PLC近半世紀的歷史,在硬體發展上已相當成熟,尤其在半導體技術的進步,同時讓PLC的效能全面升級;在此同時,PC Based控制器則對PLC帶來威脅,市場普遍相信PC Based控制器與PLC將會共存而各司其職,使自動化系統效能更全面。
就技術面言,有兩項議題對PLC有較大影響,一為內部技術的大幅提昇,二是外部技術的威脅。
先從內部技術提昇分析,PLC在1969年問世後,在各自動化廠商相繼投入下,技術發展相當快,但經過一段時間後,陷於當時科技水準,PLC的架構一度停滯,沒有大幅變動;但直到半導體技術成熟後 ,PLC因此再次升級,成為目前日趨精緻的架構。
由於半導體技術帶動了CPU的快速發展,在摩爾定律加持之下,CPU的運算速度成幾何成長,運算速度加快且價格不斷下跌,讓PLC廠商得以透過較以往更佳的運算核心,增加PLC的能力。
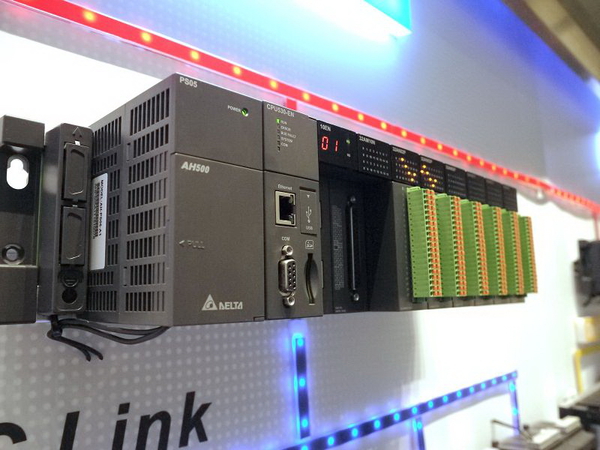
圖一 : PLC近半世紀的歷史,在硬體發展上已相當成熟。 |
|
另一方面,在PLC的CPU掃描後,CPU會擷取所有輸入點的訊號先暫存在記憶體中,隨後執行程式邏輯運算時,直接取用輸入訊號暫存區內的資料做判斷,而不是即時從現場擷取訊號。同樣的,要輸出的控制訊號也不是產生一個就輸出一個,而是先存放在記憶體中的輸出訊號暫存區,掃描周期結束時再將訊號集中輸出,因此除了CPU外,記憶體對PLC而言也相當重要,以往PLC多採用EPROM或EEPROM作為可程式記憶體,在快閃記憶體(Flash)大量普及後,PLC的元件價格不但更低廉,而且也進一步強化效能。
半導體產業加持 PLC效能大幅擴充
除了運算功能,半導體技術也讓PLC增加更多可能性,以往PLC多只負責單純的控制,在高速CPU的加持下,類比訊號處理、閉環控制、網路通訊或高速I/O等,不必再像以往,必須內建特殊功能模組來完成。
單一強大效能的CPU,降低了PLC的架構複雜度,大幅提昇了穩定性與運作速度,同時也縮小了PLC的外觀體積,當然連帶也降低了成本。這也造成目前小型PLC的功能日益加強,直逼中型裝置,但體積亦逐漸「精緻」,也造成PLC的應用,不再僅侷限於傳統工廠自動化環境。
經過現在半導體技術加持過的PLC,不再限縮於傳統的控制領域,而能比較廣泛應用於製程控制中;加上隨著擴充性與通訊能力的提高,PLC已經成為各種複雜的分散式控制系統的重要組成部分。
不過在此需要一提的是,儘管PLC的效能提昇了一個層次,這類強大效能CPU多只應用於大型PLC上,中小型PLC由於應用領域不需複雜控制,對運算速度的要求也不高,高效運算核心並不見得實用,因此部分廠商將高效CPU的技術轉型研發功能完整的SoC,將CPU及硬體處理電路 (HLS)、記憶體、週邊電路等整個系統整合到一個BGA包裝之晶片,讓一顆IC就是整套系統,不但使體積大為縮小,可靠度也大幅提高。
相較於以現有商用CPU組合其他元件所製成之PLC,其穩定度、處理速度及精度自然大幅提升;但這類研發SoC的模式,時間與金錢的大幅度損耗,除非是專業PLC以長期眼光規畫,此類設計模式仍有其困難度。
挾工業電腦氣勢 PC Based控制器來勢洶洶
外部的威脅,主要來自於PC Based控制器的挑戰。PC技術成熟後,廠商開始將觸角延伸到各個角落,在製造業,為了有效整合與管理製造現場資訊,再加上工廠新的自動化設備出現,如視覺檢測、高速擷取資料、資料統計分析及快速定位等,這些軟硬體均為PC Based架構,因此工業電腦廠商開始思考,以PC Based控制自動化設備的可能性。
PC Based穩定度仍有疑慮
PC Based控制器問世後,由於廠商號稱此類產品功能強、周邊技術支援多、相容性佳,與管理層的管理軟體可以輕鬆互連,不過PLC廠商則指出,PC Based控制器的不穩定終究將使它無法存活於工業環境。
雖然工業電腦廠商一再宣稱,已針對PC Based控制器的不穩定問題進行改善,不過這未必能說服既定印象已深的製造業者,至少就目前來看,PC Based控制器在製造業,並未獲致工業電腦廠商當初號稱的成果。
PC Based控制器發展至今,雖未能全面攻佔PLC地盤,不過也已切割出另一領域,尤其是在單純的加工環境,如實驗室、半導體前段製程、替代某一部分CNC工具機、中央監控系統等,就現況來看,PC Based控制器與PLC已共存於市場,一套自動化系統中,不太可能像以往只選擇使用PLC作為控制核心,而是兩者均用,在單純控制以PLC為主,若有分析資料、網路、統計等需求,則由PC Based 控制器負責,PLC與PC Based控制器兩者在一套大型系統中的應用比例約為7:3。
界線逐漸模糊 PC與PLC有機會並肩合作
PC Pased控制器將電腦強大的資料處理和網路能力、使用者介面及程式設計環境,整合傳統PLC的高可靠性、強抗干擾能力、組合靈活、故障查找方便等特點,通過軟體的方式,來實現傳統PLC的PID控制、離散控制和模擬控制等功能。
在過去關於PLC和PC Based的控制系統二者間相較,孰優孰劣的辯論的確相當激烈。在推出近半世紀,PLC已經發展至包含類比I/O、網路通訊,以及像是IEC 61131-3的程式標準,但工程師亦利用數位I/O、類比I/O點等,以及簡單的程式設計技術,創造出百分之八十的工業應用程式。因此可以說,PLC與PC Based控制器的界線,的確是愈來愈模糊。
此外,由於PLC等自動化元件多必須與整體自動化系統搭配,一部份零配件效能的大幅提昇,未必是整體系統的同等提昇,必須有其他週邊零配件的支援才會有效果,因此使用者必須從整體系統面來評估,才不會陷入見樹不見林的盲點。不論是PLC或是PC Based控制器,其選擇仍應依最適化原則來進行規劃,並不是只選其一就能勝任。在當今或未來的工廠自動化環境中,PLC和PC Based控制器均有其特點;甚至在很多情況下,自動化控制過程將同時包含離散和程序控制,因而 PLC與PC Based控制器將有機會並肩合作。
這意味著什麼?這代表當問及「PLC或PC在工業控制中誰會更為出色?」時,合理的回答是,「都很優秀」。
智慧工廠打造第四波工業革命
整合平台及軟硬體的共同發展,讓系統整合製造更加完整;讓工廠精確地管理原料、製程及產品,不但能夠因此降低成本,此外亦能提升效能。製造的智慧化,讓製程更加精確,亦確立了工廠自動化的新型態,向「智慧工廠」邁進。
近年來,製造業面臨的競爭日趨激烈,消費者的胃口瞬息萬變,造成產品生命週期愈來愈短,客製化產品日趨多樣,製造成本亦跟著難以控制;此外,更加複雜的其他因素變項,使得廠商必須隨時面對不穩定的訂單、少量多樣的生產、生產良率的控制,以及備料庫存壓力等相關問題,從中尋求一個能夠同時提升生產力及競爭力的關鍵策略,成為廠商有志一同的關切方向。
「智慧工廠」的發展,為廠商提出了新的方向。包括清楚掌握產銷流程、提高生產過程的可控性、減少生產線上人工的干預、即時正確地蒐集生產線數據,以及合理的生產計畫編排與生產進度等,都是業者提升競爭力及生產力所必須掌握的關鍵項目。
環顧工廠製造的發展歷程,早期主要是讓「人」來照顧機台;在自動化導入後,雖然建立大量標準化規則,並透過程式系統加以控制加工生產,但仍然需要「人」監視機台,製程資訊亦需要透過人工抄寫,統計資訊內容亦不甚完整。
一直到整合平台、軟體、硬體及機台的共同發展,逐漸形成「智慧工廠」概念,才使得廠商從單純的製造業,成為「服務型」的創新產業。
智慧工廠技術 來自人工智慧研究
製造領域的智慧化,源自於「人工智慧」的研究。自1980年代起,人工智慧被引進製造領域,製造業各種智慧化的機械、製程以及系統等技術興起,智慧製造技術尤其更加多元;此外,近年來包括系統平台、軟體技術、感測系統及網際通訊等技術的突飛猛進,讓智慧製造系統更加強大,甚至能跨越地域限制的遠端控制,都是智慧工廠的技術展現。
不可諱言,製造的全程中實現「完全的」智慧化,雖然並非完全做不到的事情,但現在的技術的確有些難度,只能期待遙遠的將來。但這類早期用於高科技的智慧製程技術,是否可以用於傳統產業的發展,這個傳統以來多是勞力密集化的產業,是否也可以透過相關技術來完成「製造智慧化」,乃至於智慧工廠?
回顧過去的製造系統演變,不難發現是常需求的改變及新技術的引進,成為改變製造系統型態的主要驅動力。1970年代之前盛行「專用製造系統」,強調快速有效率生產單一產品,以滿足市場的需求;但隨著生產技術的進步,產品的生命週期隨之縮短,傳統的專業製造系統無法滿足市場改變的腳步,於是在1980年代衍生出可程式化及多功能的「彈性製造系統」作為替代,使產品型態改變時,控制者仍可透過程式化介面,調整系統的功能。
在1980至1990年代,製造系統建構的重點,從快速製造轉換為「提升品質」及「降低成本」,這類思考也導致後來「精實製造」及「敏捷製造」蔚為主流;前者指製造活動所需資源減低,後者更進一步將企業組織與產品型態變動鎔為一體。1983年,人工智慧被帶入製造業,成為工廠自動化的起源,至此之後製造系統智慧化的腳步,就一直沒有斷過。
智慧製造的目標,簡單來說,即是將人工智慧融入製造過程的所有環節中,系統直接可以自動監測生產線運作過程,亦可自動調整、自動組織,甚至「最佳化」在製程中整合設計、加工、控制及管理等過程,以適應外界或內部的變化環境。
1989年,日本提出「智慧化製造系統」國際合作計畫,從1992至1994年進行可行性研究,建立六項工業界主導的「可行性國際合作測試案例」,包括《流程工業潔淨製造》、《全球化製造同步工程》、《21世紀全球化製造》、《全方位製造系統》、《快速產品開發》、《知識系統化》等智慧系統;此後經過10年的努力,包括日、美、加、澳、歐盟、挪威、瑞士及南韓等七大地區工業界、學術界及研究單位發展出的智慧製造技術的共通平台,以及21項研究計畫,可將智慧製造系統大致歸納下列五項特徵:
一、系統具有自主能力:可蒐集與理解外界及自身的資訊,並以之分析判及規劃自身行為。
二、整體可視技術的實踐:結合訊號處理、推理預測、仿真及多媒體技術,將實境擴增展示現實生活中的設計與製造過程。
三、協調、重組及擴充特性:系統中各組承擔為可依據工作任務,自行組成最佳系統結構。
四、自我學習及維護能力:透過系統自我學習功能,在製造過程中落實資料庫補充、更新,及自動執行故障診斷,並具備對故障排除與維護,或通知對的系統執行的能力。
五、人機共存的系統:人機之間具備互相協調合作關係,各自在不同層次之間相輔相成。
從智慧製造到智慧工廠,基本上系統的發展均依照這五項特徵為基礎,作為後續變化的支撐,而這些特徵,也成為工廠自動化的重要特色重點。
解決人力需求 系統整合讓製造更智慧
既然談到「智慧」,工廠「自動化」的系統絕對是其中重要的角色。
「製造智慧化」之所以蔚為風潮,主要的原因在於原物料價格飛漲,但產品的價格卻因為競爭激烈價格未跟著上揚,廠商必須設法吸納因原物料上漲所增加的成本負擔;因此,讓工廠精確控制原料、製程及產品,不但能夠因此降低成本,此外亦能提升效能,製造的「智慧化」便成為工廠自動化的當務之急。
另外,製造的智慧化亦是因應產能效率,以及人力成本等問題的解決方案。早期的台灣製造商,面對逐漸高昂的人力成本,多以轉向人力成本較低的大陸做為生產製造基地;但在近年來,隨著大陸經濟轉型,人力成本也成為下一階段的新負擔。在大陸的廠商必須重新佈局設點,或轉向內地,或出走他國,而仍留在台灣的製造業廠商,也同時再次面臨著人口結構的改變。
對智慧化的更高期盼
除了基層勞動力外,技術勞工的短缺也是相同的困境;不論任何地區,均促使產業界對生產自動化與智慧化的更高度期盼。
因應人力成本所衍生出的「智慧製造」,指的是透過智慧機器與「人」所共同組成的「人機一體化」系統,製造系統在製程中,協助「人」進行分析、推理、判斷、構思及決策等活動,通過人與智慧機器的合作,系統的功能再次延伸,取代人類在製造過程中原有的部份勞動與腦力,如此一來,「智慧製造」再次更新了製造自動化概念。
目前來看,「智慧工廠」概念仍眾說紛紜,如果就業界的產品布局來看,仍可歸納出一個共通定義,新概念工廠「智慧化」,主要可以包含「製程管控可視化」、「系統監管全方位」及「製造綠色化」三層面。
從「製程管控可視化」來看,由於智慧工廠高度的整合性,在產品製程上,包括原料管控及流程,均可直接即時展示於控制者眼前,讓控制者得以全盤掌握製程的現況,同時系統機具的現況亦可即時掌握,讓控制者得以進行在控管製程的同時,減少因系統故障造成偏差。
此外,製程中的相關數據均可保留在資料庫中,讓管理者得以有完整資訊進行後續規劃,也可以依生產線系統的現況規劃機具的維護;也因為資訊的整合,以之建立產品製造的「智慧組合」。
「系統監管全方位」部份,由於智慧製造的設備,必須具有感知能力,以感測器做連結,系統可進行識別、分析、推理、決策、以及控制功能;這類製造裝備,可以說是先進製造技術、資訊技術和智慧技術的深度結合。
當然此類系統,絕不僅只是在工廠內安裝一個軟體系統而已,主要是透過系統平台「累積知識」的能力,來建立設備資訊及反饋的資料庫。
這不但可掌握產品完成之時程,亦可提供更進一步服務,從訂單開始,到產品製造完成、入庫的生產製程資訊,都可在資料庫中一目了然;此外,在遇到製程異常的狀況,控制者亦可更為迅速反應,以促進更有效的工廠運轉與生產。
在「製造綠色化」方面,除了在製造上利用環保材料、留意污染等問題,並與上下游廠商間,從資源、材料、設計、製造、廢棄物回收到再利用處理,以形成綠色產品生命週期管理的循環,更可透過綠色ICT的加值應用,延伸至綠色供應鏈的協同管理、綠色製程管理與智慧環境監控等,協助上下游廠商與客戶之間共同創造符合環保的綠色產品。
從自動化到智慧化
智慧工廠早期多注重在「製程」的智慧化,這主要是來自於高科技產業的快速發展;透過電腦平台系統,直接監控機台及生產線,適合應用在較為精密的產業上;此外像是半導體晶片等相關製程,多需要在極度潔淨的無塵環境工作,「人」的變因反而有可能造成產品製程複雜化,因此「自動化」乃至於「智慧製造」成為這類高科技廠商的最佳選擇。
因此,從系統架構來看,智慧製造可以將整個系統分為「全方位製造系統」、「可重組智慧系統」以及「智慧化維護系統」三個組合。
毫無疑問,智慧製造的確是自動化的未來發展方向。在製造過程的各個環節,幾乎都可廣泛應用人工智慧技術,像是專家系統可以用於工程設計、工藝過程設計、生產調度,以及故障診斷等技術;亦可將神經網路和模糊控制技術等先進技術,應用於產品配方、生產調度等流程,實現製程智慧化。