影像感測器、光學鏡片及影像處理器,是數位相機擷取影像的三個基本元件。光線進入光學鏡片後,被傳送到影像感測器並轉換成電子訊號,再由影像處理器將電子訊號轉換成標準格式。
影像感測器與影像處理器是透過半導體技術製造而成,這些元件的製程是在晶圓層級階段完成,因此,廠商能藉由大量生產來降低製造成本。另一方面,傳統的光學元件則是利用標準的塑膠模製或玻璃研磨技術,以小批量循序的模式來生產。大多數用來製造手機相機模組的光學元件,都採用不耐高溫的塑膠原料所製。因此,這些相機模組必須先組裝在可撓式纜線(flex lead)或插座,再安裝至電路板上。由於相機模組必須與手機基板上的其他IC元件分開組裝, 使得所需的材料增加,造成額外的人力負擔與製造週期的延長,最後導致總體成本的上升。隨著影像感測器的尺寸持續變小,光學鏡片的面積也必須跟著縮減。但由於製造的高複雜性,若運用傳統技術降低光學元件尺寸,將會導致成本提高。為降低尺寸與成本,新的光學元件製造技術便應運而生,這種技術就是晶圓層級光學元件(wafer-level optics)。
晶圓級相機技術
在各種製造方法中,業者大都偏愛運用平行製程,透過大量的元件產出來分擔製造成本,而Tessera的OptiML晶圓級相機(Wafer-Level Camera)技術也是以此為基礎的技術。運用標準半導體技術及耐迴焊(reflow-compatible)的材料,能在單片晶圓上同時製造出數以千計的鏡片,接著再運用晶圓堆疊技術,將數個光學晶圓進行對校準與接合。接合的光學晶圓被切割成許多單一的整合光學鏡片後,便可安裝到影像感測器上。
運用這種晶圓級製程,光學鏡片的尺寸可縮減到和影像感測器相同的尺寸,同時相機模組所需的元件數量也能降低。此外,這種方式不需要人工調校光學元件的焦距。圖二中兩種傳統VGA相機模組與晶圓級VGA相機模組的比較,可明顯看出尺寸上的差異。
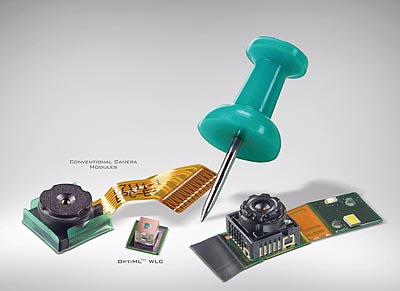
《圖一 OptiML VGA相機與兩種傳統VGA相機模組的尺寸比較》 |
|
在大多數的相機模組中,影像感測器是材料中最昂貴的元件。由於感測器是在晶圓階段完成,許多製造商正嘗試讓每片晶圓達到最佳的產量,藉以降低每個單一零件的平均成本。為達成這項目標,半導體技術開始轉移至越來越小的節點,藉以製造出更小的元件。在2004年時,典型VGA影像感測器佔用的電路板面積約為16mm2,像素尺寸為5.5um。現在相同的VGA影像感測器,底面積僅四分之一不到,像素尺寸更縮小到2.2um以下。CMOS節點也從350nm縮小至130nm。未來像素尺寸將繼續縮小至1.5um以下。
因應影像感測器的尺寸的繼續縮減,光學元件也必須大幅縮小。然而,傳統元件是在元件層級進行製造,因此要縮小尺寸極為困難,更無法降低製造成本。在許多情況中,降低尺寸往往導致成本提升,原因在於製造的困難度增加,導致良率下滑,而WLC技術是一種真正晶圓級技術,因此可以解決這方面的難題。縮小光學元件的尺寸,事實上就增加了每片晶圓所產出的鏡片數量,進而降低每個鏡片的成本。因此,運用WLC技術來製造光學元件,讓光學鏡片技術能搭上半導體產業發展的順風車,隨著像素尺寸與CMOS節點環境的持續縮小,發揮各方面的成本好處。
目前OptiML晶圓級相機技術所適用解析度範圍,涵蓋從VGA等級到百萬像素以上範圍。運用影像強化技術,三百萬像素解析度以上的相機,則可以在拍攝五十公分之內距離的物體時,強化對焦效果。
晶圓級相機製程
晶圓級相機技術運用各種半導體科技,在單片晶圓上一次製造出數千個鏡片,這些鏡片是利用傳統的微影、蝕刻及複製技術來製造。
根據相機模組的性能要求,設計晶圓級的鏡片並製造出最終光學組件所需的晶圓數量。在製造出所有鏡片晶圓後,再利用晶圓堆疊技術讓這些晶圓進行校準與接合,製成一疊晶圓光學元件陣列。(如圖三)
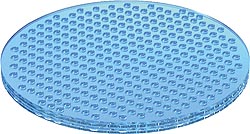
《圖三 OptiML 晶圓堆疊(WaferStack)技術帶來了晶圓級鏡片模組》 |
|
接著堆疊的晶圓被切割成光學元件(圖四)。利用這項技術,光學堆疊內的鏡片會固定在精確的位置,不需用到昂貴且影響良率的人工對焦。然後,完整的光學鏡片模組即可安裝至影像感測器上,構成相機模組。
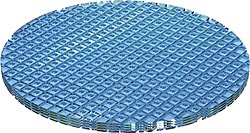
《圖四 堆疊的晶圓切割成許多光學鏡片模組(示意圖)》 |
|
如前所述,用來製造這些晶圓級鏡片的材料可承受迴焊的高溫,讓製造商能運用標準的回焊技術來組裝手機中的相機模組。此外,運用MVP技術來封裝影像感測器,還能進一步強化耐迴焊所帶來的成本效益。利用這項技術,影像感測器從初期的製程階段便被封裝在外層的玻璃中。電子接點配置在矽元件的背面,連結至焊點。
根據Prismark的報告預估,在2011年將有至少50%的影像感測器,採用晶片級封裝技術。
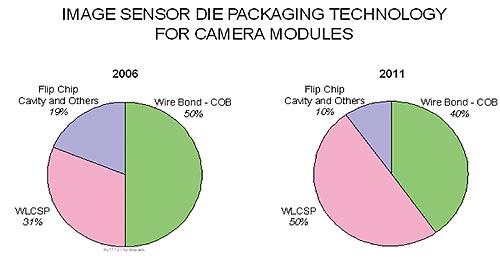
《圖六 影像感測器封裝技術的市場趨勢》 | 資料來源:Prismark |
|
把晶圓級光學鏡片模組置於晶片級封裝感測器上(圖七),建構出真正晶片級的相機模組,再透過一般IC所使用的標準迴焊製程,便能直接裝在手機的電路板上。
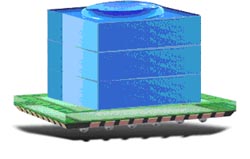
《圖七 WLC光學鏡片模組裝配在SHELLCASE 封裝的感測器上。》 |
|
以下影像是利用業界的照相手機及晶圓級相機所分別拍攝,從比較圖中可看出模組尺寸大幅縮小,材料成本也降低;此外,利用晶圓級相機技術所產生的影像,品質和其他影像亦不相上下。
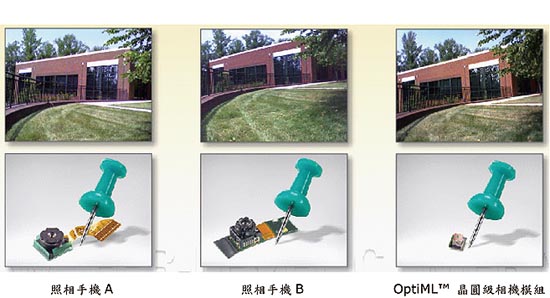
《圖八 兩種傳統照相手機與WLC照相手機之模組與拍攝影像比較》 |
|
影像強化技術
延長景深(EDoF,Extend Depth of Field)以及低光源拍攝功能,是照相手機廠商引頸企盼的兩項熱門功能,採用制動器的傳統自動對焦解決方案,其性能確實勝過定焦相機,但同時也存在許多缺點,包括成本昂貴、難以小型化、使用次數有限,以及受限於機械零件的磨損,導致無法符合嚴苛的光學誤差容許等,因此僅能提供有限的景深,且拍攝時須等候相當久的時間,才能達到穩定的對焦設定。而Tessera運用專利的OptiML Focus技術,從前景到背景的影像都維持清晰銳利,無須使用可動的零件,仍能提供更高的影像品質,勝過現有的定焦解決方案。
OptiML Focus技術結合鏡片設計以及小型化的數位演算法,得到對焦銳利的影像,以及優異的低光源拍攝功能。演算法能建置在硬體或軟體,整合至感測器、影像處理器、應用處理器,或是以離線的模式來執行。
現今的數位相機通常無法兼具景深對焦與低光源拍攝效能。但運用OptiML Focus技術,相機模組能同時擁有這兩種功能,提供景深效果以及高品質的低光源拍攝功能。圖十顯示OptiML Focus技術在拍攝近距離與遠距離物體的效果。
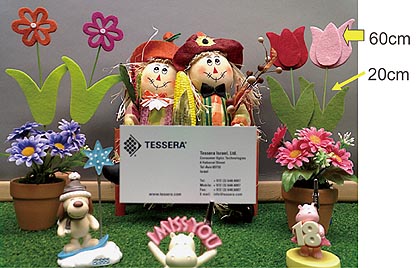
《圖九 OptiML Focus技術可確保從前景到背景皆清晰銳利的影像,》 |
|
完全沒有用到可動的零件
關鍵在於垂直整合
傳統相機模組都是由模組製造商來生產,在大多數情況下,這些模組製造商會從不同供應商購買相機零組件:半導體廠商提供影像感測器與影像處理器、鏡片製造商提供光學元件等。因此,模組製造商必須承擔每家供應商的成本。
為降低相機模組的成本,讓相機能夠整合到超低階的手機,所有元件的價格都必須兼顧,為了達成這項目標,業界已經著手針對模組製造商提高垂直整合度,例如,模組製造商除了光學元件外,也生產矽感測器晶圓,這將能降低每個元件的成本,最終達成降低相機模組的整體成本。預料這樣的垂直整合,在未來數年將出現在半導體產業。
(作者為Tessera台灣區總經理暨東亞區總監)
參考資料:
Market Breakdown of Camera Phone – 2nd Half 2006 & 1st Half 2007 Forecast, TSR May 2007
CCD/CMOS Area Image Sensor Market Analysis, TSR March 2004
Prismark