufacturability)和成本。
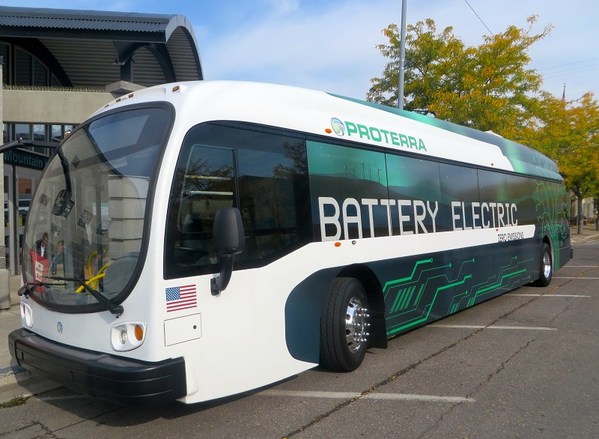
圖2 : 因應不同環境或是需求,電動車對於電池功率、串並方式等,都會有所不同。(Source:www.electrans.co.uk) |
|
就設計架構來看,大體上仍然不脫數位與類比電路彼此搭配的精神,以數位電路而言,仍然不脫MCU(微控制器)的討論範疇,類比電路則是要考量到電池電量的監測與保護。
MCU扮管理角色 中央、分權皆可適用
從MCU的角度切入,瑞薩電子汽車應用行銷部主任黃源旗表示,BMS基本上所在意的重點,仍然不脫:低功耗、高可靠度與安全性等這三個面向。市場上的電動車所使用的電池種類大致上可以分為兩類,一種是我們所知道的鋰電池,另一種則是鎳氫電池。前者就安全性上相對不是那麼穩定,原因是鋰的特性較為活潑,很容易引起爆炸或是燃燒。所以像是電池模組業者或是車廠在BMS設計上,都十分強調保護措施,以日系車廠豐田(TOYOTA)為例,從單顆電池、電池組再到整個BMS,每個環結都設下了保護機制,以確保在駕駛上能夠安全無虞。除此之外,BMS也十分強調監控功能,相較於保護機制,監控功能則側重駕駛者能有較好的使用體驗,其中最在意的,莫過於電池壽命能否進一步延長。在電池充放電時, 最重要的是每個電池芯之間的平衡調整確保電池芯不會過度充電或放電。
黃源旗談到,因應各大車廠的需求不同,大致上BMS的設計可分為兩種不同的架構,一種是「中央集權」的模式,所有的電池模組都交由一顆32位元的MCU來進行管理,另一種則是「地方分權」,各個電池模組皆使用一顆16位元的MCU來進行監控,之後再將資訊交給32位元MCU進行統一管理,作法上沒有對錯。最大的差別就是地方分權的作法,成本會較為高昂。他也談到,BMS所使用的MCU的規格並不會相當複雜,基本都會有CAN BUS的傳輸接收功能、UART、SPI與12位元的ADC(類比數位訊號轉換器),演算法的部份,大致上也是由車廠所把持,瑞薩原則上就是提供MCU為主,現階段也沒有與類比元件業者共同開發BMS的參考設計方案。
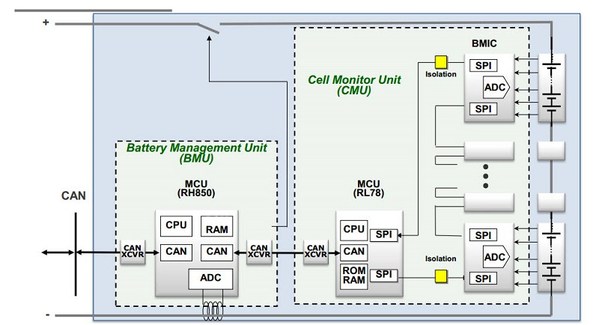
圖3 : MCU在BMS設計是不可或缺的角色,差別就在於,設計架構上,要如何貼近車廠的需求。(Source:瑞薩電子) |
|
BMS設計雖然可以區分成數位與類比兩大類別,
但兩者彼此還是要互補,前者負責管理控制,後者則負責監測保護,
如此才能發揮效益。
但說到底,仍然不脫成本、性能與體積之間的平衡。
種類大不同 類比電路設計學問大
回到類比電路的角度,文司華透露,在BMS設計上的電池數量與排列取決於眾多因素,包括電動車的類別、總體功率和能量的設定、電池芯的類型選擇等等。
電動車的類別會直接決定對的BMS的設計方向。混合動力汽車(HEV)對動力系統的功率密度要求較高,而純電動汽車(EV或BEV)的電池動力系統的總體能量和功率要求高。PHEV系統中,電池作為動力的比重有變化落實到電池選型上,BEV由於為了滿足能量要求往往採用大量的單體電池,那麼功率的要求比較容易達到。
在主流的BEV系統裡面,BMS的電池排列需要接近或超過96個單體電池串聯以達到400V左右的總電壓。例如特斯拉和NISSAN Leaf部分型號。如果選擇18650圓柱電芯,需要很多電池並聯,例如特斯拉某款車型需要74個電池並聯。而由於NISSAN Leaf某款選用大容量Laminate電池,則只需要兩顆並聯。
文司華指出,BMS監控和管理晶片的選型主要跟電池串聯數量有關,也即電池電壓有關。目前業界單顆BMS類比前端晶片能夠監控的數量(亦即通道數)為6~16節串聯電池。電動車的電池動力系統中包含的電池模組的數量與選擇的BMS監控晶片的通道數關聯。以96節總串聯電池為例,如果BMS晶片的通道數為6,那麼總共需要16個模組串聯。如果是12通道,則需要8個模組。
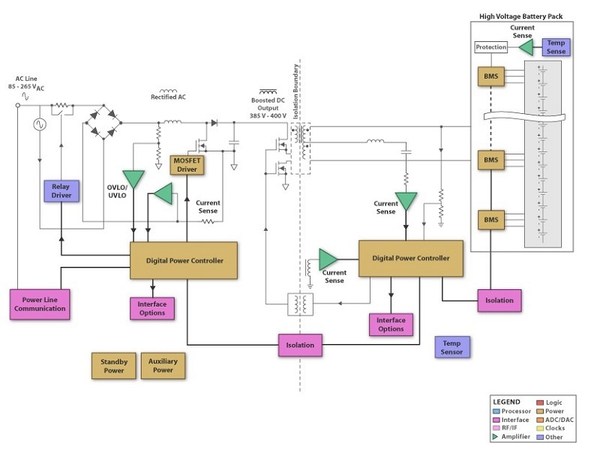
圖4 : 從圖中來看,不難看出,除了MCU外,類比元件也在BMS設計上頗具重要份量。(Source:TI) |
|
電池電力輸出表現亦是重要課題
BMS的表現,決定了電動車續航力與駕駛體驗的重要關鍵,但在電力輸出之後的穩定性與開關損失的控制,也是電動車整體功耗能否降低的重要關鍵。
Vicor資深工程師張仁程談到,Vicor過去一直以來,就是致力於開發高功率密度兼具體積微縮的電源模組產品,從電池模組提供出來的電壓送到各大電子系統時,仍要經過「降壓」的程式,但考量到各個電子系統本身也需要被保護,所以在電源設計上就必須加上穩壓設計,才能避免電子系統遭到高壓電破壞或是突波干擾的情況發生。
實務上,DC/DC電源有兩個作用,一個是作為12V鉛酸電池的充電電源,另外一個是直接給車上的12V的電源系統供電。在同時考量到電動車的安全性與整體電力傳輸的設計時,穩壓設計實乃必要的設計環結,作法上,可以從BMS端的電力輸出時,就採取穩壓設計,或者是在各部次電子系統整合穩壓電路兩種,張仁程直言,兩種作法在實務上,都有車廠採用,所以Vicor在方案的提供,也是採取同時並進的方式。
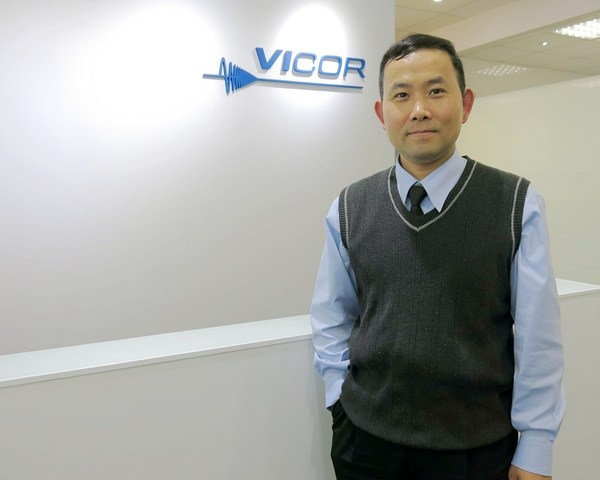
圖5 : Vicor資深工程師張仁程(攝影:姚嘉洋) |
|
張仁程進一步談到,在DC/DC電源端,穩壓與否也決定了該電路的能源效率,在沒有穩壓的情況下,Vicor能將能源效率提升至98%,在有穩壓之下,效率則能提升至92.5%,雖然效率略為下降,但與其他競爭對手相較,仍是居於領先的位置。兩者除了能源效率有差異外,電壓輸出範圍也有所不同。採取穩壓的作法,輸出電壓的範圍較小,約莫介於12至15V之間,客戶可以依照實際需求利用類比式電路的分壓電阻的作法來調整電壓高低,若客戶沒有太多的想法,通常Vicor會先給定13.8V給客戶。張仁程補充說明指出,需要穩壓的原因主要是需要對鉛酸電池充電,因此有可能會根據鉛酸電池的電壓而改變DC/DC轉換器的輸出電壓。若是數位電路,可以通過數位控制的PWM(脈寬調變)信號來改變輸出電壓的設定。
在電動汽車中,特別是混合動力類型,動力艙的空間是極為緊湊的,DC轉換器的體積也是衡量標準。所以若採用體積小的電源管理模組,對於整體設計來說,一則解決空間問題,二則對於散熱與重量也有相當的助益。
Vicor商務拓展經理陳歷忠也補充說明談到,他同意,在汽車電源設計中,客戶還是會有穩壓電路的需求,如果在前級電路就採用了非穩壓方案,後級還將增加穩壓與降壓電路,貌似增加了系統複雜度和成本,但是Vicor所提供的母線轉換器能達到極高的轉換效率,而且實現了電氣隔離,後級只需要非隔離降壓即可,其實現難度和成本並不高。
結論
雖然電動車這幾年的火熱發展,可以歸納於諸多技術或是環境瓶頸被逐漸突破,但若要進一步有所成長,關鍵還是動力來源本身,是否可以提供更長時間、更舒適與更佳的操作體驗?不論是數位抑或是類比電路控制,都不難看出彼此之間必須相互配合,才能找出最佳的解答。而性價比與系統體積等基本要素的最佳化,似乎也是電動車BMS無法擺脫的宿命。
@刊頭圖片(Source:www.abb.com)