因應航太產業向來具備嚴格品質系統認證且高複雜的整合技術,不僅向來被世界各國均視為國家產業技術能力指標;近來更隨著亞洲航空市場需求不斷增加,被看好是未來20年內少數能維持明顯成長的產業。隨著該產業即將成為下一波台灣工具機製造、加工廠商競逐主流,未來如何加工所需航太用的非鐵金屬材料:鋁、鈦、鎳基合金及複合材料等,讓業者須不斷積極尋求更完善的刀具系統解決方案。工研院也與加拿大哥倫比亞大學(UBC)持續密集合作,支援業者開發所需高效率加工設備及應用技術。
針對航太零組件加工 法人提供高效應用技術
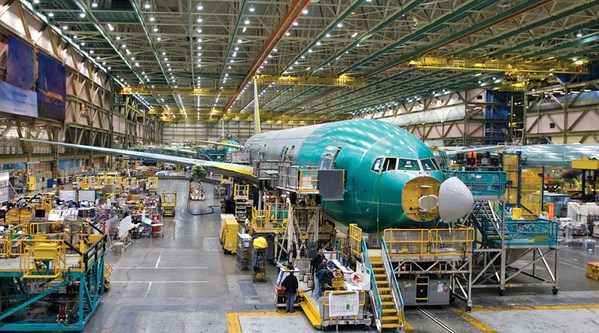
圖1 : 航太產業需具備嚴格品質系統認證且高複雜度的整合技術(source:3dprint.com) |
|
工研院智慧化工具機技術中心數位製造技術部經理彭達仁進一步分析,如航太用零組件要求輕量、高剛性及高可靠度,導致其不用鑄造工法,以免因鎖孔增添應力疲勞風險,而改用工具機大量移除90~95%以上塊材、滿足高效率製造需求。卻在加工後容易形成薄壁特徵,造成工件加工時震動更甚於一般模具,現今設備製造商除了考量End User加工時刀具、機台之震動外,還要加上工件。
因為所採用的鋁、鈦/鎳基合金等零件材質、尺寸及樣式有明顯特性差異,須對應加工設備之速度、加減速、剛性及構型、主軸扭力等不同特性,而有高度專用化趨勢。包括切削鋁質材料時須靠高轉速加工,使得精修之切線速度達700m/s、主軸轉速15,000rpm以上,進給之響應性與加減速度要夠高、夠快,以免過慢會「黏刀」;反之,加工鈦/鎳基等難切削材料時,僅要求低切線速度約30m/s及低轉速600rpm,但剛性要夠高,才能滿足增加的進給與加減速度。但他也強調:「當不斷提升機台結構剛性和切削效率後,最後受不了的恐怕是刀具,而必須利用刀具中心高壓/液態氮冷卻技術,達到更有效冷卻、潤滑。」Makino、MAG便分別透過高壓冷卻和特殊礦物潤滑油,以及加入刀具中心液態氮等冷卻技術,減輕刀具磨耗,延長使用壽命。
此外,針對切削過程中產生的振動來源約可分為:低頻(機台結構、傳動系統振動)、高頻(刀具、薄壁工件、主軸)。彭達仁指出,因為主軸與刀具系統並非剛體,而由軸承、夾爪、彈簧等多個零組件構成,在切削時都會震動,導致無法單憑理論計算剛性。須藉由加速規敲擊刀具等動態特性量測,得知Stability lobes(切削穩態圖)和機台頻率響應函數(FRF),才能清楚掌握機台切削性能;經實際加工測試也發現轉速與切深才會影響顫振,而非扭力與進給量。
彭達仁認為,End User在加工鋁合金時,幾乎可忽略低頻因素,反而應更重視主軸動剛度造成的影響較大。至於以低轉速切削鈦/鎳基材料時,則由於刀具自然頻率增、顫振少,遇到的高頻問題小,而以刀具磨耗問題居多,恐導致頻率能量失效,結構頻率的問題較大。此外,在加工發動機等薄壁件時,因低頻使得製程阻尼更嚴重,抵銷刀具振動,常須處理的是薄壁件帶來的振動問題,而非刀具。
到了要求移除量大,以免加工時間更長的航太加工產業,只要能有助於縮減工時而提升產能的價值更高,導入模擬切削分析技術也更有意義。工研院也因此導入加拿大哥倫比亞大學的數位製造模擬技術,透過Stability Lobes(協助End User在適當轉速、切深範圍內加工,避免顫振;設計者也能事先得知機台構型,加以改善。
精密機械研發中心(PMC)去年也同樣與工具機四強友嘉實業、永進機械、百德機械、崴立機電結盟,催生「切削顫振研究聯合實驗室」啟用,希望提升工具機產業附加價值,最高可提升切削加工效率達30%。PMC董事長嚴瑞雄表示,在工具機切削加工過程中,常會面臨刀具振動引起的加工不穩定現象,在工件表面留下顫振刀痕;當刀具再次經過這些刀痕時,就會引起更大的振動,在工件表面產生更深的刀痕,造成工件表面的波浪形和較大的粗糙度並且加速刀具的磨耗。導致刀具或工件損壞,並造成切削品質難管控、效率低落,浪費重做時間及成本。
友嘉實業副總經理林肇嘉也指出,該過程過去只能憑老師傅經驗解決,沒有科學數據、產生加工盲點,無法即時回應顧客需求,造成失單、退機等問題。在「切削顫振研究聯合實驗室」建置後,即進駐了4家聯盟廠商最暢銷的機台為載具,提供大量且科學的機台實機操作數值做為佐證資料。期待透過顫振預測、建立切削力係數資料庫、工具機切削性能測試,提供業界最精準、最科學的數值,有助於提升切削加工效率、縮短生產周期,讓台灣工具機產業朝高品質之路邁進。
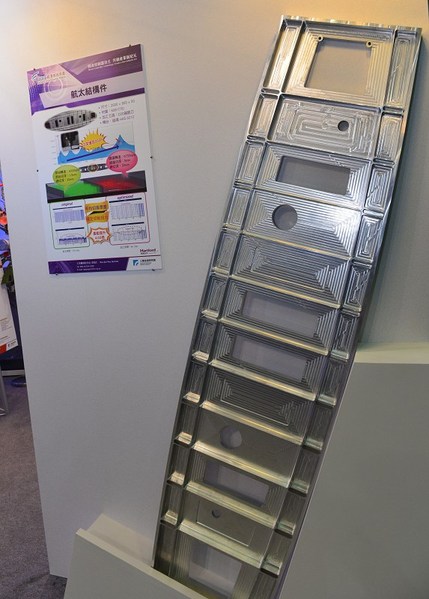
圖2 : 針對航太零組件加工特性,法人也與加拿大哥倫比亞大學密切合作,支援業者開發所需高效率加工設備及應用技術。 |
|