前言
英飛凌科技將一項任務交給位於德國慕尼黑的「汽車系統工程」(Automotive System Engineering)組:開發一部電動車(E-Cart)。這台車可開上路,用以展示油電混合車的電氣功能,車子的動力來自一具大型的鋰離子(Li-ion)電池槽(battery stack)。我們立刻發現,電荷平衡(charge balancing)的電池管理有其必要,最簡單的傳統解決方案是利用充電等化(charge equalization)的耗散功率(dissipating power),這種方式勢必要以電池之間的有實功率(active energy)轉移取代。搜尋現有文獻後徒勞無功,目前只發表過相關基本原理。於是團隊決定自行開發專業知識,結果發現在材料成本上,主動系統(active system)比被動的解決方案效能更佳,如圖一所示。
電池系統架構
鎳鎘電池及其後繼產品,鎳金屬氫化物電池的技術已廣泛使用多年,近來全新的鋰離子電池進入市場,由於效能明顯提升,市占率也急速竄升之中。鋰離子電池的能量儲存容量十分驚人,不過,單憑這樣一顆電池的容量,並不足以供應一台油電混合車的使用,電壓及電流都太低了。要增加電流的能力,必須將電池並聯;要求得更高的電壓,則必須將電池串聯。
電池組裝廠通常以簡寫的方式,例如「3 P 50 S」,來說明電池的配置,意思是3個電池並聯,50個電池串聯。
許多顆電池以串聯進行電池管理時,模組化架構的方式較佳,例如,多達12個串聯連接的電池,以3 P12 S的陣列,組合成一個電池塊(block)。這些電池靠著一個內含微控制器為核心的電子電路,進行管理與平衡。
電池塊的輸出電壓與串聯電池的數量,以及電池的電壓有關。典型的鋰離子電池電壓介於3.3V與3.6V之間,亦即電池塊的電壓會介於30V及45V之間,而油電混合車在駕駛時所需的直流供應電壓,則需要450V左右。為了補償電池在充電狀態時的電壓變化,可在電池槽及馬達驅動系統之間,加入一個DC-DC轉換器做適當的連結,這個轉換器也能同時限制電流。
為了讓DC-DC轉換器的運作最佳化,需要150V至300V的堆疊電壓(stack voltage);因此,必須將5到8個電池塊串聯起來。
平衡的必要性
若超出容許電壓範圍之外,如圖二所示,鋰離子電池很容易受損,如果超出電壓的上下限(以納磷酸鹽型為例,分別為2V及3.6V),電池便會嚴重損壞,無法復原,最後至少會擴大自我放電的速率。在寬廣的「剩餘電量」(State-Of-Charge;SOC)範圍中,輸出電壓是穩定的,偏離安全區的風險並不高。然而,在安全區的開端及尾端,曲線異常陡峭,為了防範於未然,必須謹慎監控電壓。
如果電壓達到臨界值,放電或充電程序就必須立即停止。靠著強大的平衡電路,受影響的電池能將電壓控制在安全區域內。要做到這點,電池槽中任何一個電池的電壓若開始與其他電池不同,能量就必須在電池之間移動。
電荷平衡
傳統的被動方法
常見的電池管理系統中,每個電池都透過一個開關連接至負載電阻,在這樣的被動電路裡,可個別選定電池進行放電。此方法僅適用於充電模式,以抑制電力最強的電池電壓上升。為了限制耗散的功率,使用在100mA區域的小電流,導致平衡時間長達數小時之久。
主動平衡
現有文獻中,可找到許多主動平衡的方法。移動能量需要一個儲存元件,若使用電容,會需要一個大型陣列的切換元件,以便將儲存電容連結至任一電池上;將能量儲存在磁場中,便相對有效多了。這個電路的關鍵零組件是一個變壓器,英飛凌團隊與VOGT Electronic Components GmbH共同合作,開發出一款原型產品。用途包括:
‧@內標:在電池中移動能量。
‧@內標:多路傳輸單一電池的電壓至「接地電壓式」(ground-voltage-based)的「類比數位轉換器」(Analog-to-Digital-Conversion;ADC)輸入,
整個結構的原理就在返馳式轉換器(flyback converter)。此類型的變壓器可將能量儲存在磁場中,磁鐵心內的空氣間隙增加磁阻,以避免磁心材質的磁飽和。
變壓器分為兩側:
‧@內標:一次側連接至整個電池槽。
‧@內標:各個電池則連接至二次側線圈。
一個可用的變壓器模型,可支援多達12個電池,限制的因素在於可能連接的數目。上述的原型變壓器有28支接腳,開關則以OptiMOS3系列的MOSFET為代表。該系列具有極低的導通電阻(on-resistance),因此導通損(conducting loss)可以忽略,如圖三所示。
每個電池塊都用一個現代的8-位元微控制器控制,即英飛凌的XC886CLM,它具有一個快閃程式及一個32-KB的資料記憶體。兩個硬體式的CAN介面,使用低處理器負載的通用型汽車「控制器區域網路」(Controller Area Network;CAN)匯流排通訊協定,支援通訊。一個硬體式的「乘除法單元」(Multiplication and Division Unit;MDU),可加速計算過程。
平衡的方法
可雙向使用的變壓器,依情況可應用在兩種不同方法上。掃描所有電池的電壓之後(稍後有詳細說明),先計算出平均值,然後檢查與平均值相差最大的電池。若該電池的電壓低於平均值,採用下平衡(bottom-balancing)法;若高於平均值,則採用上平衡(top-balancing)轉化。
下平衡
圖四中的例子顯示採用下平衡法的情況,經過確認,2號電池是最弱的電池,必須加以支援。
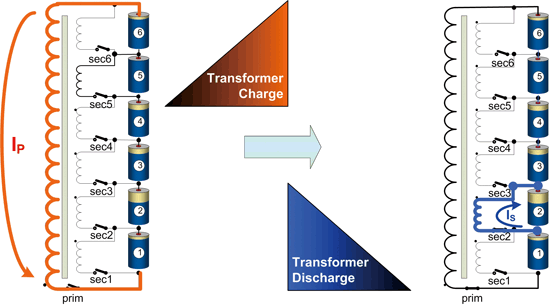
《圖四 下平衡(Bottom-balancing)原理》 |
|
一次測(prim)的開關關閉時,變壓器從電池槽充電;一次側的開關開啟之後,變壓器儲存的能量就能轉移至選定的電池上。在本例中,如果對應的二次側(sec)開關sec2關閉時,即發生此情況。
每個循環週期是由2個主動脈衝及一個暫停所組成,本例之中,40微秒的週期相當於25千赫的頻率。變壓器的設計必須要讓頻率超過20千赫以上,以免在聽頻範圍內出現擾人的哨音,而這個噪音是變壓器內磁鐵心的磁致伸縮(magnetostriction)所造成的。
特別是當電池達到剩餘電量(SOC)的下限時,下平衡法可延長電池槽的操作時間。只要來自電池槽的電流一直低於平衡電流的平均值,就能持續操作車輛,直到最後一顆電池的電力消耗殆盡為止。
上平衡
如果一個電池的電壓高於其他電池,可將能量從該電池抽出,在充電模式下,這個動作絕對有必要。若沒有平衡,充電的程序在第一顆電池充飽時就必須立即停止,平衡可藉由保持相同的電池電壓,避免此情形發生。
圖五的例子顯示出上平衡模式的能量流。掃描過電壓之後,偵測到5號電池是電池槽中電力最強的。開關sec5關閉時,電流從電池流向變壓器,因為電感的關係,電流隨著時間線性升高。電感是變壓器具有的特性,開關的導通時間定義了電流的最大值,從電池流出的能源,即以磁場的形式儲存起來。sec5開啟之後,prim開關必須關閉,變壓器的運轉狀態變成發電機模式,而能量則經由大型的一次側線圈飼入整個電池槽。其電流及時間的條件與下平衡的例子相似,只有順序及電流的方向逆轉過來。
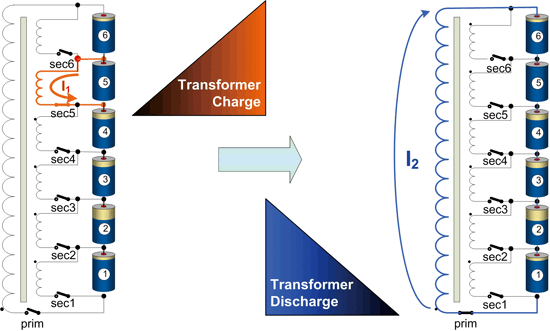
《圖五 上平衡(Top-balancing)原理》 |
|
平衡電力
使用英飛凌E-Cart上的原型組態,可達到5A的平均平衡電流,比起被動式方法,整整高出50倍之多,而且這5A的平衡所造成的整個電池塊的功率耗散,只有大約2W。這不需要特殊的冷卻處理,還可增進系統的能量平衡。
掃描電壓
要管理個別電池的充電狀態,必須先量測個別電壓。只有1號電池是在微控制器的ADC範圍內,因此電池塊其餘電池,沒辦法直接量測到電壓。可使用一陣列的差動放大器(differential amplifier)作為解決方案,而且要能承受整個電池塊的電壓。
只要新增少量的硬體,以下方法便能量測出所有的電壓。以電荷平衡為主要工作的變壓器,也能拿來作為多工器之用,在電壓掃描模式,便不使用變壓器的返馳(flyback)模式。開關S1至SN的其中之一關閉時,連接在一起的電池就將電壓轉換至變壓器的所有線圈上。
只要透過離散濾波器(discrete filter)預處理,就能將量測訊號飼入微控制器的ADC輸入。開關S1至Sn其中之一關閉時所產生的量測脈衝可能非常短,實際的導通時間是4μs,因此,儲存在變壓器內的能量並不多。無論如何,開啟開關後,以磁性儲存的能量皆會經由一次側電晶體,回饋至整個電池塊。因此,電池塊的能量含量並未受到影響,掃描過所有電池一輪以後,系統會返回最初的狀態。
結語
只要利用一套功能優秀的電池管理系統,便能善加利用鋰離子電池的優勢。相較於傳統的被動方法,主動的電荷平衡系統更能提供顯著的絕佳效能。巧妙使用一具簡單的變壓器,就能將物料成本降低。
--作者Werner Rosler,Dipl.-Ing.是德國紐必堡英飛凌科技旗下「安全應用系統工程」(System Engineering for Safety Applications)的系統工程師。