人類之歷史最早係由各種燃料燃燒釋放出來的光與熱來滿足照明需求,隨著愛迪生在1879年首次展示以鎢絲燈泡為電極之白熾光源後,照明設備不斷推陳出新;如螢光燈、金屬鹵化燈與鹵素燈等等,皆是為了滿足人們的要求,如同一句口號—科技始終來自人性。由於世界各國對於綠色能源的日益重視,佔據超過20%以上電源消耗的照明系統,也逐漸成為重要課題。傳統白熾燈光源轉換效能過低,世界各國早已明定禁用時程,預計於2012年到2014年會逐漸被淘汰;而其他發光源則因或多或少含有有害物質,也讓環保意識高漲的現今社會開始尋求其他新興照明光源。自從1960年代後期發光二極體(LED)固態照明發展以來,隨著發光效率的不斷提升,LED先天上省電、壽命長、反應時間快、環保以及固態元件耐震動之優勢,逐漸讓LED嶄露頭角,取代市面上的各種發光源。
雖說LED發光效應較其他發光源為高,仍是有約80%以上的能量會轉成熱能消散。尤其隨著發光功率提升、以及超高亮度LED應用之需求,高功率LED以及串接式LED亦應運而生,尤其LED具有半導體之特性,其產生之廢熱對於LED之壽命、發光特性,都有著舉足輕重之影響。以往LED發光產品之功率要求較低,但為拓展其應用層面至如室外照明、大尺寸背光模組以及車前燈照明等有著超高亮度需求,或是散熱環境嚴苛之產品;LED之熱管理必定成為未來發展相關產業的技術門檻之ㄧ。
LED溫度量測
誠如前文所述,LED之廢熱消散機制,將會繼LED發光效益、封裝、驅動IC控制之後,成為未來主導LED照明商品之重要課題;如何準確量得LED之溫度,便成為熱管理的首要目標。本節將為各位介紹,如何精準量到LED之接面溫度。
LED發光效應
要得到準確的LED發熱溫度,首先便要先了解LED之發光原理。LED主要是利用二極體之p-n接面(p-n junction)結構,施加一順向偏壓,驅動N型半導體中電子與P型半導體之電洞於接面結合時,部分能量轉為光能,其餘能量則產生聲子造成接面結構震動,最終轉成熱能型式釋放,如圖一所示。
LED接面溫度量測
由於LED晶粒尺寸相當小,欲直接量測其接面溫度實屬不易。不管是以熱電偶貼附方式量測,亦或是採用紅外線熱顯像儀直接照射,都由於空間解析度不足而產生相當大之誤差。目前一般多是採用半導體之熱特性,亦即其順向偏壓會隨溫度上升而下降,來反推求得接面溫度。在實際操作的時候,通常會先將待測元件放置於一溫控環境下,待其達到穩態,量測該溫度下之順向電壓值。反覆在不同溫度下操作,以求得電壓隨溫度上升之遞減曲線。在一般LED操作環境溫度下(10℃~90℃),順向電壓隨溫度遞減呈現線性,其斜率一般稱之溫度敏感參數(TSP),我們則稱其倒數為K因子(K factor),如公式一。
由於LED此一元件量測電壓較量測溫度為易,在已知K因子之先決條件下,只需量測當下之順向電壓,即可由K因子反推求得相應之接面溫度。
坊間大多以此方式求得LED作動時之接面溫度變化,進而求得LED之熱阻值;然而受限於量測機台,多半僅能測得待測元件之整體等效熱阻,欲求得各層熱阻變化並不見得相當精確。本文將介紹LED溫度量測技術,不同於以往只量測接面溫度之變化曲線,取而代之的是以傳熱途徑來詮釋LED內部結構,除可量測待測元件或模組之整體等效熱阻,更可直接且精準量到待測物內部各層之熱阻值。
量測原理與方法
此種新穎之LED溫度量測技術係採用半導體接面溫度量測機台(Thermal Transient Tester;T3Ster)進行量測,其測量LED接面溫度方法與一般順向電壓量測法大同小異,量測符合JEDEC 。但T3Ster可於1微秒(1μs)即啟動量測,一般量測機台大約是在1毫秒(1ms)後才能啟動,若以1毫秒來估算,大約會損失10%~15%的資料量。且最高可於每1微秒紀錄一點數據,每次量測最多可記錄65000筆數據點,訊號雜訊比(SNR)達70dB。
T3Ster量測方式是提供待測元件一功率變化,讓元件產生溫度響應,紀錄由初始條件到溫度變化趨於穩定間,溫度隨時間變化的暫態曲線。除了得到溫昇曲線與整體熱阻外,藉由大量精準的量測數據,配合其演算法,更可了解元件中各層結構之熱阻與熱容。
簡單的說,T3Ster在演算過程中就是以電子學中常見之RC系統來模擬LED內部之熱傳遞途徑,以熱阻取代電阻、熱容取代電容。利用NID演算法,將量測所得之熱響應函數或熱阻抗函數微分後,加以反摺積得到時域頻譜,離散化後再轉換成結構函數;結構函數橫軸為熱阻,縱軸為熱容值,其與一般常見之熱特性曲線大相逕庭,圖二為T3Ster量測資料之演算流程。
我們可將結構函數之橫軸、縱軸分別看成熱在結構中行進時,所歷經之總熱阻與熱容。以下採一均質柱體來解釋,如圖三所示。
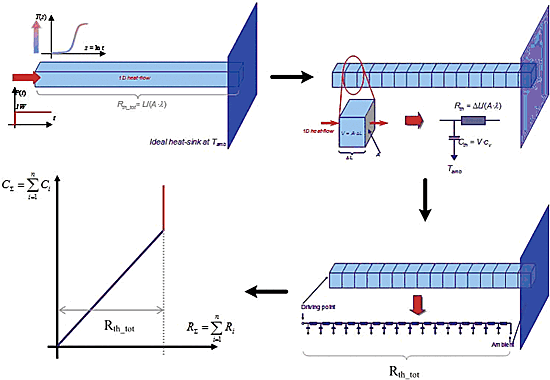
《圖三 Compact model for explaining structure function》 |
|
圖四左上有一熱源自柱體左端傳入,右端為一理想熱沉(heat sink),將此柱體視為由許多小單元所組成,每一單元之體積為V=A˙ΔL,單元熱阻Rth=ΔL /(A˙λ),單元熱容Cth=V˙Cν。當結構內部之熱容Cν、熱傳導係數λ或截面積A產生變化時,其斜率就會改變;換句話說,若結構內Cν、λ、A皆不變時(通常代表熱通過相同物質且其幾何條件相等),斜率保持不變,如圖四所示。
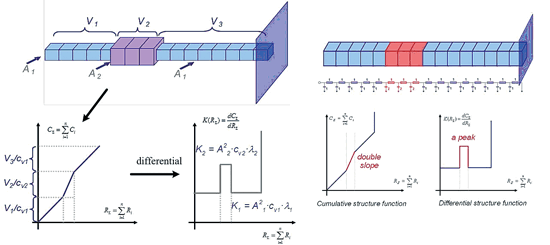
《圖四 結構函數變化:圖(a)代表結構截面積改變,圖(b)代表結構熱容變化》 |
|
由圖四可明顯看出,當熱在結構中行進時,若遭遇同樣大小之相同材質,其熱阻與熱容增加趨勢保持恆定,一旦進入結構或材質發生變化之處,其結構函數即會出現轉折。結構函數之最大優勢,便是可直觀判斷LED封裝結構之變化,進而讀出相應熱阻熱容值,這是在一般常見的溫昇曲線中所無法得知的。
圖六為兩個不同物體測量所得之溫昇曲線與結構函數曲線比較。圖五(a)為待測物之溫昇曲線,在圖形中可看出,雖然兩待測物在結構中間有所不同,但在整體溫度變化曲線卻不會因此結構改變而有太大變化。相反地,若是採用結構函數曲線來比較二者差異,則可馬上看出兩者之不同點,如圖五(b)。
實際量測結果
由前文敘述可知,結構函數對於吾人了解LED內部各組成之特性有相當大的幫助,尤其是在封裝完成後之LED非破壞性檢測應用上;接下來就介紹LED的實際量測案例,圖六為實際LED量測時之實驗架設示意圖。量測系統僅需以RS232與USB傳輸介面,即可連結量測系統與個人電腦。
今以Lumileds之Luxeon系列產品進行LED熱阻實際量測,其LED內部結構如圖七所示。此待測LED為一般常見之LED結構,其結構層分別為,氮化鎵LED晶片、錫球陣列、矽質鑲嵌晶片、散熱銅座以及鋁基板MCPCB;量測進行時,會再將此LED元件放置於一散熱模組或溫控元件上。後續量測資料將會以微分後之結構函數方式呈現,以此方式可快速判讀結構函數之斜率變化,協助了解LED各層內部熱阻狀況。
圖八則為此待測LED之微分結構函數圖形。圖形由左至右為LED內部熱傳導途徑,由原點的PN接面開始,直到最右端之大氣環境,此圖以不同顏色區分各層結構。
T3Ster除了量測LED模組之整體熱阻外,其與一般量測最大之差異就在於內部結構熱阻之量測。之所以能夠處理內部熱阻之量測,主要就是在於暫態量測時之快速啟動量測,以及大量的量測數據供作後續之訊號處理。圖九則分別以不同之量測參數比較其結果差異,由圖中可明顯看出,當量測啟動於44微秒時,兩者之整體熱阻值RthJC與RthJB並無太大之差異,但在結構內部之量測結果,44微秒所得之量測解析度明顯較啟動於15微秒要差;且約有3%的資料量在最初量測階段無法測得。
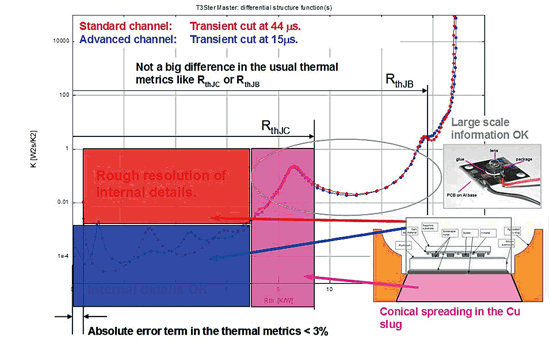
《圖九 不同量測解析度之結果比較(44μs與15μs)》 |
|
然而一般LED或接面溫度量測系統則多半僅能於一毫秒後啟動量測,接下來便實際以1ms的量測條件來與之作比較。圖十左上角為熱阻隨量測時間變化圖,橫軸為時間變化以對數方式表現,縱軸則為熱阻變化量。若量測於1毫秒後啟動,整體熱阻值大約會有2K/W的誤差產生。以微分結構函數比較,更可明顯看出其差異,LED內部結構在散熱銅座之前之熱阻資料幾乎完全無法判讀,甚至在散熱銅座之熱阻值也很難加以定義。
LED散熱模擬
LED之熱阻主要可以封裝端作一分野,分為內部熱阻與外部熱阻,內部熱阻的問題多半是受LED材料本身以及封裝方式所影響;外部熱阻問題則可外加散熱模組來加以解決。以過在作LED之熱傳模擬分析時,無法確切得到各層熱阻,且LED量測得到之整體熱阻亦不見得準確,其模擬結果的準確度有待商議。而今可利用上述T3Ster量測方法求得正確之LED各層結構熱阻,作為模擬分析時之依據,本節就介紹封裝端與LED照明模組端的熱模擬分析。
如圖十一所示,在以T3Ster量測後可得到LED各層結構熱阻與整體熱阻值,前者可協助使用者在模擬時建立LED細部模型,針對LED封裝等級進行熱分析。而整體熱阻值則可在模組端之熱分析模擬時,建立簡化之LED模型,此時使用者所在意的應是後段散熱模組之設計,故採用簡化模型可針對後段散熱模組加以分析。
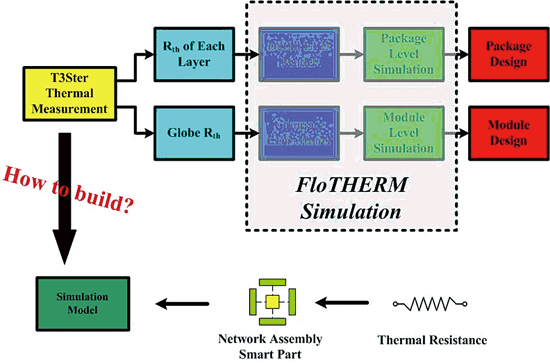
《圖十一 LED封裝等級與模組等及散熱模擬示意圖》 |
|
本文所採用的是計算流體力學模擬軟體FloTHERM,此軟體有內建快速建模零組件,可輸入T3Ster量測結果,作為元件之材料熱特性參數。
此快速建模零組件主要是將待模擬之元件,以立方體型式建立,並指定該元件與其他接觸面之節點,利用T3Ster量測結果,定義節點間之熱阻值。以此方式去建立LED內部各層結構,包含LED晶片、錫凸塊、矽基座與散熱底座等等。當操作簡化模型時,可將上述結構整合成單一立方體,並輸入LED模組整體熱阻值。
圖十二(a)為LED以CAD軟體繪製完成之圖形,透過簡單的轉檔,即可將此CAD模型轉成FloTHERM模擬模型,如圖十二(b)。本次模型之建置係模擬LED於T3Ster量測過程中之狀況,LED固定於鋁基電路板上,再將此待測LED放置於一理想散熱平板上。LED功率1watt,折減因子為0.8,再經過簡單的設定即可模擬出LED之溫度分布狀況與其流場情形,如圖十二(c)、十二(d)。
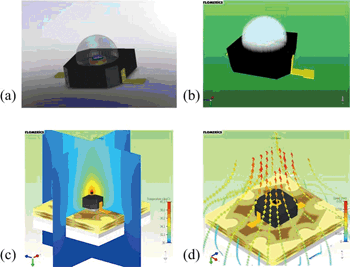
《圖十二 LED模擬狀況:(a)LED CAD模型,(b)數值模擬模型,(c)模擬後之LED溫度分佈,(d)流場分佈圖》 |
|
結語
隨著LED市場的蓬勃發展,高功率與高亮度LED之開發勢在必行,高功率所伴隨而來的熱問題將會影響LED之使用壽命、光學演色性以及LED整體可靠度。如何有效解決熱問題,將會在LED未來的發展歷程上,扮演相當重要的角色。已過採用紅外線熱顯像儀與熱電偶貼附的方式量測LED接面溫度,並無法量到準確之接面溫度。欲解決LED熱問題,勢必要先了解其內部熱阻結構;而T3Ster正可解決此一問題,完整描述其內部結構各層熱阻,進而配合電腦輔助分析之觀念,模擬其熱特性,探討不同封裝方式與後段散熱模組設計對於LED解熱的影響。期待在LED設計初期,便可了解其熱特性,藉此變更設計案,加速LED研發設計之流程,提高競爭力。
---作者任職於勢流科技---